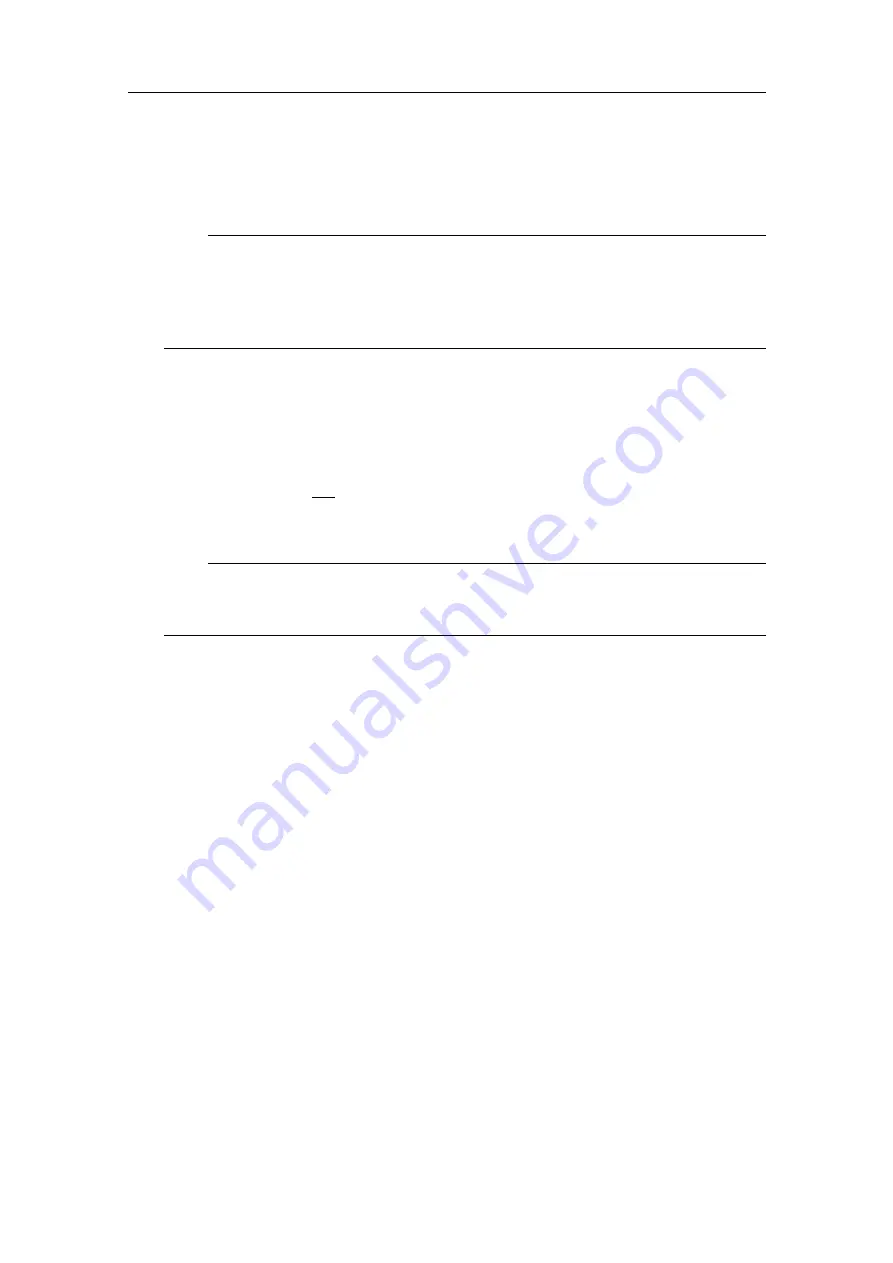
438371/A
107
2
Select the cable to be connected into the cabinet, and select the cable gland through
which the cable is to pass.
Note
A minimum of 5 cm (recommended 5 to 10 cm) of cable slack must be allowed, both
inside and outside the unity or cabinet, when you install cables. This is to allow for
vibration damping, maintenance and measurement errors. Always double-check
your measurements before taking any irreversible actions.
3
Measure the maximum length of cable.
a
If the cable has already been installed in conduits: Measure the maximum
length of cable required to reach from the final cable clip outside the cabinet to
the terminal block(s) inside the cabinet. Add 20 cm, and remove the excess
cable.
b
If the cable has not been installed in conduits: Measure the maximum length of
wire required to reach from the cable gland to the terminal block(s) inside the
cabinet. Add 20 cm, and mark the cable.
Note
The outer insulation on the cable will extend into the cable gland to a point
approximately 5 mm outside the outer surface of the cabinet wall.
4
Carefully remove the outer insulation from the required cable length.
Be careful! Do not damage the screen!
5
Leaving an appropriate length of the screen exposed from the insulation, cut off
the remainder.
Related topics
Basic cable requirements, page 102
Securing and terminating cables
Once a cable has been prepared for termination, it must be connected to a unit or cabinet.
Prerequisites
Electrical installations can only be done by certified electricians. All necessary tools and
instruments required must be available. The installation shipyard must prepare detailed
drawings of the electrical system, and identify each cable.
Context
Observe the relevant cable plans, cable lists and/or interconnection drawings for the
EC150-3C.
Summary of Contents for EC150-3C
Page 2: ......
Page 8: ...6 438371 A Simrad EC150 3C...
Page 128: ...126 438371 A Simrad EC150 3C Installation Manual...
Page 129: ...438371 A 127 Related topics Preparations page 29 Installation page 60 Drawing file...
Page 131: ...438371 A 129 Drawing file...
Page 134: ...132 438371 A Simrad EC150 3C Installation Manual...
Page 135: ...438371 A 133 Related topics Preparations page 29 Installation page 60 Drawing file...
Page 138: ...136 438371 A Simrad EC150 3C Installation Manual...
Page 139: ...438371 A 137 Related topics Preparations page 29 Installation page 60 Drawing file...
Page 141: ...438371 A 139 Drawing file...
Page 142: ...140 438371 A Simrad EC150 3C Installation Manual...
Page 143: ...438371 A 141 Related topics Preparations page 29 Installation page 60 Drawing file...
Page 150: ...2019 Kongsberg Maritime...