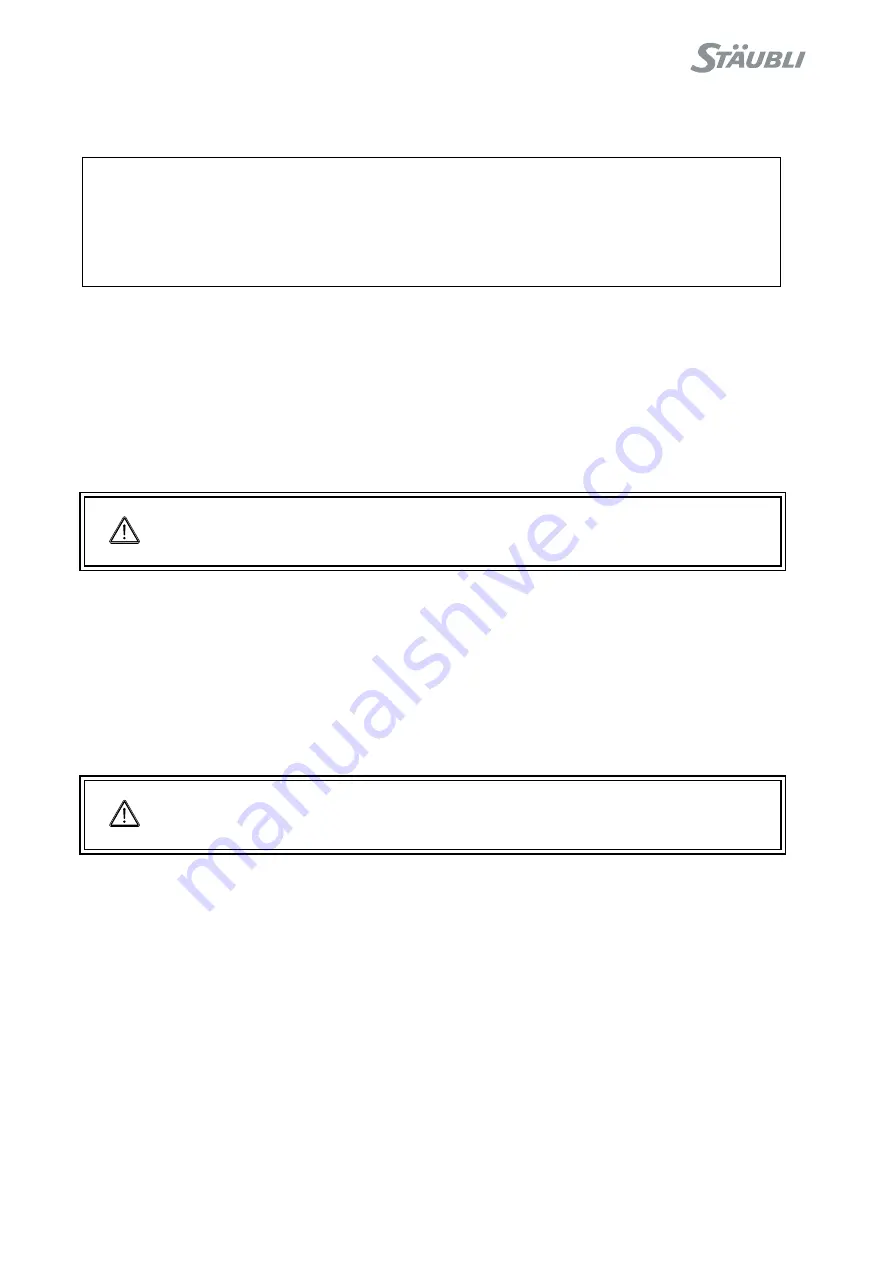
D28070504A
CS8C
126 / 248
6.4.
EMERGENCY STOP
When the emergency stop button is pressed, the power is removed from the arm and the brakes are applied. The
other equipment in the cell is also cut off from the power supply (depending on the cell wiring).
Following an emergency stop, a specific procedure is required to restore power to the arm:
•
The operator must leave the danger zone.
•
The
MCP
must be resting on its holder, fixed permanently outside the cell (a contact inside the
MCP
enables
this operation to be checked).
Restarting
Once those concerned have made certain that safety conditions have been restored, the arm power procedure
can be carried out using the
MCP
.
Note:
This operation must be carried out with the
MCP
on its holder when in manual mode.
•
Release the emergency stop button by turning it clockwise 1/4 turn.
•
Restore power to the arm in accordance with the standard procedure, using the arm power button on the
MCP
.
CAUTION:
The emergency stop is not the normal method for stopping arm movements; it must only be
used in a case of absolute necessity for a stop not provided for in your application.
An emergency stop leads to a sudden cut-off of power to the arm (and other equipements in
the cell), which, if it is repeated too often, leads to damage and reduced motor service life.
DANGER:
When the robot is restarted, all persons are prohibited from remaining in the isolation
area in which the arm moves.
DANGER:
If the
MCP
is not connected to the controller, it must not be left near the cell, because
its emergency stop button no longer works.
Summary of Contents for CS8C
Page 1: ...CS8C Controller Instruction manual D28070504A 26 03 2009 CS8C St ubli 2009...
Page 4: ...St ubli 2009 D28070504A CS8C 4 248...
Page 6: ...St ubli 2009 D28070504A CS8C 6 248...
Page 8: ...St ubli 2009 D28070504A CS8C 8 248...
Page 9: ...CS8C St ubli 2009 D28070504A 9 248 Chapter 1 Introduction CHAPTER 1 INTRODUCTION...
Page 10: ...St ubli 2009 D28070504A CS8C 10 248...
Page 13: ...CS8C St ubli 2009 D28070504A 13 248 Chapter 1 Introduction...
Page 14: ...St ubli 2009 D28070504A CS8C 14 248...
Page 16: ...St ubli 2009 D28070504A CS8C 16 248...
Page 20: ...St ubli 2009 D28070504A CS8C 20 248...
Page 21: ...CS8C St ubli 2009 D28070504A 21 248 Chapter 3 Safety CHAPTER 3 SAFETY...
Page 22: ...St ubli 2009 D28070504A CS8C 22 248...
Page 31: ...CS8C St ubli 2009 D28070504A 31 248 Chapter 3 Safety...
Page 32: ...St ubli 2009 D28070504A CS8C 32 248...
Page 33: ...CS8C St ubli 2009 D28070504A 33 248 Chapter 4 Installation CHAPTER 4 INSTALLATION...
Page 34: ...St ubli 2009 D28070504A CS8C 34 248...
Page 43: ...CS8C St ubli 2009 D28070504A 43 248 Chapter 4 Installation Holder measurements Figure 4 5...
Page 52: ...St ubli 2009 D28070504A CS8C 52 248...
Page 53: ...CS8C St ubli 2009 D28070504A 53 248 Chapter 5 Integration CHAPTER 5 INTEGRATION...
Page 54: ...St ubli 2009 D28070504A CS8C 54 248...
Page 77: ...CS8C St ubli 2009 D28070504A 77 248 Chapter 5 Integration Figure 5 13 Switches...
Page 81: ...CS8C St ubli 2009 D28070504A 81 248 Chapter 5 Integration Figure 5 14 Switches...
Page 111: ...CS8C St ubli 2009 D28070504A 111 248 Chapter 5 Integration...
Page 112: ...St ubli 2009 D28070504A CS8C 112 248...
Page 113: ...CS8C St ubli 2009 D28070504A 113 248 Chapter 6 Operation CHAPTER 6 OPERATION...
Page 114: ...St ubli 2009 D28070504A CS8C 114 248...
Page 153: ...CS8C St ubli 2009 D28070504A 153 248 Chapter 6 Operation...
Page 154: ...St ubli 2009 D28070504A CS8C 154 248...
Page 155: ...CS8C St ubli 2009 D28070504A 155 248 Chapter 7 PC utilities CHAPTER 7 PC UTILITIES...
Page 156: ...St ubli 2009 D28070504A CS8C 156 248...
Page 161: ...CS8C St ubli 2009 D28070504A 161 248 Chapter 7 PC utilities...
Page 162: ...St ubli 2009 D28070504A CS8C 162 248...
Page 163: ...CS8C St ubli 2009 D28070504A 163 248 Chapter 8 Maintenance CHAPTER 8 MAINTENANCE...
Page 164: ...St ubli 2009 D28070504A CS8C 164 248...
Page 243: ...CS8C St ubli 2009 D28070504A 243 248 Chapter 8 Maintenance...
Page 244: ...St ubli 2009 D28070504A CS8C 244 248...
Page 245: ...CS8C St ubli 2009 D28070504A 245 248 Chapter 8 Maintenance APPENDIX...