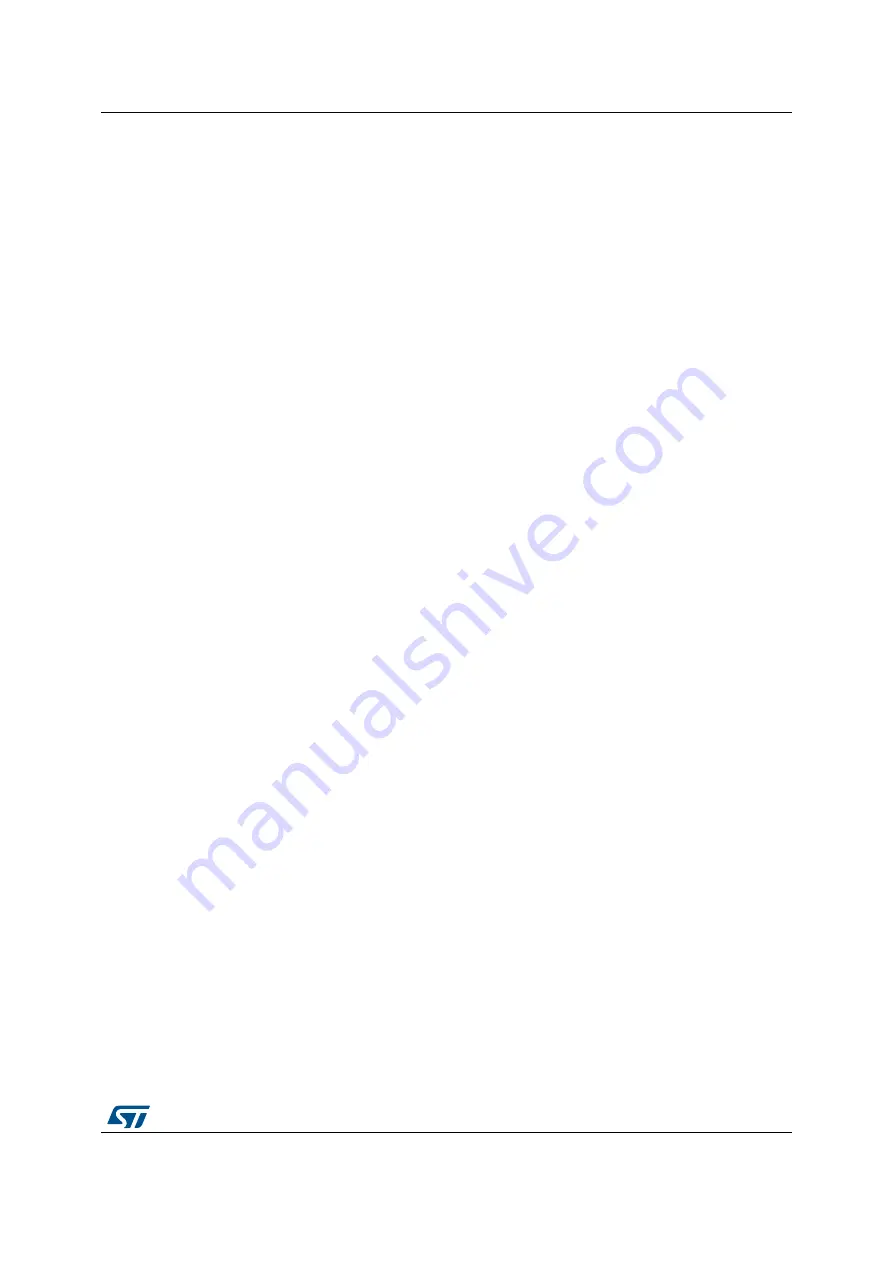
DocID025978 Rev 1
9/26
AN4450
Hardware (designing PCB schematics and layout)
26
In SPI the CS pin is the chip select and it is controlled by SPI master. It goes low at the start
of the communication and returns high at the end.
SPI communication can work in 2 different modes: 3-wires and 4-wires. In the first case the
pins used are: CS, SPC and SDIO; in the latter: CS, SPC, SDI and SDO. SPI mode
selection is done through bit 0 of register CTRL_REG1: 0=4-wires; 1=3-wires.
Both SPI and I²C interfaces are active by default. In case of SPI use only, I²C interface can
optionally be disabled by programming the corresponding bit in a control register
(CTRL_REG2[3]=1).
2.2
Pressure sensor PCB layout and soldering
recommendations
The LPS25H has an aperture on top of the package, so special care is required since
sensor performance could be compromised by:
Mechanical stress coming from the PCB board
–
The whole package s air should have minimum temperature gradient
–
Avoid placement in long and narrow PCB area, warp-free area
Temperature gradients (non-uniform/rapidly changing temperature around sensor)
Strong electrical field / light source
Localized air pressure stability (unwanted fast air pressure variation, fans)
Dust and water exposure/condensation (GORE-TEX
®
protection, etc.)
The HCLGA package is compliant with the ECOPACK
®
standard and is qualified for
soldering heat resistance according to JEDEC J-STD-020.
2.2.1
PCB design rules
The pressure sensor is affected by mechanical stress coming from the PCB board, hence it
should be minimized. A typical suggestion is to place the pressure sensor at the edge of the
PCB where warping is minimal.
PCB land and solder masking general recommendations are shown below. Refer to the
LPS25H datasheet for pad count, size and pitch.
It is recommended to open a solder mask external to PCB land.
The area below the sensor (on the same side of the board) must be defined as a keep-
out area. It is strongly recommended not to place any structure on the top metal layer
underneath the sensor.
This means that it is possible to place the ground plane in the PCB middle layer under
the LPS25H, but not in the plane immediately under the LPS25H.
Traces connected to pads should be as symmetrical as possible. Symmetry and
balance for pad connection will help component self-alignment and will lead to better
control of solder paste reduction after reflow.
For better performance over temperature, it is strongly recommended not to place large
insertion components like buttons or shielding boxes at distances less than 2 mm from
the sensor.
The pin 1 indicator must be left unconnected to ensure proper device operation.