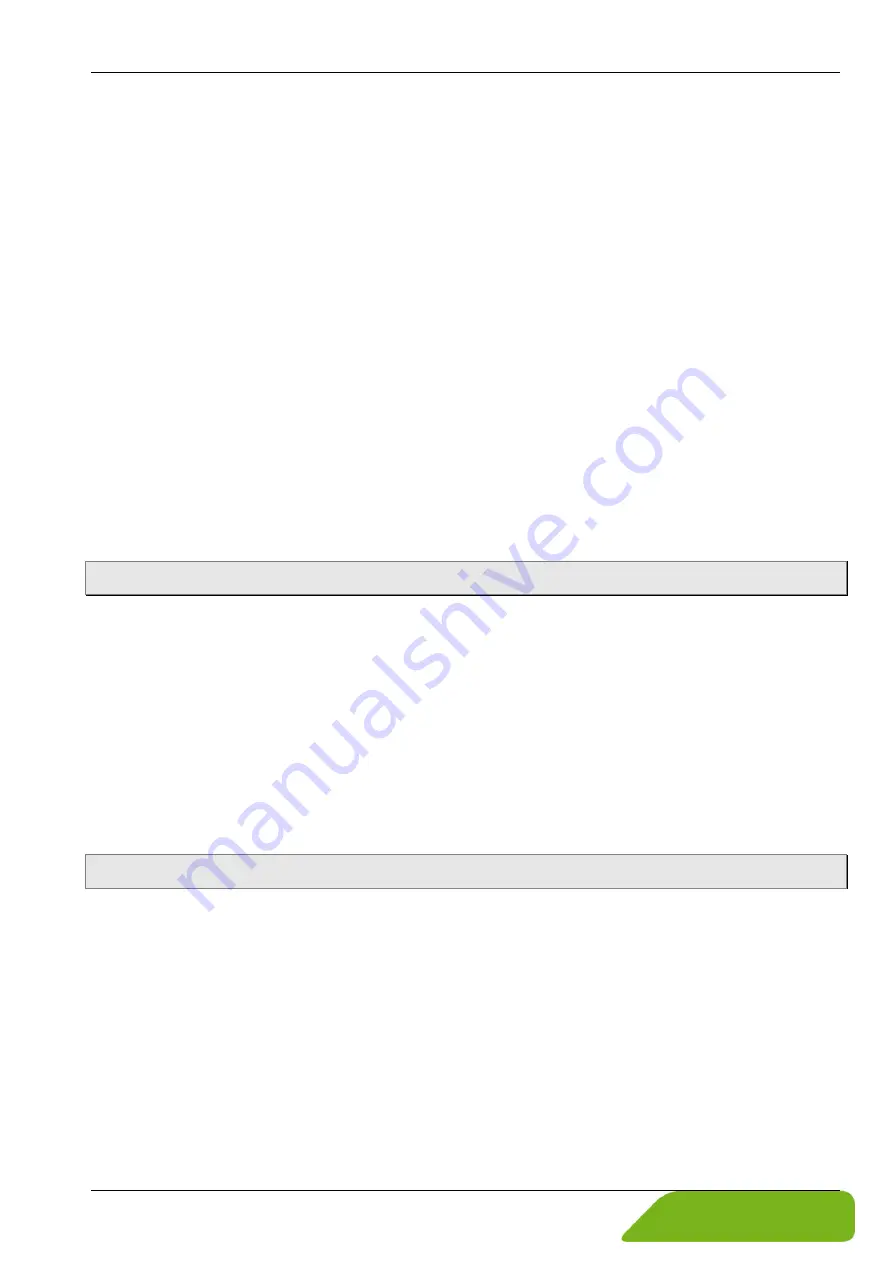
VTR
Installation of turbine meter
Technical changes reserved
- 21 -
•
If the turbine meter is installed directly after a pump, the length of the inlet section should
be twenty times greater than the pipe diameter. Furthermore, the installation position
should not be directly after a pipe bend. If there is a pipe bend, the inside bending radius
should be twice the size of the inside diameter of the turbine. If it is not possible to provide
the specified inlet sections, the use of a smoothing section, e.g. with a cross-shaped sec-
tion, is recommended.
•
Use conical pipe sections with a maximum angle of 20° to reduce the existing pipe diame-
ter.
•
If the turbine flow sensor is installed at the lower end of a tank, a smoothing section with a
cross-shaped section (deflector) should be installed between the tank and the turbine in
order to prevent turbulences in the turbine system.
•
The medium which is to be measured should contain as little particulate material as pos-
sible.
Possible particles should not be larger than 0.5 mm. If necessary, install a filter!
•
Prior to initial start-up the turbine flow sensor should be run for several hours at a mean
speed to minimise the bearing friction and to increase the service life.
3.2
Installation into pipe system
Now install the turbine meter into the pipe system which has been prepared in accord-
ance with chapter 3.1.
The threaded connections have a conical inner form and are suitable for Ermeto pipe fit-
tings.
The respective counter flanges for flanged connections have to be in accordance with DIN
or ANSI.
If the external thread has to be sealed, ensure that no fibrous sealant (hemp or Teflon
tape) enters the system.
3.3
Influence of viscosity
The turbine flow sensors have been calibrated for measuring water (viscosity 1 mm²/s). How-
ever, the measurement of high-viscosity liquids is possible. Please note the following effects:
•
The measuring range is reduced,
•
the linearity error increases,
•
the output frequency decreases.
In order to achieve acceptable linearity behaviour, the turbine should be operated in the up-
per part of the measuring range.
Respective special calibration of up to max. 200 mm²/s is possible.