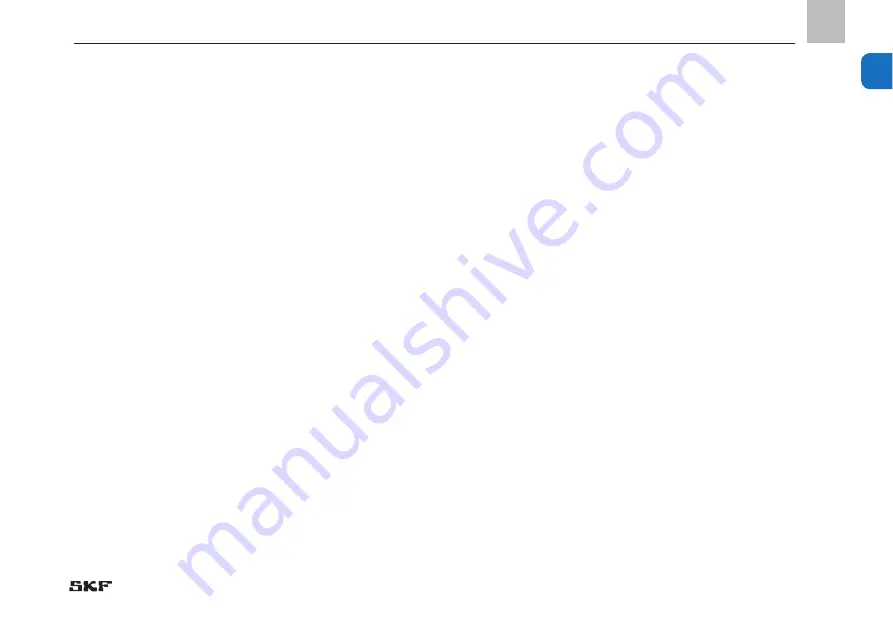
1
- 11 -
951-180-087-EN
Version 01
EN
1. Safety instructions
1.5
Painting plastic components
The painting of all plastic components and
seals of the products described here is
prohibited. Completely remove or mask af-
fected components before painting the main
machine.
1.6 Modiications to the product
Unauthorized modifications and changes
can have an unpredictable effect on safety.
Unauthorized modifications and changes
are therefore prohibited.
1.7 Prohibition of certain activities
The following activities must be performed
only by employees of the manufacturer or
ATEX persons authorized by the manufac-
turer due to possibly undetectable sources
of error or due to statutory requirements:
○
Repairs, modifications to the generator
○
Replacement, modifications to the
connections
1.8 Inspections prior to delivery
The following tests were performed prior to
delivery:
○
Safety and functional tests
○
For electrically operated products: Elec-
trical tests according to DIN EN 60204-
1, VDE 0113-1
○
For explosion-proof products: Inspec-
tions pursuant to the requirements of the
ATEX Directive
○
Use with a damaged, missing, or improp-
erly performed subsequent ATEX finish
pors, or fluids whose vapor pressure
exceeds normal atmospheric pressure
(1013 mbar) by more than 0.5 bar at
their maximum permissible operating
temperature
○
Use to feed, forward, or store lubricants
with solvents
○
Use in potentially explosive gases and
vapors whose ignition temperature is
less than 125% of the maximum surface
temperature
○
Use in potentially explosive dusts whose
minimum ignition temperature and glow
temperature are less than 150% of the
maximum surface temperature
○
Use in another, more critical explosion
protection zone