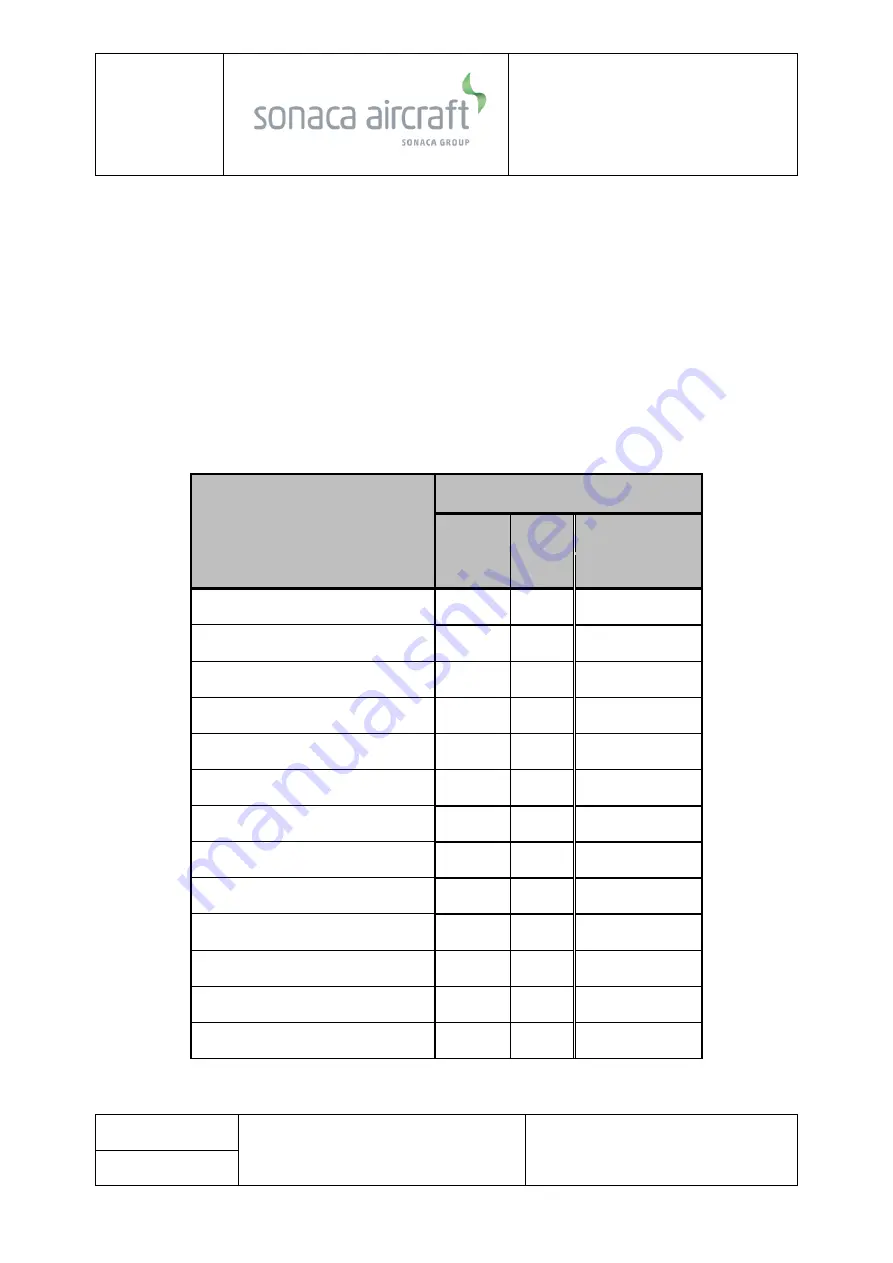
S201 AFM
6 - WEIGHT AND BALANCE
6.7 - EQUIPMENT LIST
27/06/2019
SONAIR-S2-D-MAN-006
Page : 6-6
Rev. : A
6.6
AIRCRAFT WEIGHING
Weighting the empty aircraft is a maintenance task, performed by an approved
Maintenance Organisation. Refer to the SONACA S201 Maintenance Manual for
aircraft weighing instructions. This is needed periodically or when a
modification or a repair is made to the aircraft.
6.7
EQUIPMENT LIST
ITEM
Metric
Weight Arm
Moment
kg
mm
kg.mm