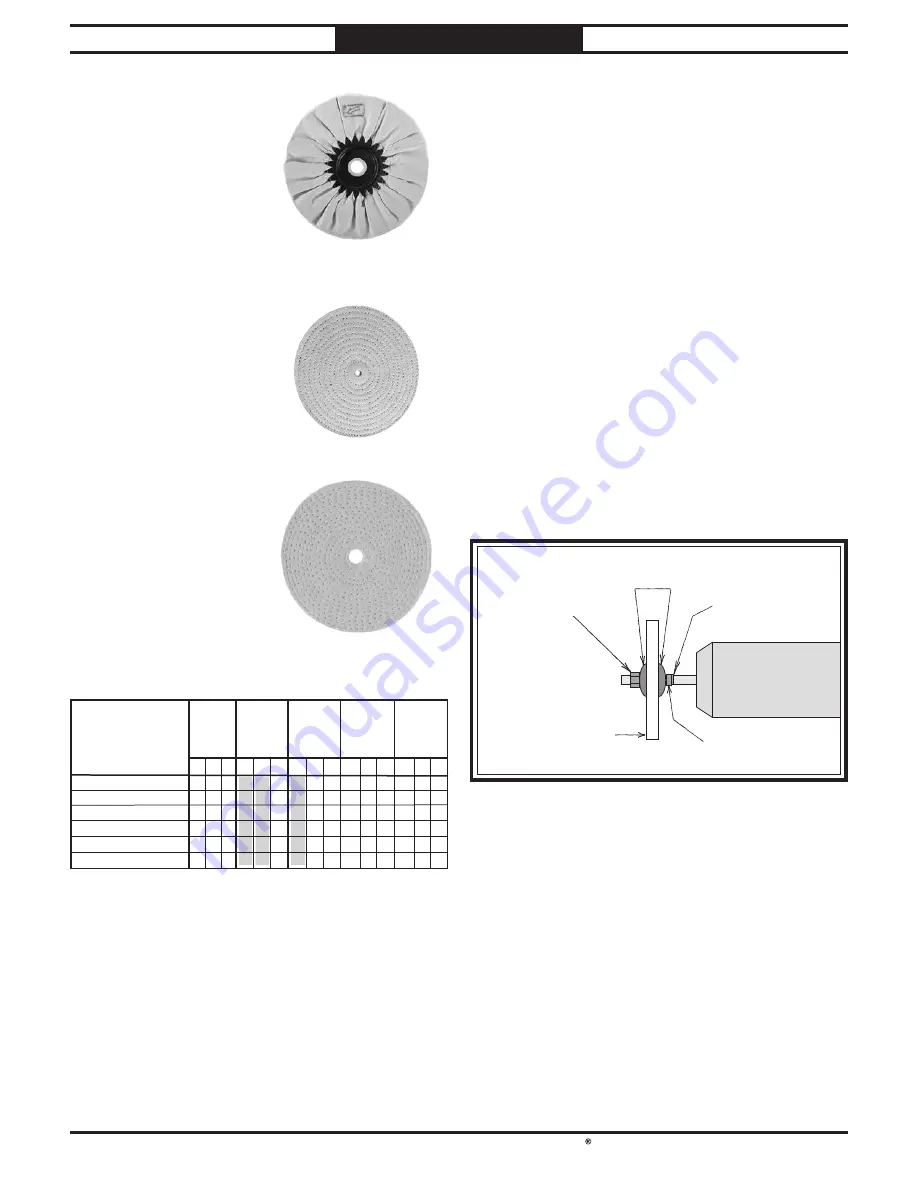
South Bend Tools
For Machines Mfd Since 1/21
Model SB1493
-19-
O P E R A T I O N
Airway Soft
Made of 100% cotton
sheets and held
together with a steel
retainer Pleats in the
material help hold
compound These
wheels are great for
polishing soft metals
and plastics
Laminated Sisal
Designed for rough
cutting, sisal works
well with various steels,
copper, aluminum,
and brass to remove
scratches and prepare
the piece for polishing
Spiral Sewn
Consist of layers of
100% unbleached cotton
sheeting that are spiral
sewn
1
⁄
8
" apart Works
well for initial polish on
brass, stainless steel,
aluminum, bronze and
cast iron
Buffing Sequence: R = Rough F= Final Cut, Initial Polish P = Final Polish
Plastics
Soft
Metals
Thin
Plating
Gold
Silver
Chrome
&
Nickel
Plate
Copper
Brass
Aluminum
Iron
Steel
Stainless
Steel
Buff Style
Loose Muslin-Soft
Loose Muslin-Hard
Airway Hard
Airway Soft
Laminated Sisal
Spiral Sewn
R F P R F P R F P R F P
R F P
X
X
X
X
X
X
X
X
X
X
X
X
X
X
X
X
X
X
X
Buffing Wheel Sequence Key
X
X
Installing/Removing
Buffing Wheel
The spindle shafts protruding from either side
of the motor make it easy to swap out different
buffing wheels for different projects Install an
appropriate wheel for your operation with a
5
/
8
"
bore
Tools Needed
Qty
Open-End Wrenches
7
/
16
" 2
To install/remove buffing wheel:
1.
DISCONNECT MACHINE FROM POWER!
2.
Remove spindle hex nut and outer flange
from each end of spindle (see Figure 13)
Note: Left spindle shaft has left-hand
threads so hex nut threads counterclockwise
onto sleeve.
5
/
8
" Hex Nut
Wheel
Flanges
16mm Bushing
19mm Bushing
Figure 13. Buffing wheel order of installation.
3.
Remove old buffing wheels (if installed) DO
NOT remove inner flange or bushings
4.
Install desired buffing wheels between inner
and outer wheel flanges (see Figure 13)
5.
Secure wheels and flanges with spindle hex
nuts removed in Step 2