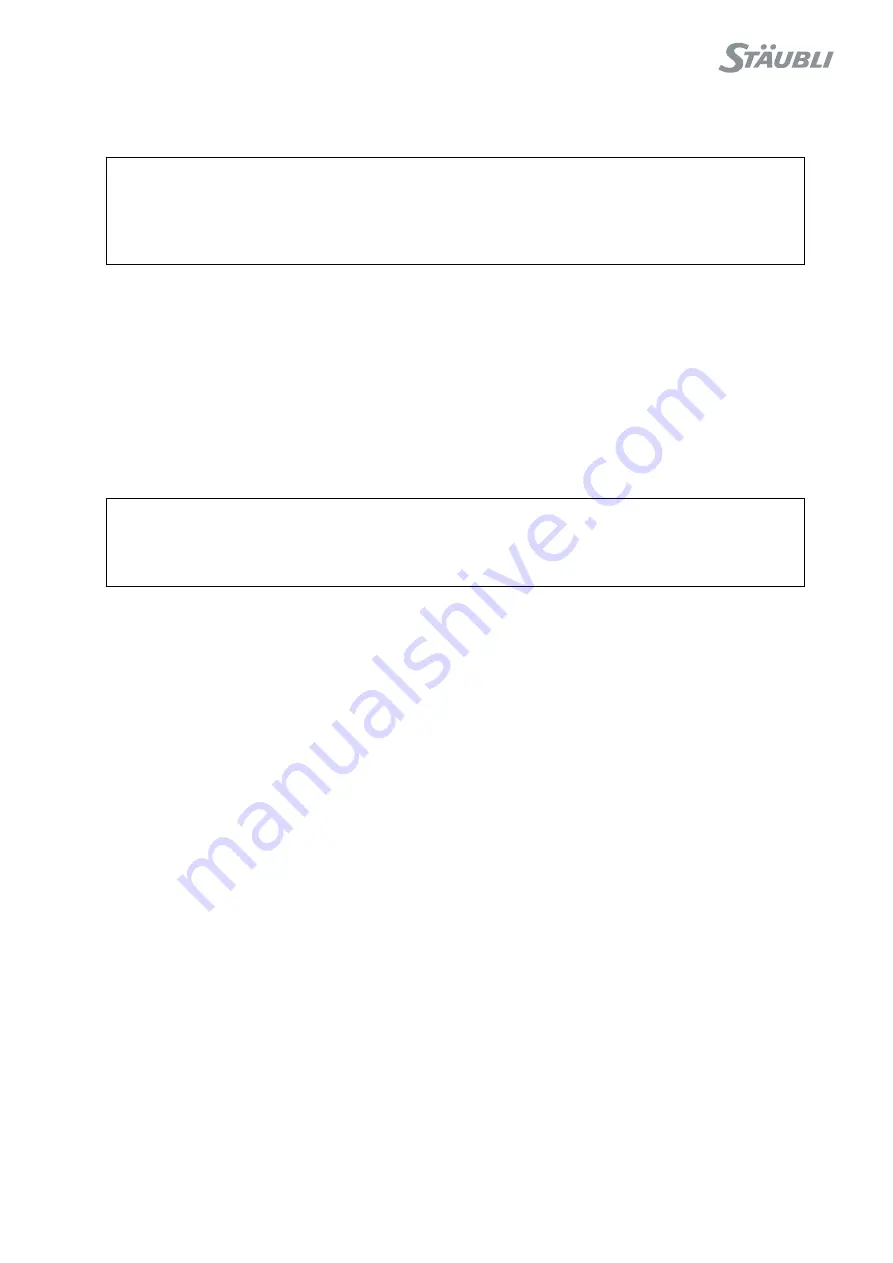
CS8C
D28070504A
127 / 248
Chapter 6 - Operation
6.5.
CALIBRATION, ADJUSTMENT, RECOVERY
6.5.1.
DEFINITIONS
Stäubli arms are
calibrated
in the factory, to determine the specific 'zero' arm position with maximum precision.
Calibration quality is essential for arm accuracy, i.e. its ability to respect the required Cartesian positions.
If drive elements (motor, encoder) have been replaced, or in the event of mechanical slippage due to a shock, the
specific "zero" arm position can be displaced on one or more joints: it is then necessary to
adjust
the joints to
restore the arm's original precision.
If one or more axis have been displaced, there are simple procedures for resetting them, using pre-established
reference positions. If more than two joints have been displaced, or if no reference positions are available, it is not
possible to adjust the arm correctly and it is necessary to carry out a full readjustment procedure.
The arm position at any given moment is shown by:
•
The position measured for each motor (encoder).
•
The "zero" resetting offsets
These offsets are stored in the respective encoders of each motor. A backup is saved in the
arm.cfx
file of the
controller, a copy of which is supplied on the CdRom delivered with each arm.
During start-up, if a zero offset from a motor encoder is different from the one in the
arm.cfx
file (f.i. replacement
of the arm linked to the controller), it is necessary to determine which offset is correct. This is done in the recovery
operation.
The motor encoder also stores a phase offset for the encoder-motor combination. In the same way as for the zero
offsets, the motor phase offsets are saved in the
arm.cfx
file of the controller. During start-up, if a motor phase
offset on a motor encoder is different from the one in the
arm.cfx
file, it is necessary to state which offset is correct,
using the recovery operation.
6.5.2.
RECOVERY PROCEDURE
The recovery application is accessed via the main menu on the
MCP
.
This is used to update arm or controller data if an inconsistency is detected between the data on a motor encoder
and the data in
arm.cfx
file of the controller.
The procedure consists of determining which set of data is correct, using a series of questions:
•
If you have simply replaced the arm linked to the controller, the
arm.cfx
file of the controller corresponds to the
former arm. You can then use the recovery menu to update it.
CAUTION:
Each time an adjustment or recovery procedure is done, the calibration of the arm has to be
checked carefully to verify that the robot is able to move in its expected angular range and not
more then that range. This verification has to be done at slow speed.
CAUTION:
It is important to provide for an adjustment procedure in the cell and define the associated
reference positions beforehand.
Summary of Contents for CS8C
Page 1: ...CS8C Controller Instruction manual D28070504A 26 03 2009 CS8C St ubli 2009...
Page 4: ...St ubli 2009 D28070504A CS8C 4 248...
Page 6: ...St ubli 2009 D28070504A CS8C 6 248...
Page 8: ...St ubli 2009 D28070504A CS8C 8 248...
Page 9: ...CS8C St ubli 2009 D28070504A 9 248 Chapter 1 Introduction CHAPTER 1 INTRODUCTION...
Page 10: ...St ubli 2009 D28070504A CS8C 10 248...
Page 13: ...CS8C St ubli 2009 D28070504A 13 248 Chapter 1 Introduction...
Page 14: ...St ubli 2009 D28070504A CS8C 14 248...
Page 16: ...St ubli 2009 D28070504A CS8C 16 248...
Page 20: ...St ubli 2009 D28070504A CS8C 20 248...
Page 21: ...CS8C St ubli 2009 D28070504A 21 248 Chapter 3 Safety CHAPTER 3 SAFETY...
Page 22: ...St ubli 2009 D28070504A CS8C 22 248...
Page 31: ...CS8C St ubli 2009 D28070504A 31 248 Chapter 3 Safety...
Page 32: ...St ubli 2009 D28070504A CS8C 32 248...
Page 33: ...CS8C St ubli 2009 D28070504A 33 248 Chapter 4 Installation CHAPTER 4 INSTALLATION...
Page 34: ...St ubli 2009 D28070504A CS8C 34 248...
Page 43: ...CS8C St ubli 2009 D28070504A 43 248 Chapter 4 Installation Holder measurements Figure 4 5...
Page 52: ...St ubli 2009 D28070504A CS8C 52 248...
Page 53: ...CS8C St ubli 2009 D28070504A 53 248 Chapter 5 Integration CHAPTER 5 INTEGRATION...
Page 54: ...St ubli 2009 D28070504A CS8C 54 248...
Page 77: ...CS8C St ubli 2009 D28070504A 77 248 Chapter 5 Integration Figure 5 13 Switches...
Page 81: ...CS8C St ubli 2009 D28070504A 81 248 Chapter 5 Integration Figure 5 14 Switches...
Page 111: ...CS8C St ubli 2009 D28070504A 111 248 Chapter 5 Integration...
Page 112: ...St ubli 2009 D28070504A CS8C 112 248...
Page 113: ...CS8C St ubli 2009 D28070504A 113 248 Chapter 6 Operation CHAPTER 6 OPERATION...
Page 114: ...St ubli 2009 D28070504A CS8C 114 248...
Page 153: ...CS8C St ubli 2009 D28070504A 153 248 Chapter 6 Operation...
Page 154: ...St ubli 2009 D28070504A CS8C 154 248...
Page 155: ...CS8C St ubli 2009 D28070504A 155 248 Chapter 7 PC utilities CHAPTER 7 PC UTILITIES...
Page 156: ...St ubli 2009 D28070504A CS8C 156 248...
Page 161: ...CS8C St ubli 2009 D28070504A 161 248 Chapter 7 PC utilities...
Page 162: ...St ubli 2009 D28070504A CS8C 162 248...
Page 163: ...CS8C St ubli 2009 D28070504A 163 248 Chapter 8 Maintenance CHAPTER 8 MAINTENANCE...
Page 164: ...St ubli 2009 D28070504A CS8C 164 248...
Page 243: ...CS8C St ubli 2009 D28070504A 243 248 Chapter 8 Maintenance...
Page 244: ...St ubli 2009 D28070504A CS8C 244 248...
Page 245: ...CS8C St ubli 2009 D28070504A 245 248 Chapter 8 Maintenance APPENDIX...