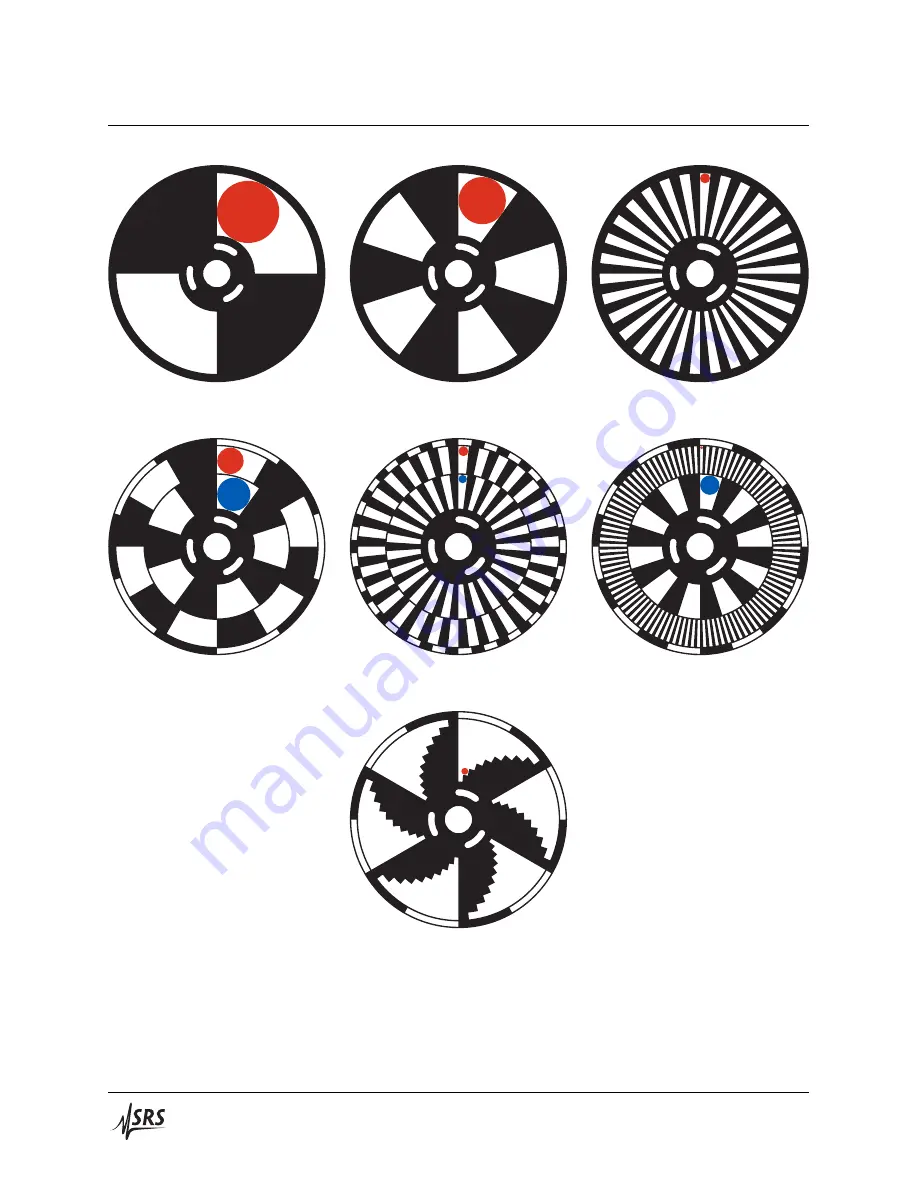
6
General Information
O54256 5/6 Slot
O5422530 25/30 Slot
O54210100 10/100 Slot
O542DF Variable Duty (10%–90%)
O5422 2 Slot
O5425 5 Slot
O54230 30 Slot
Figure 1:
Available chopper blades for the SR542. Max beam size for outer (red) and inner (blue) tracks are listed
in Table 1. The variable duty factor blade permits selection of duty factor from 10% to 90% in 10% increments
depending on the radial placement of the beam spot.
SR542 Precision Optical Chopper