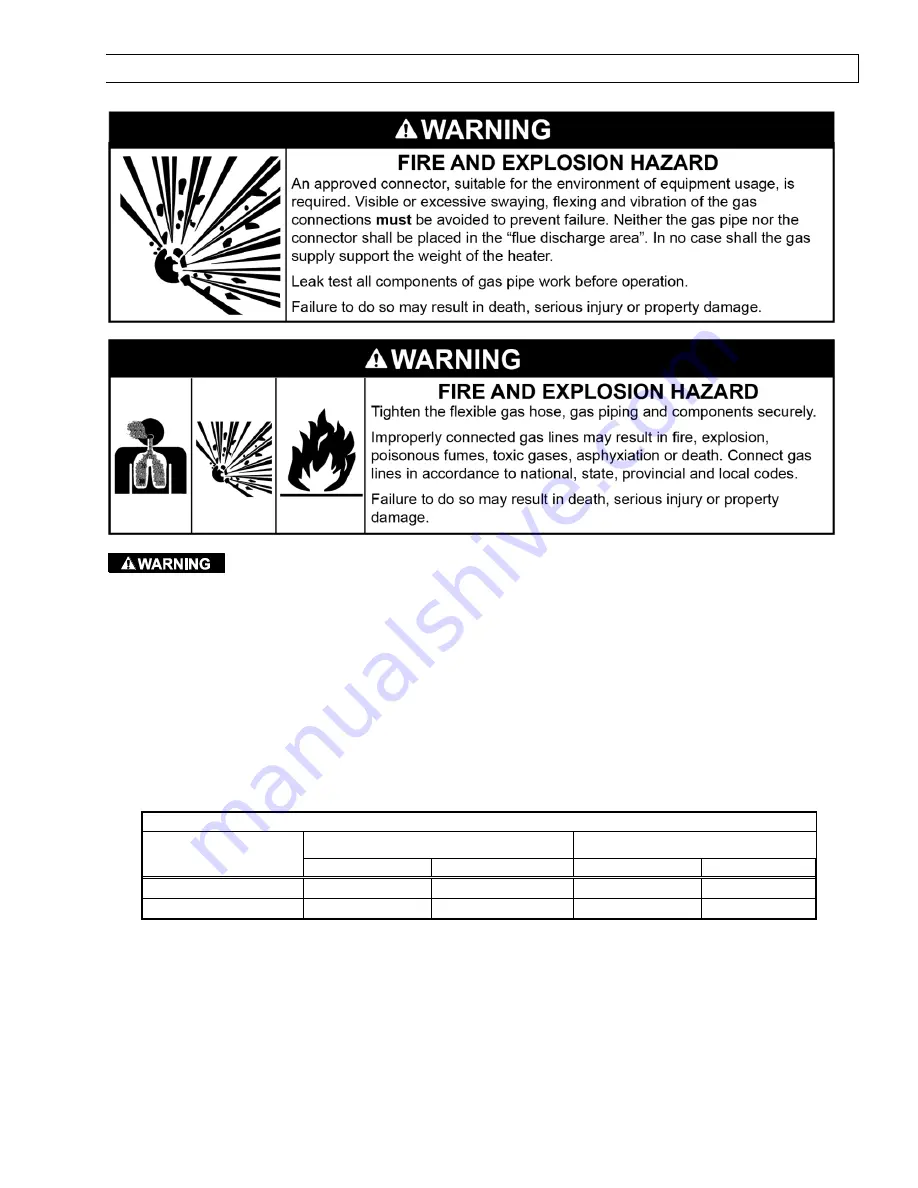
Form 44201360
26
Oct 2019
GAS CONNECTIONS AND REGULATION
15.0)
Use an approved flexible gas connector of 600mm minimum length when installing the heater
with flexible hanging methods as described in Section 12.0).
IMPORTANT BEFORE CONNECTING THE GAS TO THE HEATER
a)
Connect to the supply tank or manifold in accordance with National or local building codes. Authorities
having jurisdiction should be consulted before the installation is made.
b)
Check that the gas fuel on the burner rating plate matches the fuel for the application.
c)
Check that the gas supply piping has the capacity for the total gas consumption of the heaters and any
other equipment connected to the line.
d)
Check that the calculated supply pressure with all gas appliances and heaters operating will not drop
below the minimum supply pressure required for these heaters. See table below.
e)
All gas supply lines must be located in accordance with the required clearances to combustibles from the
heater as listed on the clearances label of the heater and Section 4.0) of this manual.
f)
Pipe joint compounds must be resistant to the action of liquefied petroleum gases.
g)
The heater will move when installed with flexible hanging methods, see Section 12.0). Use an approved
flexible connector for connections between the rigid piping and the heater. An approved shut off valve
should be installed within 1.8m (6ft) of the heater.
GAS PRESSURE TABLE
GAS TYPE
MANIFOLD PRESSURE
SUPPLY PRESSURE
High
Low (2-stage only)
Minimum*
Maximum
Natural Gas N7
15.0 mbar
7.0 mbar
20.0 mbar
60.0 mbar
Propane Gas L7
26.7 mbar
12.5 mbar
37.0 mbar
60.0 mbar