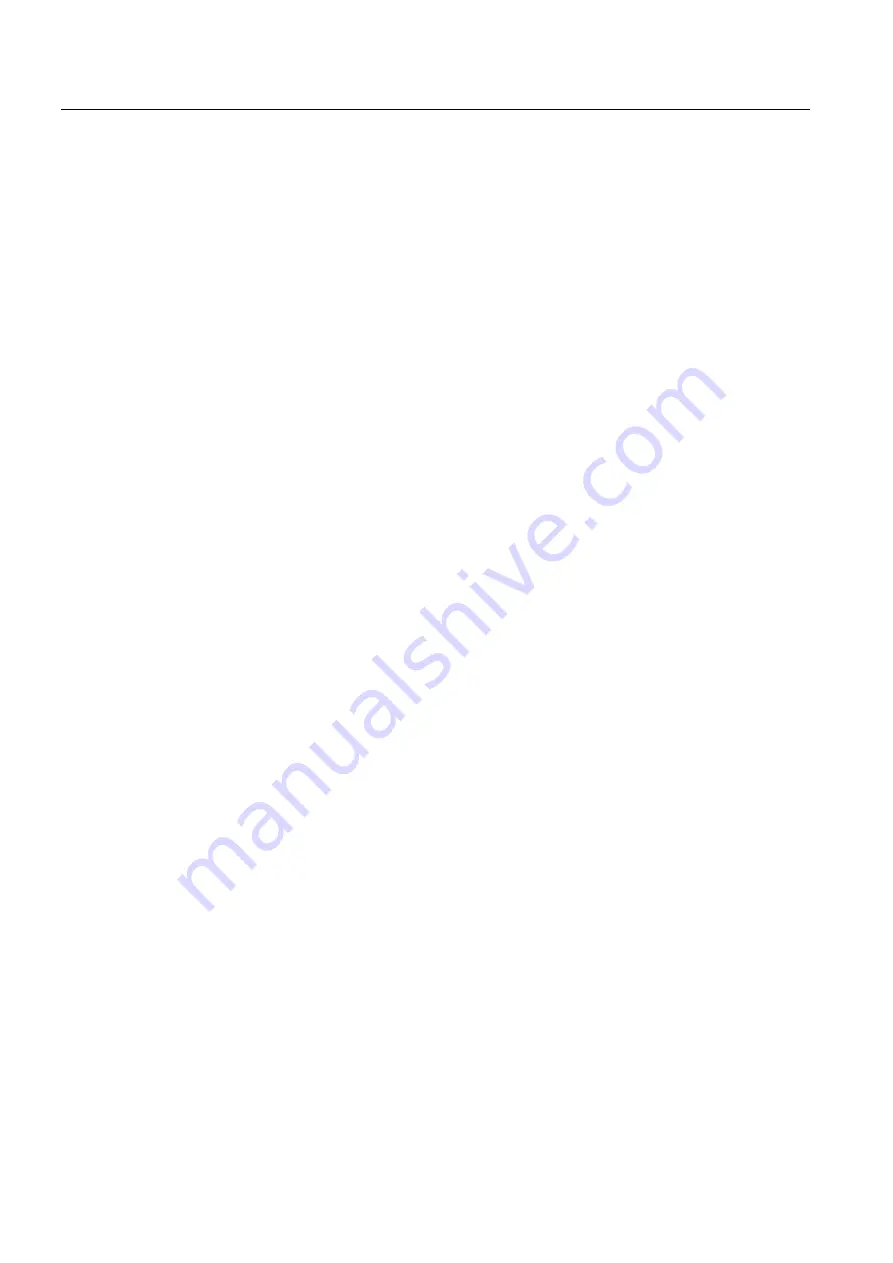
Detailed description
2.3 Channel
Basic logic functions: Mode group, channel, program operation, reset response (K1)
24
Function Manual, 11/2006, 6FC5397-0BP10-2BA0
Special cases
•
Errors during mode change
If a mode change request is rejected by the system, the error message "Operating mode
cannot be changed until after NC Stop" is output. This error message can be cleared
without changing the channel status.
•
Mode change disable
By means of the interface signal:
DB11, ... D0.4 (Mode change disable)
one can prevent mode changes.
This suppresses the mode change request.
The user must configure a message to the operator indicating that mode change is
disabled. No signal is set by the system.
•
Mode change from MDA to JOG
If all channels of the mode group are in RESET state after a mode change from MDA to
JOG, the NC switches from JOG to AUTO. In this state, part program commands
START
or
INIT
can be executed.
If a channel of the mode group is no longer in Reset state after a mode change, the part
program command
START
is rejected and Alarm 16952 is issued.
2.3
Channel
Assignment of programs
Part programs are assigned to channels. Programs of different channels are largely
independent of each other.
Channel properties
A channel constitutes an "NC" in which one part program can be executed at a time.
Machine axes, geometry axes and positioning axes are assigned to the channels according
to the machine configuration and the current program status (AXIS CHANGE, GEO AXIS
CHANGE, SETMS).
The system assigns each channel its own path interpolator with associated programming.
Each channel can run its own machining program, which is controlled from the PLC.
The following channelspecific functions make it possible for the channels to process part
programs independently:
•
Each channel has its own NC Start, NC Stop, RESET.
•
One feedrate override and one rapid traverse override per channel.
•
Dedicated interpreter for each channel.
•
Dedicated path interpolator for each channel, which calculates the path points such that
all the machining axes of the channel are controlled simultaneously from path axes.
•
Selection and deselection of tool cutting edges and their length and radius
compensations for a tool in a specific channel.
Summary of Contents for SINUMERIK 840D sl
Page 282: ...Index Basic logic functions Acceleration B2 64 Function Manual 11 2006 6FC5397 0BP10 2BA0 ...
Page 388: ...Basic logic functions Travel to fixed stop F1 Function Manual 11 2006 6FC5397 0BP10 2BA0 52 ...
Page 962: ...Index Basic logic functions Emergency Stop N2 20 Function Manual 11 2006 6FC5397 0BP10 2BA0 ...
Page 1704: ...Constraints Basic logic functions Spindles S1 94 Function Manual 11 2006 6FC5397 0BP10 2BA0 ...
Page 1716: ...Index Basic logic functions Spindles S1 106 Function Manual 11 2006 6FC5397 0BP10 2BA0 ...
Page 1996: ...Index Basic logic functions Tool Offset W1 208 Function Manual 11 2006 6FC5397 0BP10 2BA0 ...
Page 2150: ...Table of contents Basic logic functions Appendix 4 Function Manual 11 2006 6FC5397 0BP10 2BA0 ...
Page 2184: ...Glossary Basic logic functions Appendix 38 Function Manual 11 2006 6FC5397 0BP10 2BA0 ...