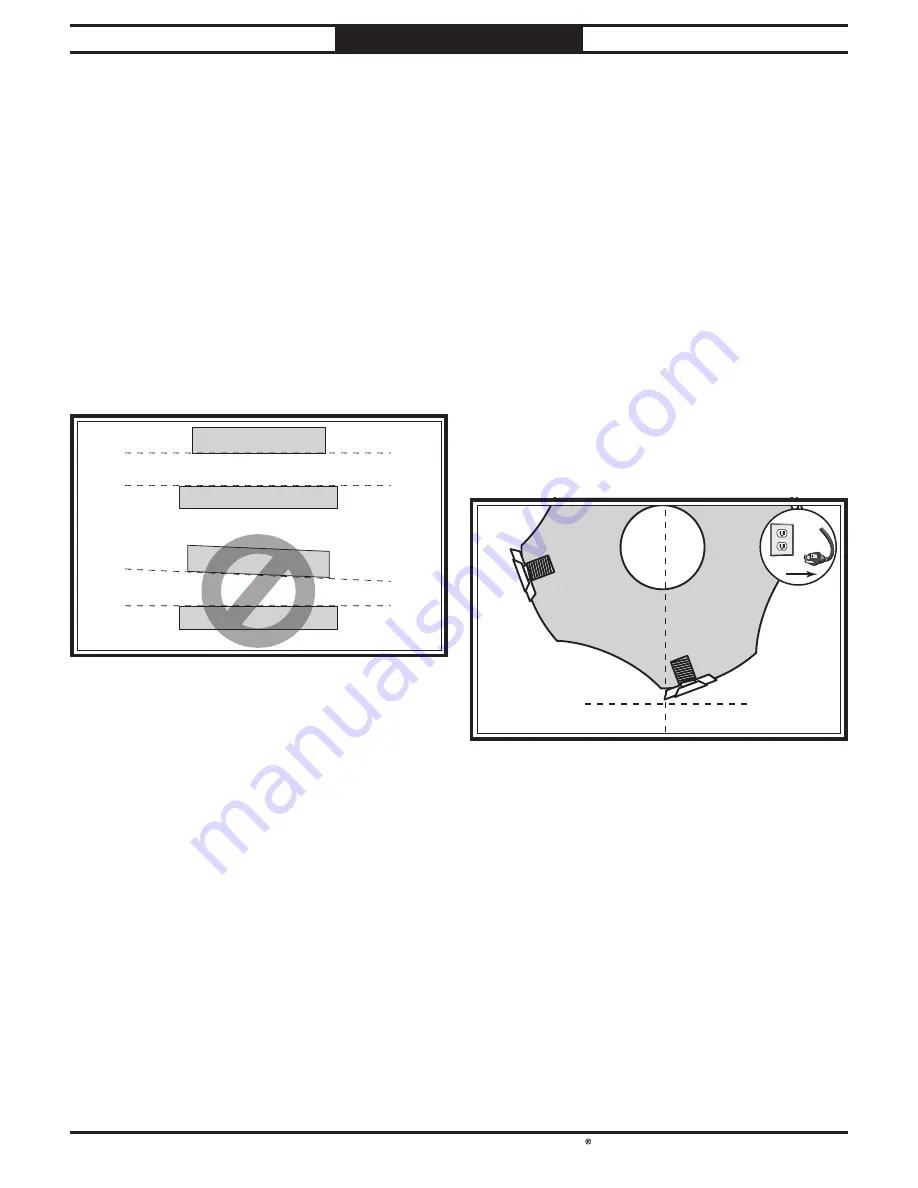
-52-
For Machines Mfd. Since 10/21
South Bend Tools
Model SB1118
S E R V I C E
Adjusting Table
Parallelism
Maximum Allowable Tolerances
Cutterhead/Table Side-to-Side .....................0.003"
Tools Needed
Qty
Rotacator ...............................................................1
Hex Wrenches 6, 10mm .................................. 1 Ea
Figure
Figure 69. Side-to-side parallelism of table and
. Side-to-side parallelism of table and
cutterhead.
cutterhead.
Cutterhead
Cutterhead
Table
Table
Parallel
Parallel
Not Parallel
Not Parallel
FRONT
VIEW
SIDE-TO-SIDE
Table parallelism is critical to the operation of
the machine. As such, it is essential that the
table is adjusted parallel with the cutterhead
(within 0.002") from side-to-side, as illustrated in
Figure 69.
Table Parallelism Inspection
The easiest way to determine if your head
casting has a parallelism problem is to plane a
workpiece and measure the thickness in multiple
locations. If the workpiece is tapered from left-to-
right or from front-to-back, then parallelism may
be a problem.
Use your Rotacator (refer to Page 37) to further
inspect the table parallelism. If you do not have
a Rotacator, a wood block and feeler gauges may
be used, but extra care must be taken to ensure
accuracy. If the table is not within the maximum
allowable tolerances, it must be adjusted.
Table Parallelism Adjustments
The table is adjusted by turning the elevation
leadscrew housing brackets underneath the
table.
To adjust table parallelism:
1.
DISCONNECT MACHINE FROM POWER!
2.
Make sure all inserts are properly installed
(refer to Rotating/Replacing Cutterhead
Inserts on Page 36).
3.
Lower table at least 4" below headstock
casting using handwheel.
4.
Raise headstock cover.
5.
On left-hand edge of cutterhead, find bottom
dead center (BDC) of any carbide insert (see
Figure 70).
Figure
Figure 70. Determining bottom dead center.
. Determining bottom dead center.
Top Dead
Center
Bottom Dead
Center
— If using a Rotacator, find BDC of carbide
insert by slowly rocking cutterhead pulley
back and forth, and set Rotacator dial to
"0".
— If a Rotacator is not available, use a
wood block and a feeler gauge. Slowly
rock cutterhead pulley back and forth so
carbide insert just makes contact as it
passes feeler gauge.
!