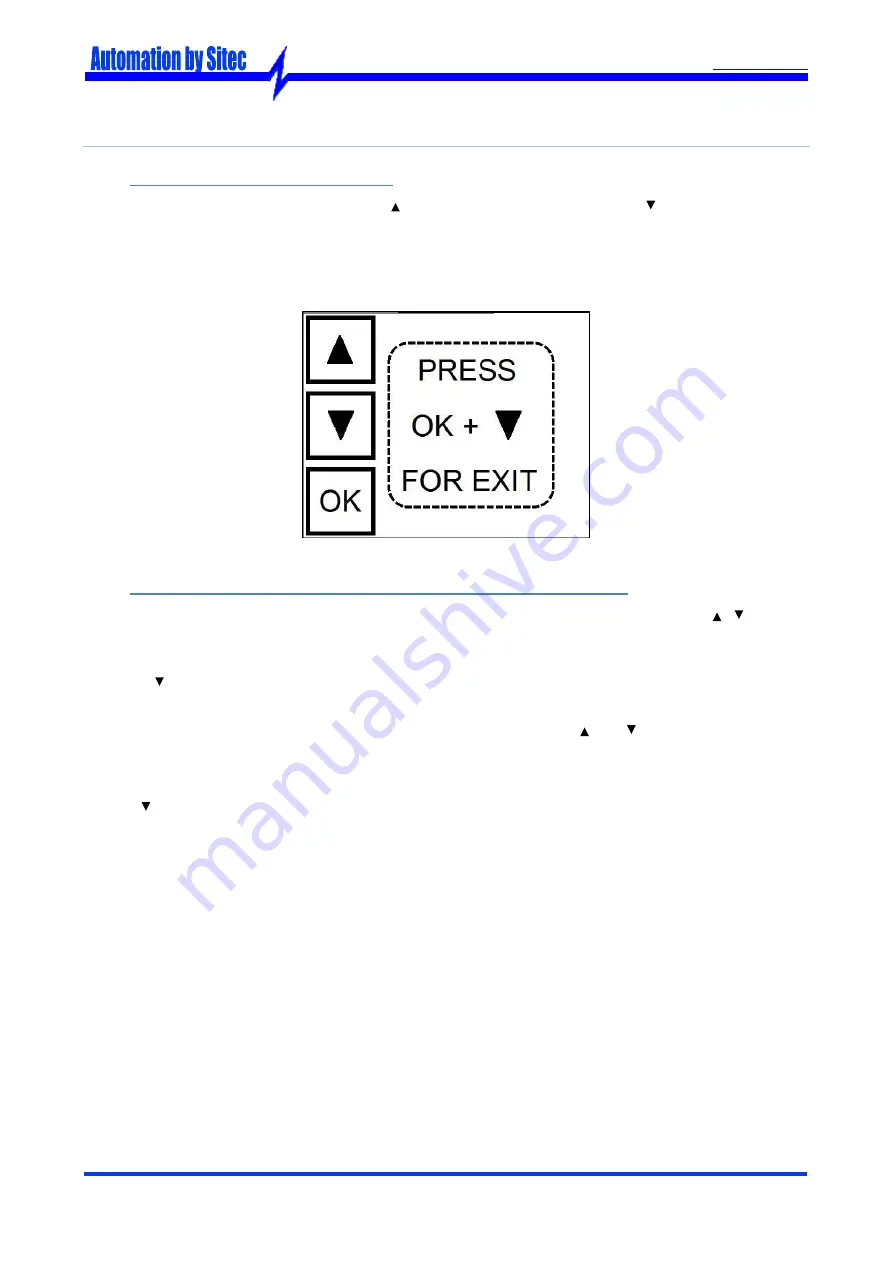
SITEC S.r.l. Industrial electronics
User Manual TRG 72x72
R2.A
Pag. 11
4.0 CONFIGURATION MENU
4.1 M
ENU CONFIGURATION KEYS
To change the values, you have to act on the key to increase the value or on the key to decrease it.
These keys function with one digit each time but, if pressed for more than half a second, the value increases
or decreases rapidly and, after three seconds pressed, the speed increases even more, in order to allow the
rapid achievement of the desired value.
4.2 H
OW TO ENTER
-
EXIT
-
SURF THE CONFIGURATION MENU
To access the thermoregulator configuration menu, simply press once any one of the ( , , OK)
keys beneath the thermoregulator.
To exit the configuration menu, you have to go back all the menu "hierarchy" while pressing the
OK
+
(
EXIT
) keys, or you can wait 10 seconds without pressing any button, then the thermoregulator
will automatically close the configuration menu without saving the ongoing changes.
To surf/increase/decrease the menu values you have to press the
and keys.
To confirm a selection, you have to press the
OK
key.
To cancel a change or go back to the upper level menu, you have to press simultaneously the
OK +
=
EXIT
keys
(
in this sequence
).