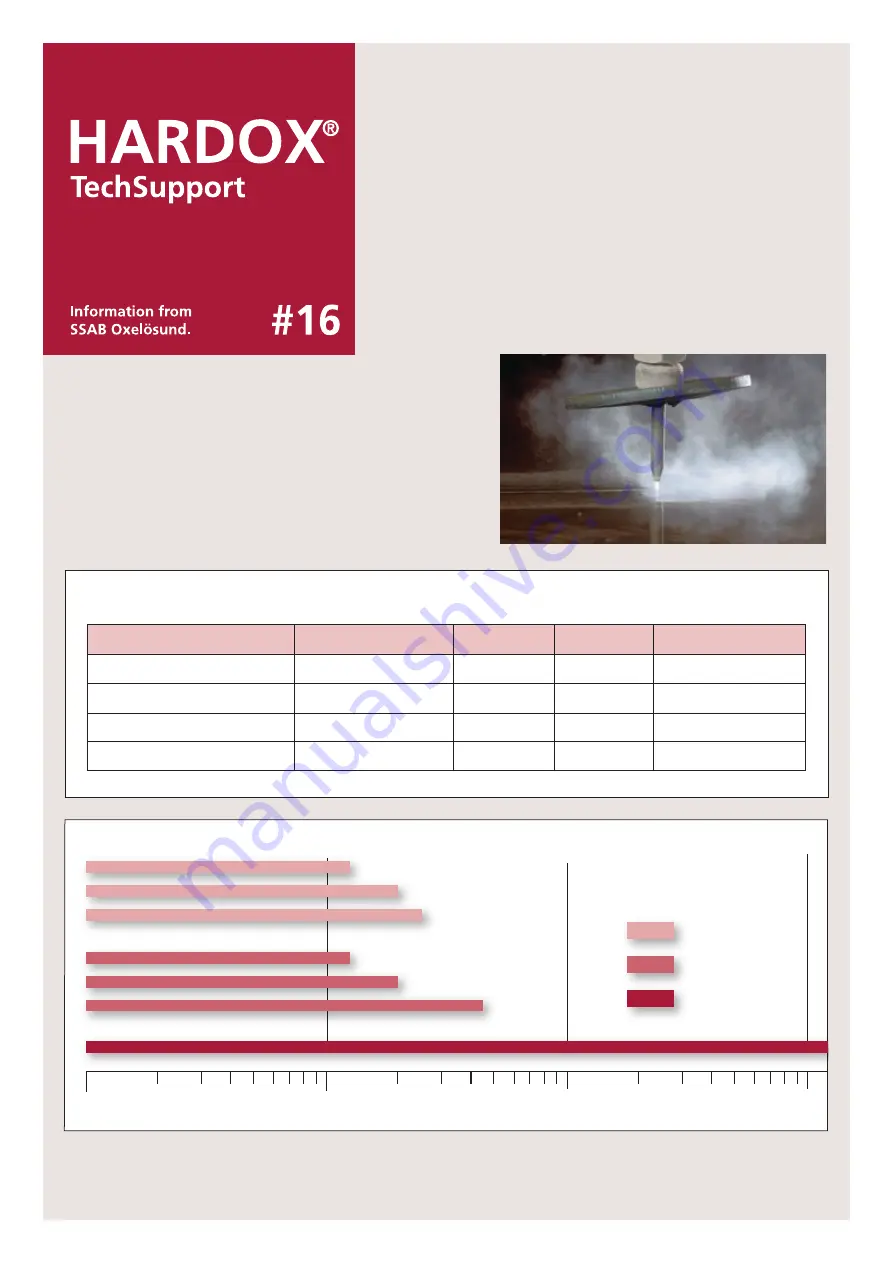
Cutting of HARDOX wear plate
Oxygen fuel cutting of HARDOX wear plate
is as simple as cutting of regular Mild Steel.
When cutting of thicker HARDOX plates special
attention is needed. For thick and hard plates the
risk of developing cut edge cracks increases. By
following the recommendations and guidelines
given below cut edge cracking and component
softening can be prevented.
Cutting methods
HARDOX wear plate can very well be cut
using both cold and thermal cutting methods.
The cold methods are abrasive water jet cut-
ting, shearing, sawing or abrasive grinding,
while thermal methods are oxy-fuel, plasma
and laser cutting.
This leaflet contains general suggestions and calculation models. SSAB Oxelösund AB does hereby expressly exclude any liability whatsoever for
their suitability for individual applications. It is the responsibilty of the user of the manual to adapt the recommendations contained herein to the
requirements of individual applications.
1000
CO
2
Laser
Plasma
Oxy-fuel
1.5 kW
3.0 kW
4.0 kW
100 A
200 A
600 A
Thickness range for different cutting methods
Plate thickness [mm]
10
100
1
1000
Abrasive
water jet
cutting
General features for different cutting methods
Cutting method
Cutting speed
Kerf
HAZ
Dim. tolerance
Abrasive water-jet cutting
8 –150 mm / min
1– 3 mm
0 mm
± 0,2 mm
Laser cutting
600 – 2200 mm / min
< 1 mm
0,4 – 3 mm
± 0,2 mm
Plasma cutting
1200 – 6000 mm / min
2– 4 mm
2– 5 mm
± 1,0 mm
Gas cutting
150 – 700 mm / min
2– 5 mm
4 –10 mm
± 2,0 mm
Table 1
Diagram 1