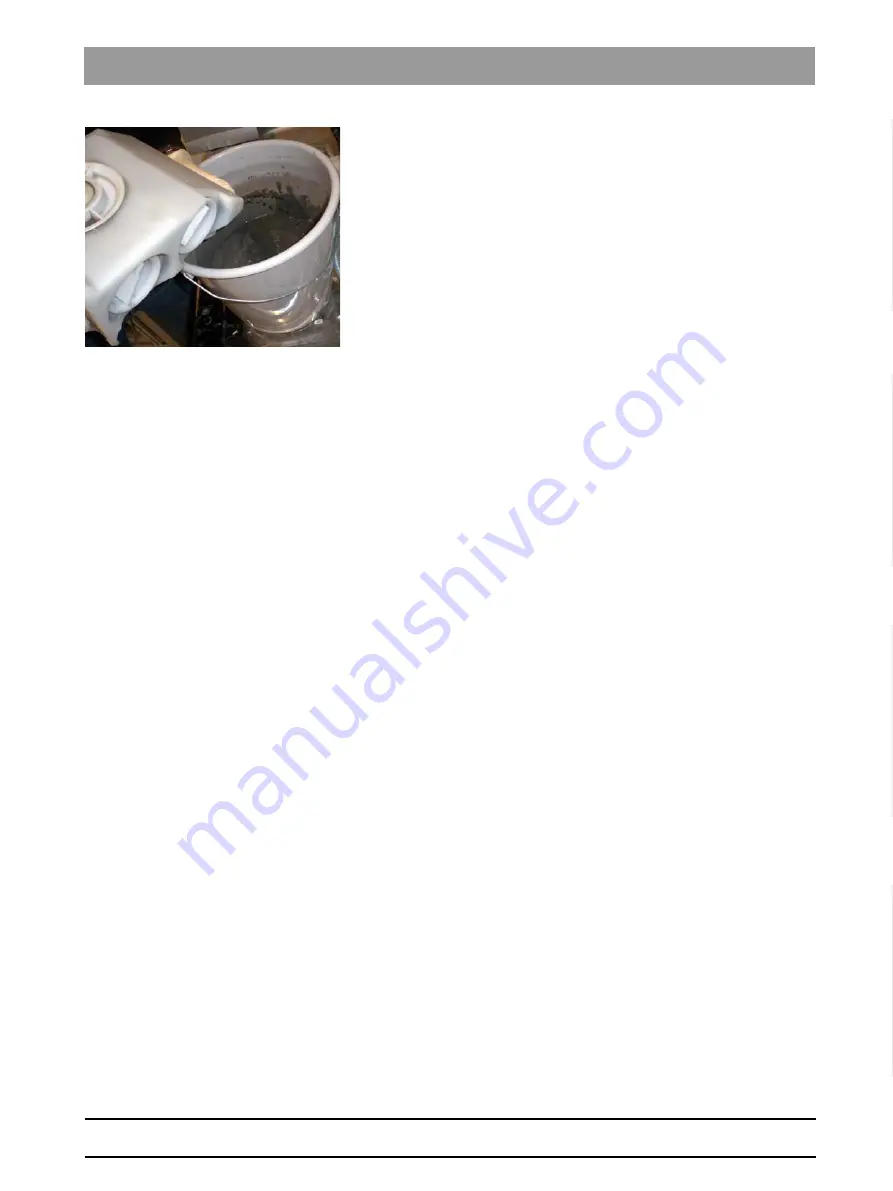
63 98 536 D 3439
D 3439
.
201.06.10
.
02 10.2017
57
Dentsply Sirona
7 Service
Operating Instructions CEREC MC XL Premium Package
7.4 Instruments
båÖäáëÜ
5. Empty approx. 1/3 of the contents of the tank into the collecting
vessel provided. Operating the spring-loaded inlet opening of the
tank cap (B) allows the contents to flow out more easily.
6. Close the drain opening (D) using your thumbs and pan the tank
vigorously 5x in circular movements again.
7. Empty approx. 1/2 of the remaining contents of the tank into the
collecting vessel provided. Operating the spring-loaded inlet opening
of the tank cap (B) allows the contents to flow out more easily.
8. Close the drain opening (D) using your thumbs and pan the tank
vigorously 5x in circular movements again.
9. Empty the residual contents into the collecting vessel provided.
10. Close the drain opening (D) with the screw cap.
Rinsing and emptying the water tank
1. Turn the tank cap (B) counter-clockwise and take it off.
2. Fill the tank approx. 1/3 full with water.
3. Close the tank cap (B).
4. Open the drain opening (D). Tilt the tank so that no liquid escapes
through the drain opening.
5. Close the drain opening (D) using your thumbs and pan the tank
vigorously 5x in circular movements again.
6. Empty the residual contents into the collecting vessel provided.
7. Close the drain opening (D) with the screw cap.
7.3.2.2.3
Filling the water tank
1. Turn the tank cap (B) counter-clockwise and take it off.
2. Add approx. 75 ml of DENTATEC to the tank.
3. Fill the tank with water until the filter inserts are completely immersed
(up to the bottom edge of the cover thread, approx. 3 liters).
4. Wait briefly until the filter inserts are soaked full and add a
corresponding amount of water. This applies in particular after the
filter has been changed.
5. Close the water tank by tightening the tank cap clockwise by hand.
Do not use the tank cap opener for closing the tank cap.
6. Push the water tank back into the housing.
7.4
Instruments
7.4.1
Overview of materials/instruments
For an updated table of approved instrument combinations, please visit
the
"www.sirona.com"
. To access the online portal for technical
documentation, follow the
"SERVICE"
/
"Technical Documentation"
menu items in the navigation bar. The portal can also be accessed
directly via the following address
http://www.sirona.com/manuals.
Select your product there and then open the
"Bur table"
document.
Summary of Contents for CEREC MC XL Premium Package
Page 77: ......