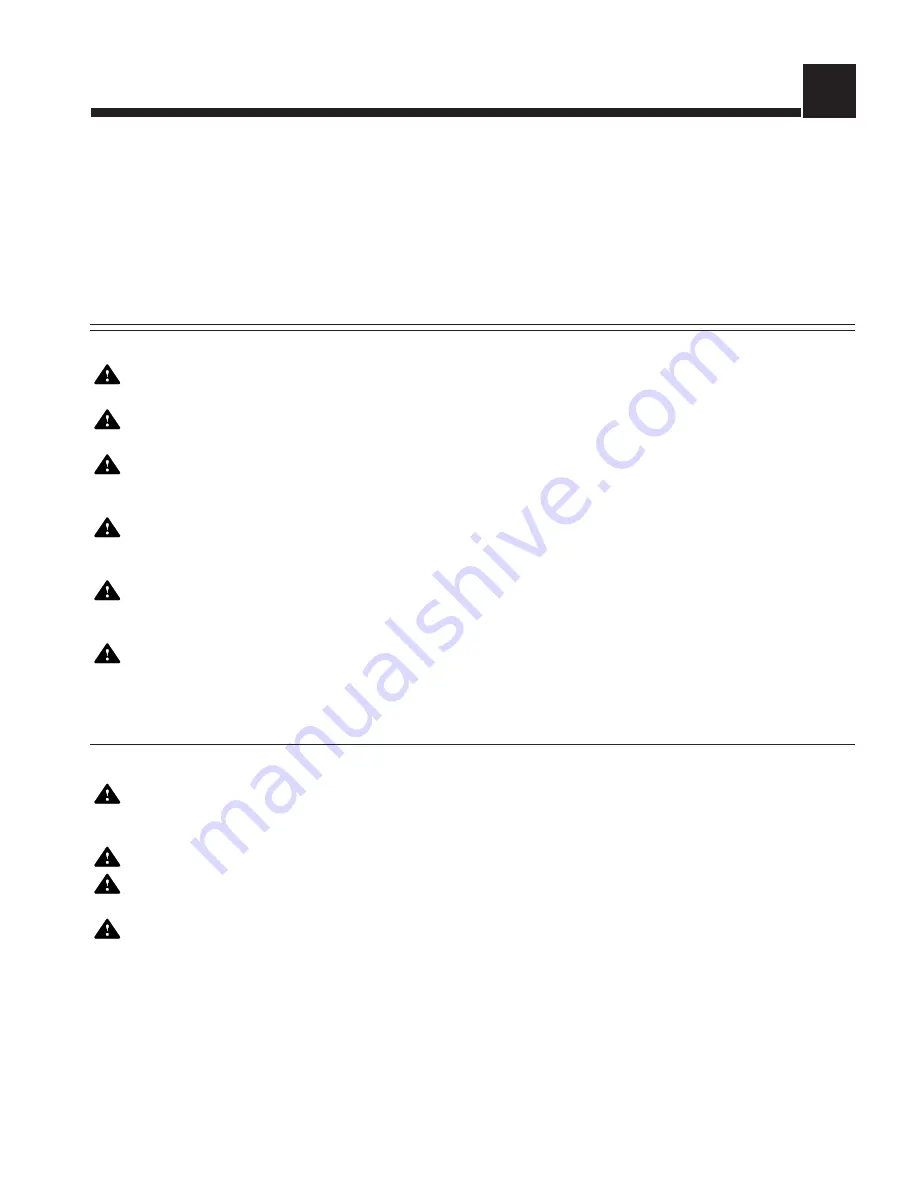
1-1
Safety Precautions and Symbols
Operator Manual
920017-148
The following
Safety Precautions must
must
must
must
must be observed when operating and servicing this equipment. WARNING indicates
the potential for personal injury and CAUTION indicates the potential for danger to equipment. These
Safety Precautions
are repeated, where applicable, throughout the manual.
It is important to review these
Safety Precautions before
operating or servicing the unit.
Strictly following these
Safety Precautions enhances your ability to safely and effectively utilize the unit and allows the
customer to avoid improper maintenance methods which could damage the unit or render it unsafe. It is important to
understand that these
Safety Precautions are not exhaustive; customers are encouraged to develop their own safety
policies and procedures to enhance and compliment these Safety Precautions.
WARNING – PERSONAL INJURY AND/OR EQUIPMENT DAMAGE HAZARD:
Always wear appropriate Personal Protective Equipment (PPE) when cleaning or removing debris from bottom of
the wash chamber and over the suction plate.
Before servicing or cleaning exterior of unit, always turn LOCK/UNLOCK/INIT key selector to LOCK position to
de-energize unit. Keep the key on yourself.
Only fully qualified service personnel should make repairs and adjustments to this equipment. Maintenance done
by inexperienced, unqualified personnel or installation of unauthorized parts could cause personal injury,
invalidate the warranty, or result in costly damage. Contact STERIS regarding service options.
Regularly scheduled preventive maintenance, in addition to the faithful performance of the minor maintenance
described within this manual, is required for safe and reliable operation of this equipment. Contact STERIS to
schedule preventive maintenance.
To open doors from inside wash chamber, pull EMERGENCY STOP cables. Washer operation will automatically
stop. Then, push firmly between door panels using shoulder and upper arm, applying upper body force. Do not
push between the two doors, but between the door panels.
To test or demonstrate Emergency Exit Safety Doors, first press EMERGENCY STOP pushbutton (located under
control) or EMERGENCY STOP cables (inside wash chamber) to turn power OFF. If power is still on while adjusting
or servicing doors, the photoelectric sensor will detect the movement of the door panels and doors will open
automatically.
WARNING – PERSONAL INJURY HAZARD:
If doors are still slightly open (less than 2 inches [5 cm]) when power is restored after a power failure, control will
apply pressure to complete closing. Lock building electrical supply disconnect switch in OFF position and close
unit air supply when opening doors after a power failure.
Keep hands/fingers away from closing doors to prevent crushing between the two doors.
Never perform cleaning of wash chamber until full cycle has been completed. If cycle has not been completed,
contaminated debris or water may remain in the bottom of the wash chamber
When doors are closing, a pinch point is created at the hinges. Keep fingers away from door hinges to prevent
pinching.
SAFETY PRECAUTIONS AND SYMBOLS
1
(See next page for additional Safety Precautions)