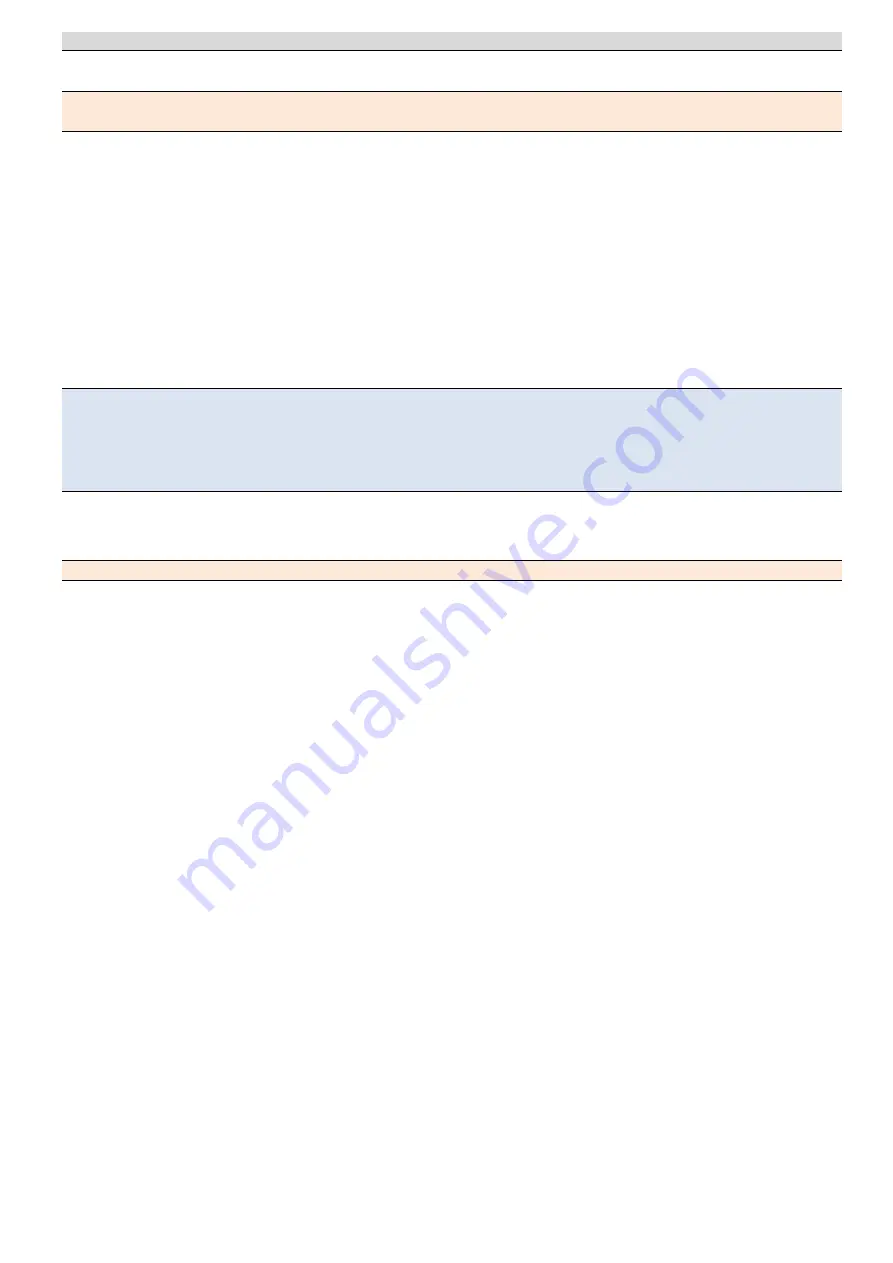
12
12.
CLEANING AND MAINTENANCE
12.1
CLEANING
Failure to carry out the correct cleaning routine could increase the risk of cross infection, due to presence of body fluids and/or residuals.
The operator must always wear adequate personal protection such as gloves and mask, etc. during all checking and cleaning procedures.
The exposed metal parts are usually treated and/or painted in order to increase their resistance to external agents. Clean the exposed parts
with water and delicate soap;
never use solvents or stain removers
.
Rinse thoroughly with warm water making sure that you have removed all traces of detergent, which could degrade or compromise the
integrity and durability of the device.
The use of high pressure water should be avoided
because water penetrates the joints creating the
risk of corrosion of components. Allow the device to dry thoroughly before storing. Drying after washing or after use in wet environments
must be natural and not forced; do not use flames or other sources of direct heat.
If you need to carry out
disinfection
, use products that do not have corrosive or solvent action on the materials constituting the device Be
sure to take every precaution to ensure that there is no risk of cross-infection or contamination for patients and / or operators.
To maintain the polished appearance of the frame parts we recommend the use of polish cleaner Spencer STX 99 or in alternative creams or
waxes used for polishing car bodywork.
12.2
PRECAUTIONARY MAINTENANCE
Establish a maintenance program and periodic testing routine, identifying an employee responsible for this. The person to whom the
ordinary maintenance of the device is entrusted must ensure the basic requirements foreseen by the manufacturer in following paragraphs
are inspected.
All maintenance and periodic servicing activities must be registered and kept together with the servicing reports. These documents have to
be kept for a period of 10 years after the disposal of the device itself. This register will be made available to the competent authorities and/or
manufacturer if requested.
Routine maintenance of the device must be carried out by operators in possession of specific qualifications, trained and experienced in the
use and maintenance of the device.
The operator must always wear adequate personal protection such as gloves and mask, etc. during all checking and cleaning procedures.
Checks to be carried out before and after each use and at deadline indicated above, are as follows:
General functionality of the device
Cleanliness of the device (remember that the failure of cleaning may cause the risk of cross infections)
Correct fixation of all nuts, bolts and screws
Absence of cuts, holes, tears on the structure, including the straps
None of the tubes or metal sheets present bends or cracks
The seat or the backrest has no structural damage or cracks
Welded areas are intact, without any cracks or breaks
The seat belts, sheets, moving parts, wheels and handles are intact and functioning properly.
Lubrication of moving parts
State of use of wheels and breaking system
The wheels are correctly fixed, they are stable and turn properly
The wheels are free from debris.
The device opens and locks properly
The device opens and closes properly
There are belts for the immobilization of the patient and they are intact and functioning.
Posterior telescopic handles can be positioned, folded and locked properly in all positions as described in this manual.
Handles are stable and have no risk of slipping out
The locking mechanism of the telescopic handles works properly