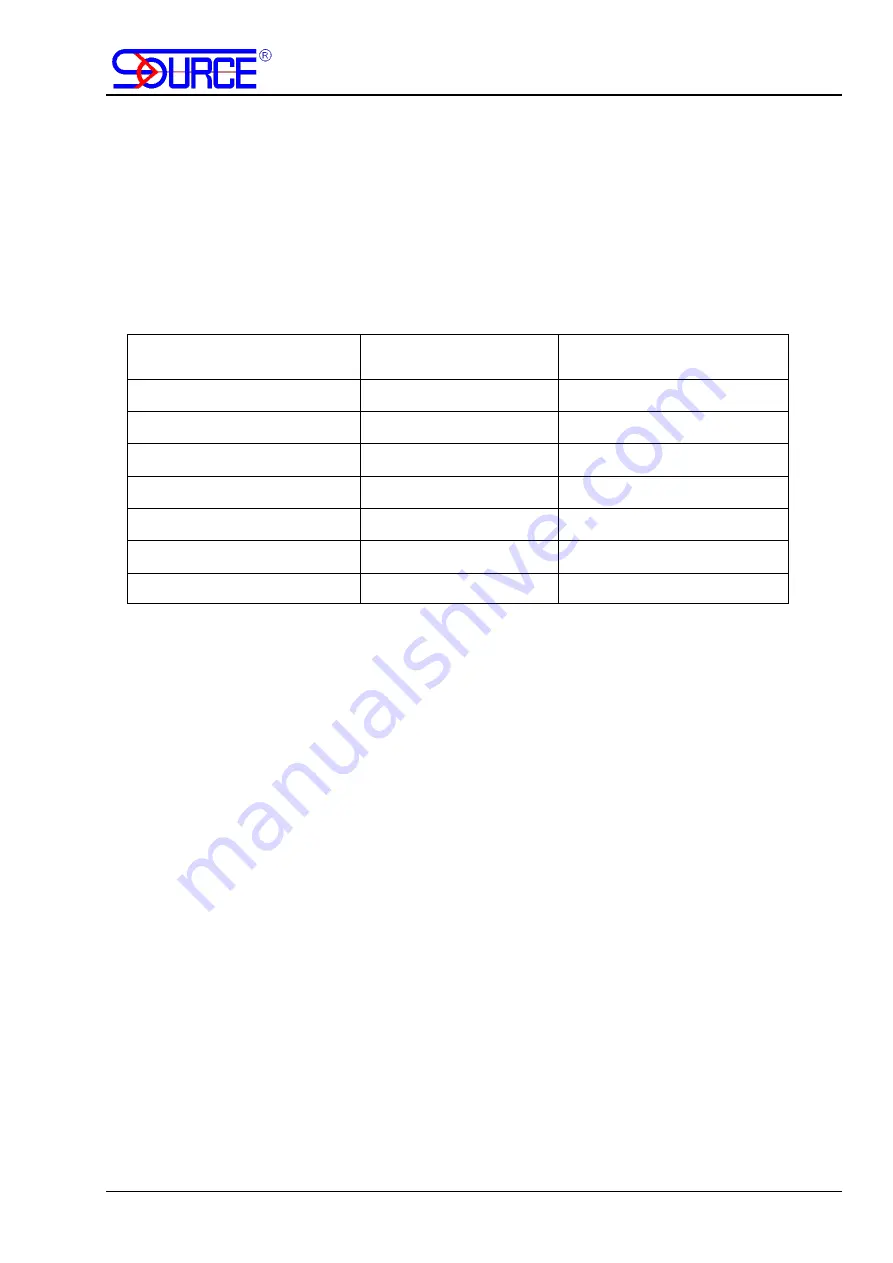
Operating & Service Manual 9 OPS-804 Rev.01
any pressure trapped in the valve cavity.
b)
Make up hose of injection pump to bonnet injection fitting and pump the approximate displacement
volume of grease as shown in Table 1 into the valve cavity.
c)
Operate the valve open/close several times to distribute the grease in the valve cavity. Continue to
pump until the required amount is displaced.
d)
Closed the valve. Bleed pressure and remove grease pump. Re-install injection fitting cap.
Table 1
Valve Sizes
Rectangular Cavity
Round Cavity
2-1/6" 2000 to 10000 Psi
1.0 Lbs
2.0 Lbs
2-9/16" 2000 to 5000 Psi
2.0 Lbs
3.0 Lbs
2-9/16
” 10000 Psi
3.0 Lbs
3-1/8" 2000 to 5000 Psi
3.0 Lbs
4.0 Lbs
3-1/16
” 10000 Psi
4.0 Lbs
4-1/16" 3000 to 5000 Psi
5.0 Lbs
4-1/16" 10000 Psi
5.0 Lbs
2)
Lubrication Procedure with Open Line Pressure
In a situation where the line pressure cannot be isolated to perform valve cavity lubrication, a high pressure
grease gun may be employed to force pressurized grease into the cavity.
a)
Close valve. Slowly back off cap on injection fitting. If the ball-check in the fitting is bleeding pressure,
than quickly retighten cap and abort the attempt to lubricate valve under line pressure. Otherwise,
proceed lubrication as follows.
b)
Install an isolation needle valve between injection fitting and the high pressure injection pump. Shut-off
needle valve, pump grease pressure up to approximately 1,000 psi higher the line pressure in the valve.
c)
Open needle valve to allow the pressurized grease to force open the ball-check and flow into the valve
cavity. Repeat this procedure until sufficient grease is injected into the valve cavity.
d)
Close needle valve, remove injection pump and replace the cap to the bonnet injection fitting.
4.3 Field Replacement of Parts
1)
Replacement of Stem Packing
The VERSA-SLAB
TM
–LS Gate Valve is designed with the stem back seat feature to allow replacement of
stem packing while the valve is in service. The stem back seat can be performed with the valve either in the
open or closed position. However, as far as possible, the back seating of the stem is done preferably with
valve in closed position when field replacement of stem packing is desirable.