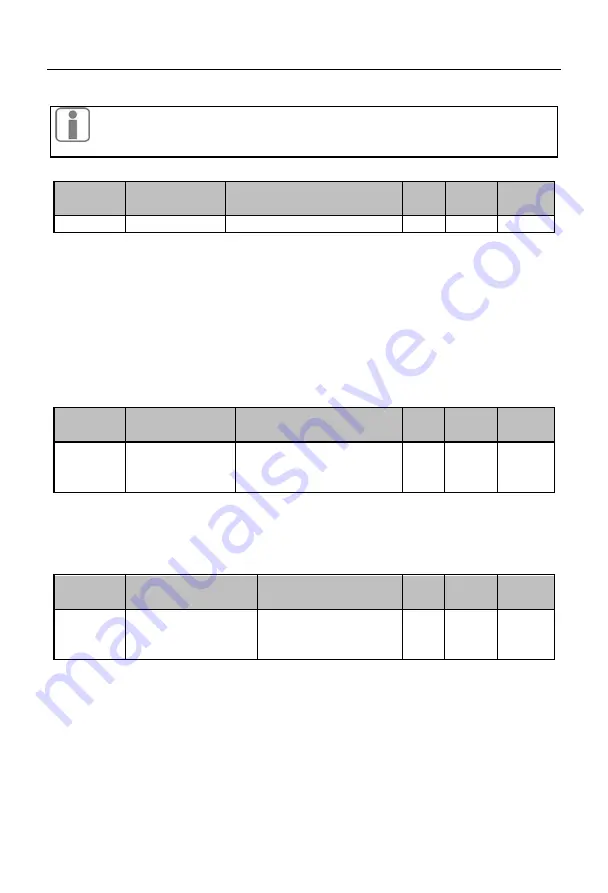
User Manual of A90 Series Inverter
167
Fig. 7-17 DC Braking Process for Start Fig. 7-18 DC Braking Process for Stop
In the presence of heavy loads, the motor cannot be stopped completely through
normal deceleration due to inertia. You can extend the duration of DC braking for
stop or increase the current of DC braking for stop to stop the motor from rotating.
Function
code
Function code
name
Parameter description
Unit
Default
setting
Attribute
F04.24
Flux braking gain 100-150 (100: no flux braking)
100
○
When the magnetic flux braking is valid (F04.24>100), the motor can be quickly
slowed down by increasing its magnetic flux, and the electric energy can be converted into
thermal energy during motor braking.
Flux braking may lead to quick deceleration, but the output current may be high. The
flux braking intensity (F04.24) can be set restriction and protection to avoid damage to the
motor. If flux braking is not applied, the deceleration time will be extended but the output
current will be low.
Function
code
Function code
name
Parameter description
Unit
Default
setting
Attribute
F04.26
Start mode after
failure/free stop
0: start according to F04.00
setting mode
1: start of speed tracking
0
○
The start after the fault or free stop may be set by default according to the F04.00
setting (F04.26=0), or set to the speed tracking start (F04.26=1). For the stop mode, see the
description of the function code F04.00.
Function
code
Function code name
Parameter description
Unit
Default
setting
Attribute
F04.27
Second confirmation of
terminal start command
0: Not required for
confirmation
1: to be confirmed
0
○
F04.27=0
: not confirmed
The running terminal (RUN or F/R) is closed, F00.03 is set to 0 or 1, and the terminal
is powered on during start/stop or directly run once enabled by switching the start/stop
mode.
F04.27=1
: confirmed
The running terminal is closed, F00.03 is set to 0 or 1, and the terminal is powered on