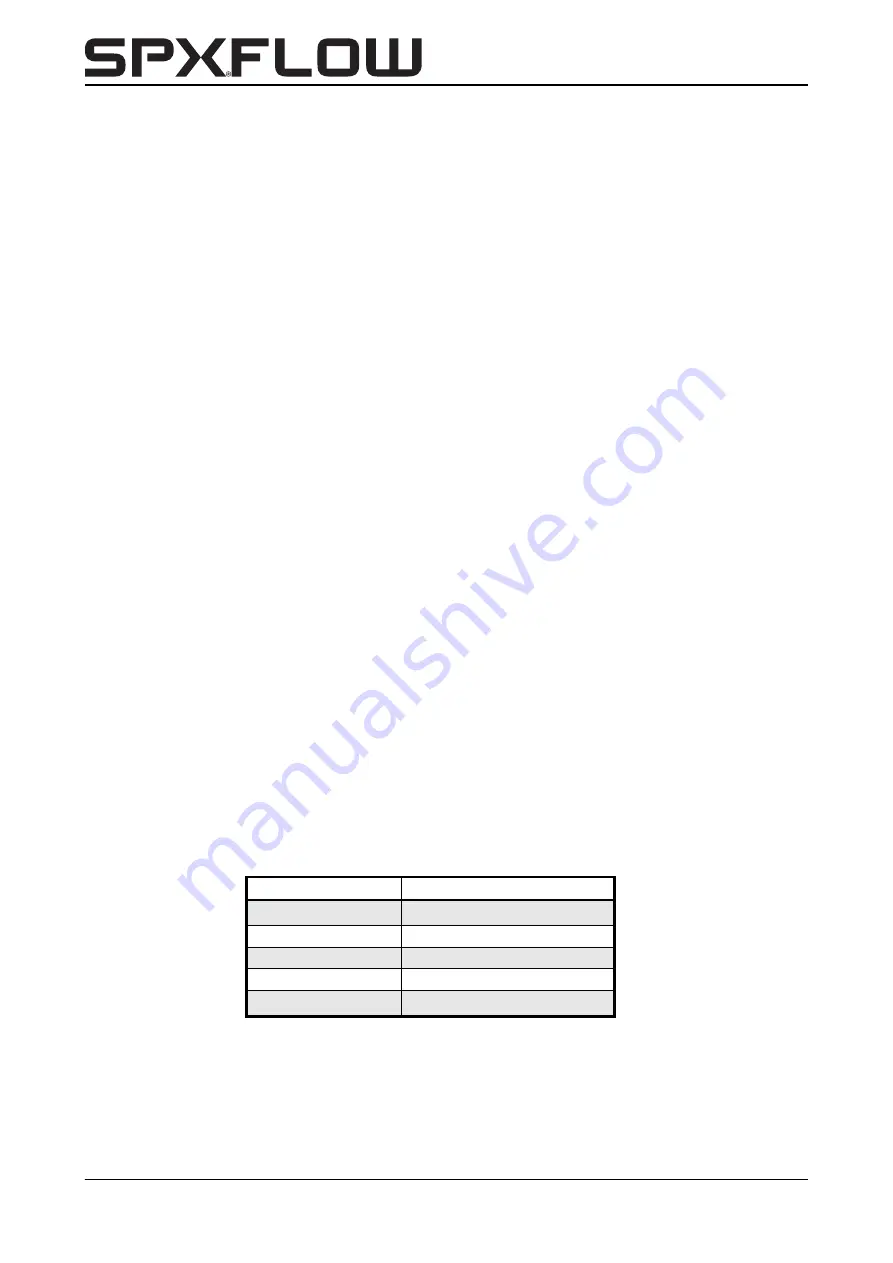
16
General
CRL/EN (1810) 2.2
2.7
Impeller
The back of the closed impeller is provided with back vanes in order to limit the pressure
on the shaft seal and to allow the flushing liquid to circulate. Contamination of the shaft
seal is also prevented. On the inlet side the impeller is provided with an interchangeable
wear ring. Running clearances meet the requirements of API 610.
2.8
Pump cover
The pump is designed to fit any seal type in accordance with API 682. In collaboration
with various suppliers of mechanical seals the design has been closely evaluated in order
to be able to build in the required variants.
2.9
Wear rings
Both the impeller and the pump casing are fitted with a renewable wear ring. The impeller
wear ring has a hardness at least 50°Br over the casing wear ring. The rings are secured
by three lock screws.
2.10
Mechanical seal
The various designs of pumps are created by the addition of shaft seal "cartridges".
These "cartridges" are standardized in the same three groups as the pump shafts and are
designed in accordance with API 682.
2.11
Bearing OH3 pump
• The bearing construction consists of two angular contact bearings (in "O"
arrangement) combined with a cylindrical roller bearing. The bearings are grease
lubricated. The bearings on the coupling side with which the axial force is taken up are
retained on the shaft by a shaft nut. The outer ring of these bearings is retained by the
bearing cover.
• The cylindrical roller bearing on the impeller side takes up radial forces and is mounted
"floating" on the outer ring. As a result of this the machining tolerances and expansions
can be easily accommodated. The bearing arrangement is sealed by labyrinth rings.
2.12
Coupling OH3 pump
Pump and motor are coupled by means of a flexible coupling with spacer sleeve
('spacer'). After the guards and spacer have been removed, the rotating part of the pump
can be easily dismantled as a whole without having to disconnect the electric motor or
the piping. This construction is called the Top Pull Out principle.
2.13
Application area
The application area globally looks as follows:,
However, the maximum allowable pressures and temperatures depend strongly on the
selected materials and components. Also working conditions may cause differences.
Table 1: Application area.
Maximum value
Capacity
470 m
3
/h
Discharge head
160 m
System pressure
5000kPa (50 bar)
Temperature
-30 to +200 °C
Viscosity
300 mm
2
/s
Summary of Contents for Johnson Pump CombiProLine OH3
Page 2: ......
Page 4: ...2 EC EN 1712 6 0 ...
Page 6: ...4 INT EN 1512 1 2 ...
Page 10: ...8 CRL EN 1810 2 2 ...
Page 20: ...18 General CRL EN 1810 2 2 ...
Page 40: ...38 Dimensions CRL EN 1810 2 2 ...
Page 52: ...50 Parts CRL EN 1810 2 2 ...
Page 66: ...64 ORDFORM 1512 3 3 EN ...