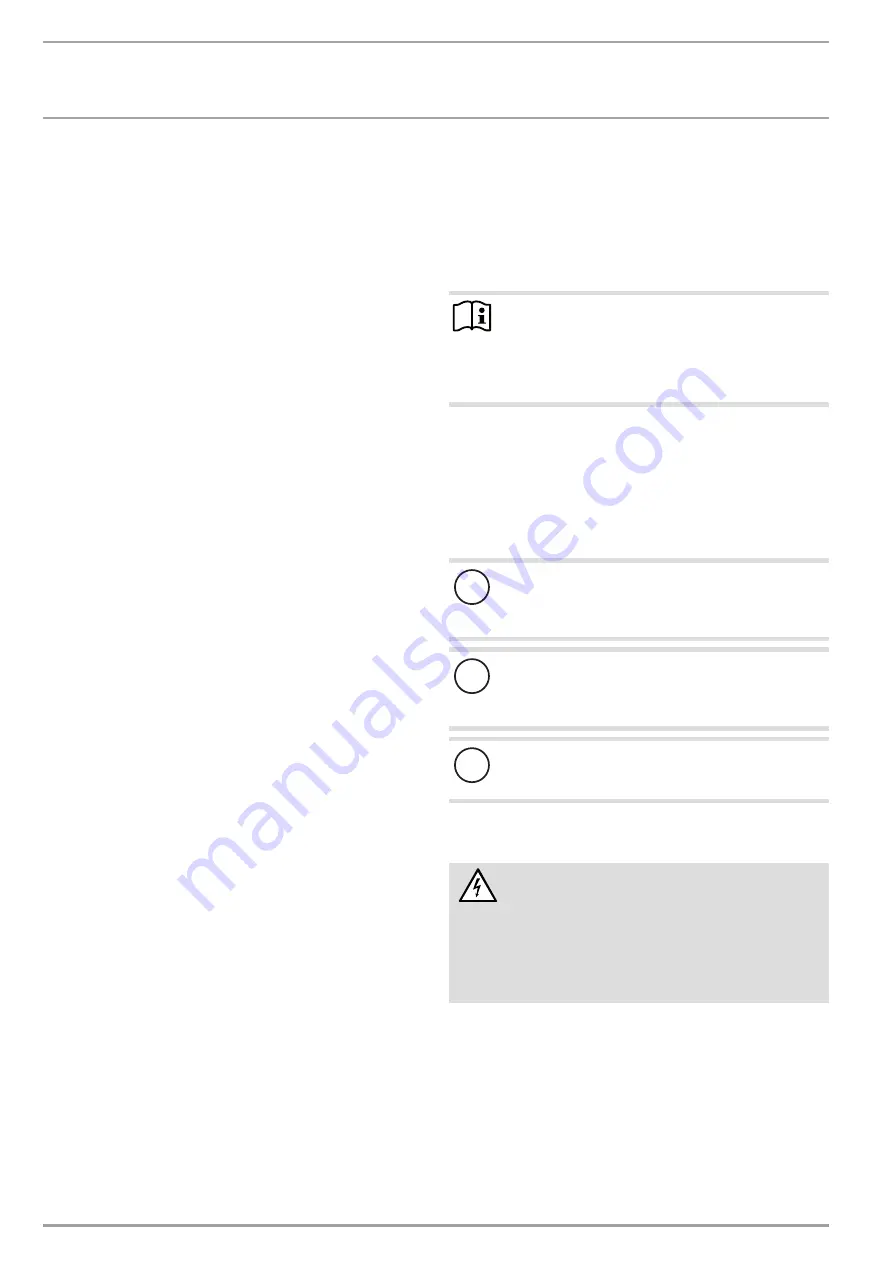
INSTALLATION
Appliance shutdown
60
| WPE-I H 400 Premium
www.stiebel-eltron.com
Compressor
f
f
In the “Manual test” menu, select the compressor test.
f
f
Select the compressor stage to be tested.
f
f
Check that no unusual noises can be heard.
f
f
Check if the hot gas line gets hot.
f
f
Check the other compressor stages.
f
f
Stop the compressor via the menu.
13.2.2 Optional tests
The additional tests displayed in the “Manual test” menu are op-
tional.
13.3 Checking for unusual noises
Under adverse circumstances, supply lines and the way they are
routed can cause noise and vibrations, which are increased at
certain compressor and pump speeds.
f
f
Test the operation of the appliance in heating and DHW mode
across the entire speed range of the compressor and pumps.
f
f
Make sure there are no unusual noises near the appliance
and in other parts of the building.
f
f
If required, install anti-vibration mounts and sound-absorb-
ing pipe clamps near the appliance.
f
f
If the unusual noises continue occurring, you can block or
adjust the problematic speeds of the compressor and the
pumps in the controller.
13.4 Connecting to the internet
The connection required to connect to the internet can be found
behind the front panel below the controller unit.
f
f
Remove the front panel (see chapter “Installation / Removing
the casing parts”).
f
f
Connect a router to the terminal.
f
f
Observe the commissioning instructions for the programming
unit and the operating and installation instructions for the
Internet Service Gateway (ISG).
13.5 Locking commissioning mode
After commissioning, leave the programming unit in safe mode.
f
f
Press the open lock on the screen. Confirm the selection. A
closed lock appears on the left of the menu window.
13.6 Heating curve adjustment during
commissioning
The efficiency of a heat pump decreases as the flow temperature
rises. Therefore adjust the heating curve with care. A heating
curve that is set too high leads to the zone or thermostatic valves
closing and the minimum flow rate required for the heating circuit
may not be achieved.
The following steps will help you to adjust the heating curve cor-
rectly:
f
f
Fully open thermostatic or zone valves in a lead room (e.g.
living room or bathroom).
We do not recommend installing thermostatic or zone valves
in the lead room. Control the temperature for these rooms
via a remote control.
f
f
At different outside temperatures (e.g. -10 °C and +10 °C),
adjust the heating curve so the required temperature is
achieved in the lead room.
13.7 Appliance handover
Explain the appliance function to users and familiarise them with
how it works.
Note
Hand over these operating and installation instructions
to the user for safe-keeping. All information in these
instructions must be closely observed. The instructions
provide information on safety, operation, installation and
maintenance of the appliance.
14. Appliance shutdown
If the system is to be taken out of use, set the programming unit
to standby. This retains the safety functions designed to protect
the system (e.g. frost protection).
There is no need to shut the system down in summer. The pro-
gramming unit has an automatic summer/winter changeover.
!
Material losses
Never interrupt the power supply, even outside the heat-
ing season. The system's active frost protection is not
guaranteed if the power supply is interrupted.
!
Material losses
Observe the temperature application limits and the min-
imum circulation volume on the heat consumer side (see
chapter “Specification / Data table”).
!
Material losses
If the heat pump is completely switched OFF and there is
a risk of frost, drain the system on the water side.
15. Troubleshooting
WARNING Electrocution
f
f
Isolate the appliance from the power supply when
carrying out any work.
Following isolation from the mains supply, parts of the
appliance may remain live. This is because the condens-
ers on the inverter still have to discharge. When the
condensers have discharged, the LEDs on the inverter
stop flashing.
15.1 BM card status display
LEDs are arranged on the BM card (internal heat pump control
unit) which display the current control status.