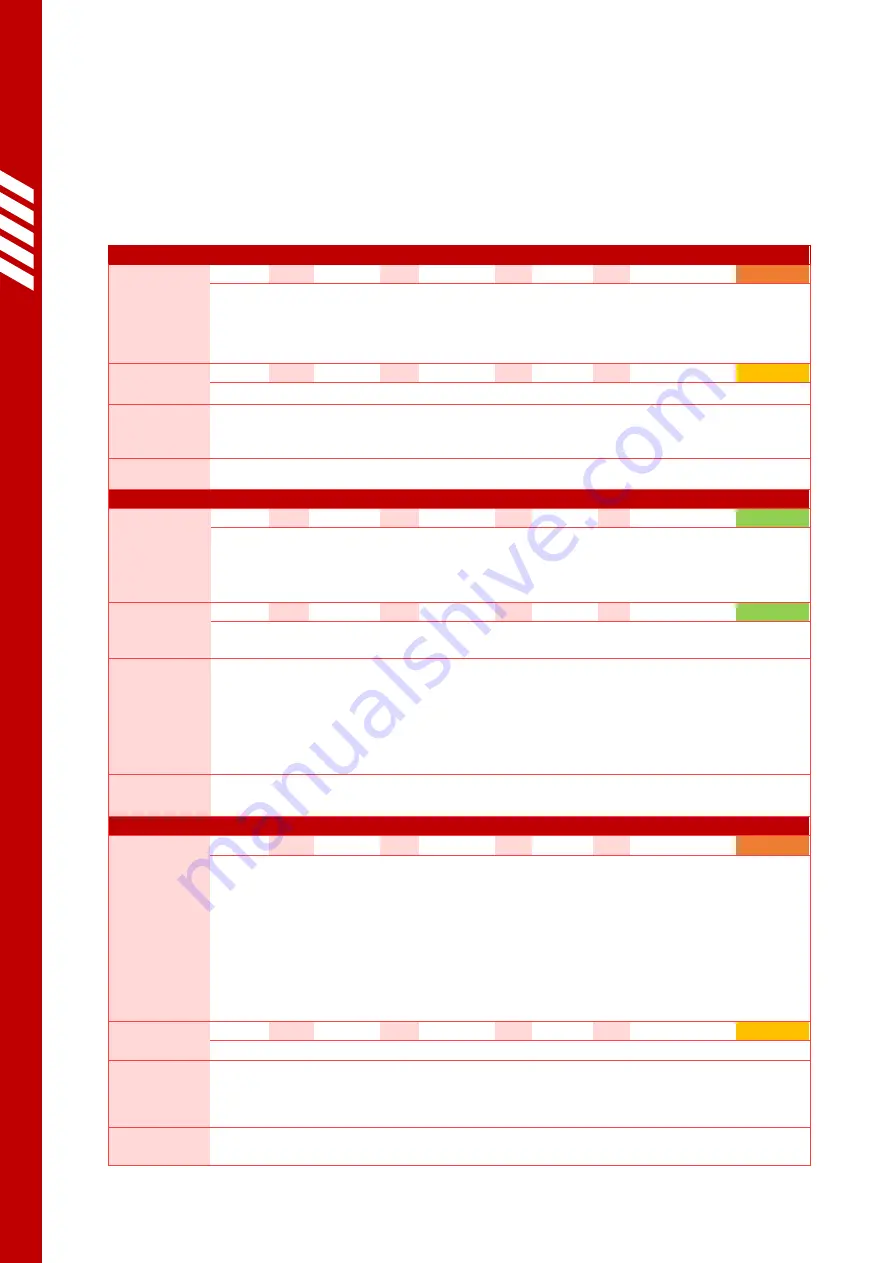
6.3.2
Identified Hazards
The following hazards have been identified that are intrinsic to the Quikstak design. For each
hazard a Risk Evaluation has been completed and control measures described.
Blank spaces are also provided to identify, assess, and describe control measures for
application- or site-specific hazards.
Entanglement or amputation of fingers or limbs in moving parts
Operator
LO:
1
FE:
4
DPH:
4
NP:
1
Risk Factor:
16
The Quikstak is designed so that potential trapping points and shear hazards are
eliminated, minimized, or isolated by guarding.
When QUIKSTAK MODE is enabled, the forks will not descend below 200mm
without manual control input.
Other
persons
LO:
1
FE:
2.5 DPH:
4
NP:
1
Risk Factor:
10
Other persons will less frequently be in proximity to moving parts.
Control
measures
Operators are responsible to obey warning signs fitted to the machine and
instructions regarding keeping clear of all moving parts.
Comments
Being struck by objects falling off the forks
Operator
LO:
1
FE:
4
DPH:
1
NP:
1
Risk Factor:
4
When being used as pallet stacker, the Operator is shielded from the load by
the body and mast of the stacker.
When using QUIKSTAK MODE it is possible for product to fall off the pallet and
strike the operator.
Other
persons
LO:
1
FE:
4
DPH:
1
NP:
1
Risk Factor:
4
When being used as a pallet stacker, it is possible for product to fall off the
pallet and strike persons standing near the stacker.
Control
measures
Product must be stacked carefully, and the load should be lifted no more than
500mm when being transported.
Ramps should always be traversed in a direction which causes the load to
recline against the fork carriage.
Operators are responsible to keep themselves and others well clear of the forks
when lifting loads higher than 1000mm.
Comments
Low-speed mode is automatically engaged when the forks are raised above
500mm.
Crushing due to rapid and/or uncontrolled descent of the forks
Operator
LO:
0.5
FE:
4
DPH:
8
NP:
1
Risk Factor:
16
There is no physical guarding preventing personnel from accessing the area
beneath the forks.
A pressure-compensating valve limits the lowering speed of the forks in normal
operation, and a hose-burst valve prevents the forks from falling in the event of
a hydraulic failure.
When QUIKSTAK MODE is enabled, the forks will not descend below 200mm
without manual control input.
Significant safety margins ensure that the probability of failure of any steel,
hydraulic, or control parts failing is very low.
Other
persons
LO:
0.5
FE:
2.5 DPH:
8
NP:
1
Risk Factor:
10
Other persons will less frequently be in proximity to the forks.
Control
measures
Operators are responsible to obey instructions and warnings regarding keeping
themselves and others away from the area beneath the forks at all times.
The Quikstak must be regularly maintained, and all faults promptly repaired.
Comments
Summary of Contents for QUIKSTAK QS10MM
Page 1: ...User Manual Quikstak QS10MM Original Instructions English v52 0 April 2022 USER MANUAL...
Page 3: ...User Manual Quikstak QS10MM Original Instructions English v52 0 April 2022 Page 2...
Page 26: ...4 4 9 Wiring diagram C O N TR O L L ER C U R TIS1212...
Page 36: ...Date Name Location Checks complete Maintenance carried out Parts used...