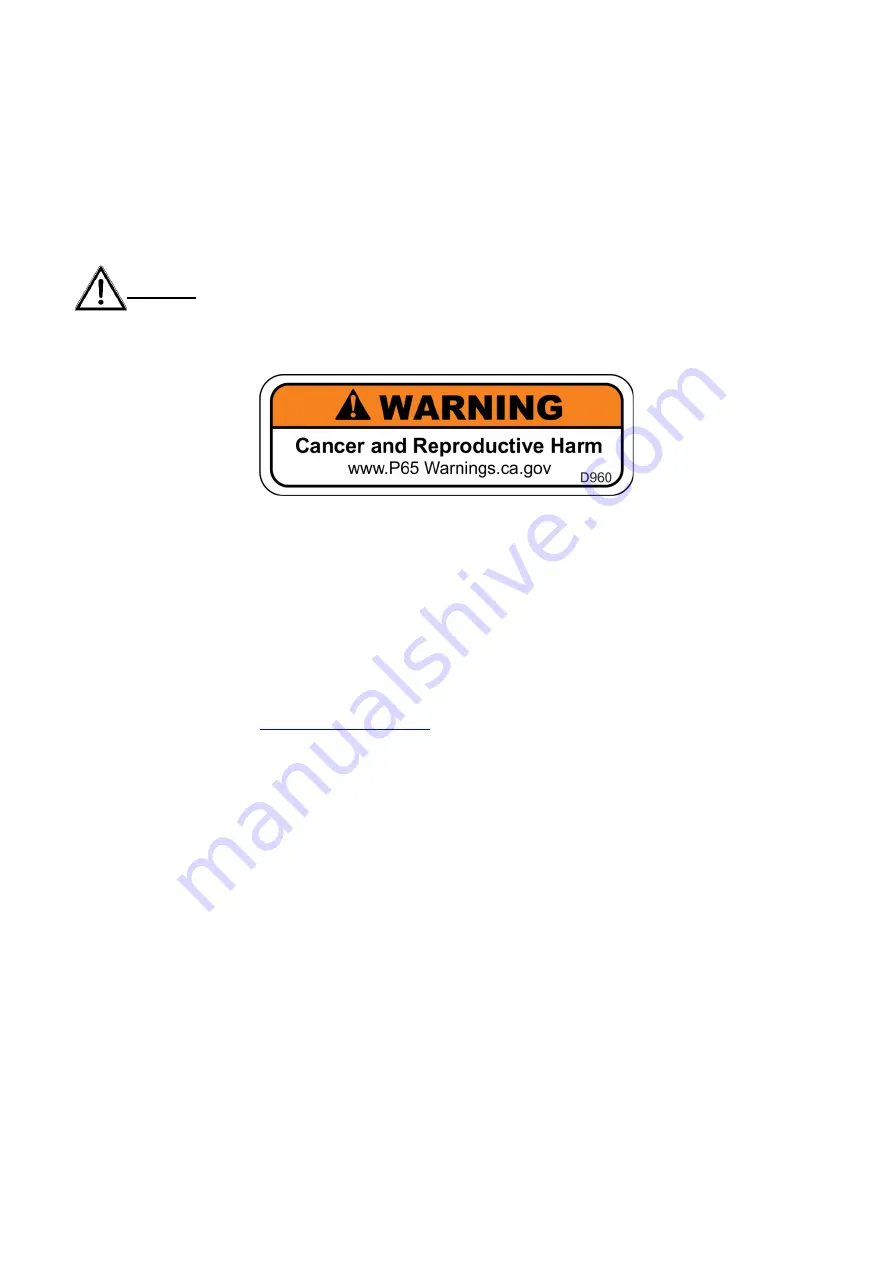
8999118EN: v1.1 21/12/2020
18
Original instructions (ENGLISH)
Website: www.spearheadmachinery.com
2.8
Working On Embankments
Sudden potholes at speed can quickly cause the tractor to change direction. At the same time the weight of the
implement may try to lift the front axle. This is a potentially lethal combination when working along narrow
embankments or dykes and can lead to overturning and potential drowning.
When working on top of embankments it is very important to have sufficient forward stability to ensure rapid
steerage control. Spearhead recommend 20% forward stability. This means that at least 20% of the total
vehicle weight is acting on the steering axle under normal level conditions.
DANGER!
When working on raised embankments ensure sufficient weight is on the steering wheels.
2.9
Proposition 65
Figure 2.1
– P65 Cancer And Reproductive Harm Decal
Operating, servicing and maintaining this equipment can expose you to chemicals including gasoline, diesel fuel,
lubricants, petroleum products, engine exhaust, carbon monoxide, and phthalates, which are known to the State
of California to cause cancer and birth defects or other reproductive harm.
To minimize exposure, avoid breathing exhaust, do not idle the engine except as necessary, service your vehicle
in a well-ventilated area and wear gloves and wash your hands frequently when servicing your vehicle. Battery
posts, terminals and related accessories contain lead and lead compounds, chemicals known to the state of
California to cause cancer, birth defects or other reproductive harm.
For more information go to
This website, operated by California's Office of Environmental Health Hazard Assessment, provides information
about these chemicals and how individuals may be exposed to them.