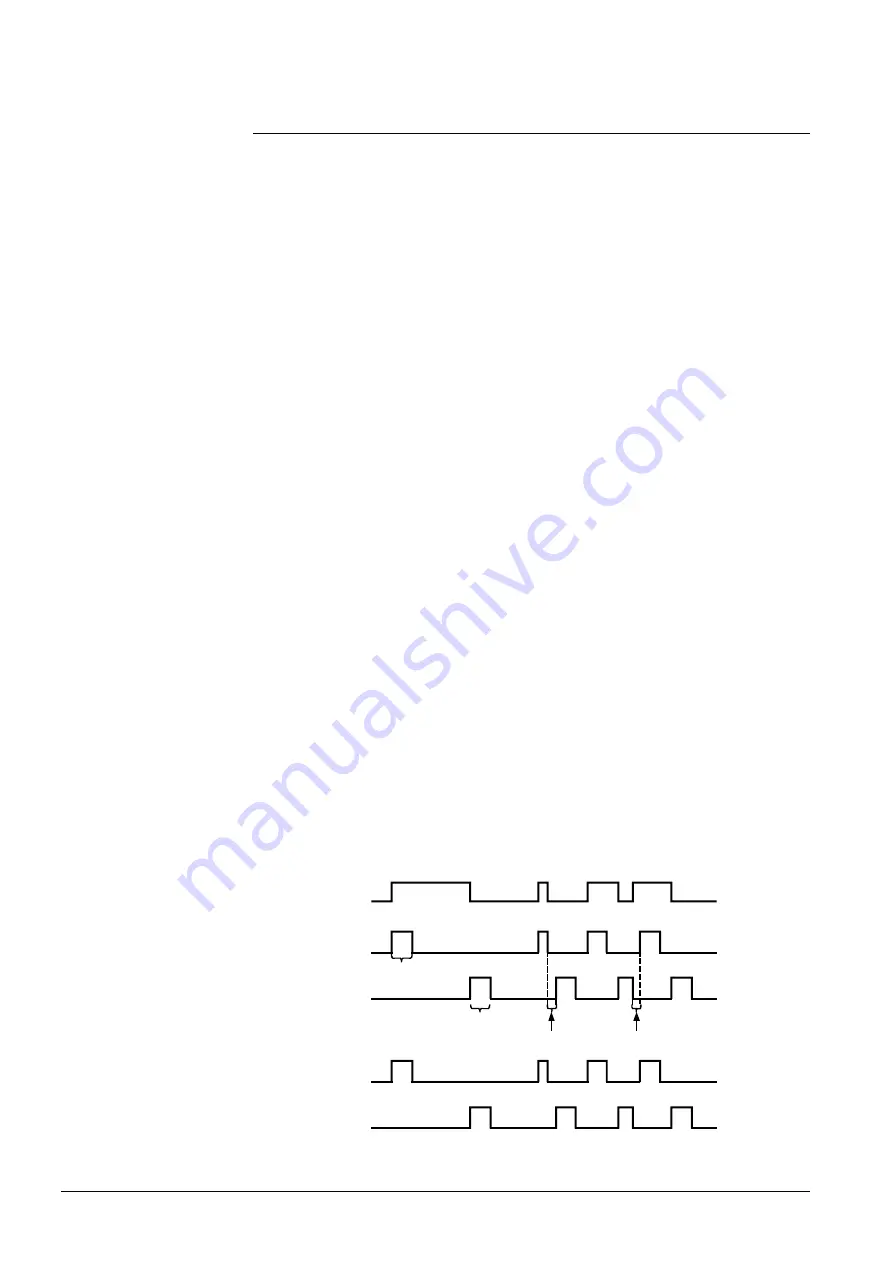
34/54
Siemens
TX-I/O™ Module system – Functions and operation
CM110561en_08
Building Technologies
Digital output functions
2018-10-25
5.5 Pulse, on/off
(BO Pulse On-Off / Q250-P250A-P)
Switching of single-stage electrical loads (electrical consumers)
•
1 N/O contact and 1 N/C contact for self-latching (Q250-P)
•
2 N/O contacts for two-coil switches
(250A-P)
The following functions can be implemented by use of external circuits (and see the
connection diagrams in the data sheets):
– If the control voltage for the self-latching mechanism fails, the loads are not
automatically enabled when power is restored, even in the case of manual override.
Example: power restoration circuit
– If the bus master fails, the loads are not disabled.
Example: lighting controls
– Two or more open loop control circuits can switch the same load.
– Override is also possible from one or more remote switching locations.
•
Connection diagrams: see module data sheets.
•
Step switches, pulse switches, bistable relays: see Q250, section 5.2.
•
The function uses two I/O points which must be on the same module and adjacent to
each other.
•
The TX-I/O relay modules have changeover contacts
•
The I/O point with the lower number (n) is used for the OFF command
•
The I/O point with the higher number (n+1) is used for the ON command
•
The process value can be written in "Normal" mode or in "Trigger" mode.
The latter option is used in cases where there is more than one source, e.g. with
lighting applications.
•
The pulse times can be set as parameters:
– 0.1...25.5 s (Parameter
Pulse Time
) (default = 0.5s)
–
P-bus BIM
: 0.5...25 s
•
The break time can be adjusted 0...25.5 (default = 0.1s)
•
P-bus BIM
: The break time is fixed to 0.1 s
Each change in the process value generates an ON or OFF command:
Process value
Relay (n+1)
"ON"
Relay (n)
"OFF"
Pulse/pause time
I/O status LED (n+1)
I/O status LED (n)
BreakTime
BreakTime
PulseTime
PulseTime
Active
Inactive
Relay Active
Relay Inactive
Relay Active
Relay Inactive
105
61
D
03
ON
OFF
ON
OFF
Application
Notes
Hardware
Function