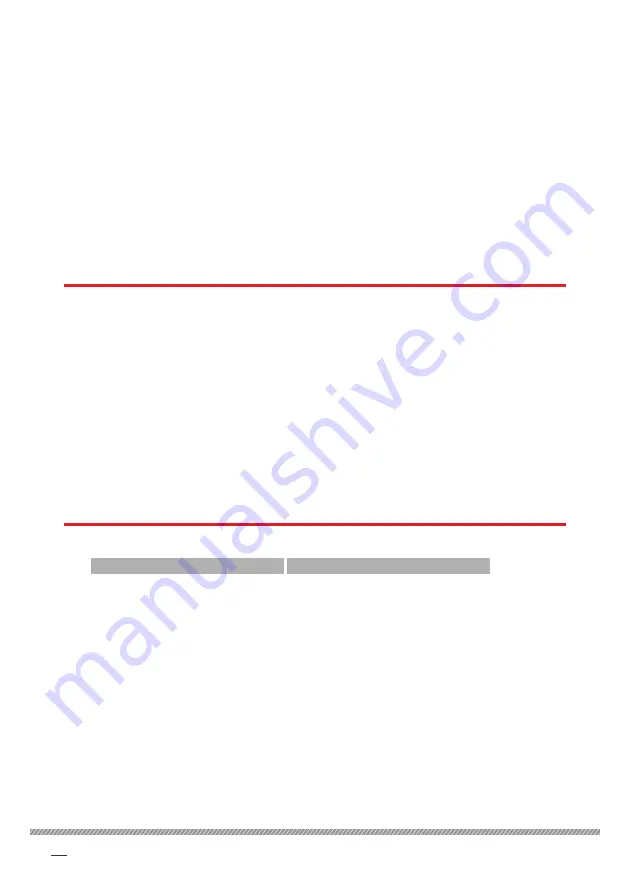
12
Commissioning
7
7 Commissioning
Commissioning
The suggested Commissioning strategy starts in the safest possible mode of operation and
progressively exercises each element of the system to achieve full functionality. For this
reason, we ship all drive units to run using:
• The highest supply option
• At nominal speed
• ARMATURE VOLTAGE control mode
1.
Therefore, this commissioning procedure requires the drive set-up shown in "Figure 7
BASIC CONNECTION - Forward/stop/reverse by centre zero" on page 8.
2.
Ensure the BOTTOM jumper is factory set to
AV
(ARMATURE VOLTAGE control) and TOP
jumper to select
P
(Proportional). Refer to "8.1 PID feedback" on page 14.
7.1 Pre-operation motor checklist
3.
With no power applied, complete the following checklist:
• All power and control connections are secure, and the dc supply voltage is correct.
• The motor rating (armature current and voltage (plus 8 V)) is within the drive rating.
• Check for the correct insulation between individual motor elements and between
these elements and the earthed motor frame. Disconnect all drive cables before
testing. The motor elements are armature winding, temperature sensors*,
tachogenerator* (* where applicable).
• Check inside the motor connection box for foreign objects, damaged terminals, etc.
• Check that motor brushes are in good condition, correctly seated and free to move in
brush boxes.
• Check for the correct action of brush springs.
• Check motor vents are free of any obstruction and remove any protective covers.
7.2 Initial settings - without power
4.
For an initial start, disconnect the armature and adjust the following presets for safety:
Max.
Fully anti-clockwise
IR Comp
Fully anti-clockwise
5. Apply power to the drive.
Check the READY lamp lights.
6.
Set the Stop switch to the RUN position.
7.
Rotate the external demand potentiometer fully clockwise and monitor the output
voltage between terminals 8 and 9 with a voltmeter. Increase the clockwise rotation
of the
MAX
preset until the meter shows the maximum forward armature voltage
required.
8.
Rotate the external demand potentiometer fully anti-clockwise and monitor the output
voltage between terminals 8 and 9 with a voltmeter. Check that the voltmeter indicates
the maximum reverse armature voltage. Do not move the
MAX
preset.
9.
If using a STOP contact, check this reduces the armature voltage to approximately 0 V.
10.
Set the external speed demand to zero (refer to "8.1 PID feedback" on page 14 for the
PG links to set the voltage range to either ±4 to ±25 V or ±8 to ±50 V).
11.
Turn off the power supply.
Reconnect the motor armature.
Summary of Contents for 200XLV
Page 6: ......