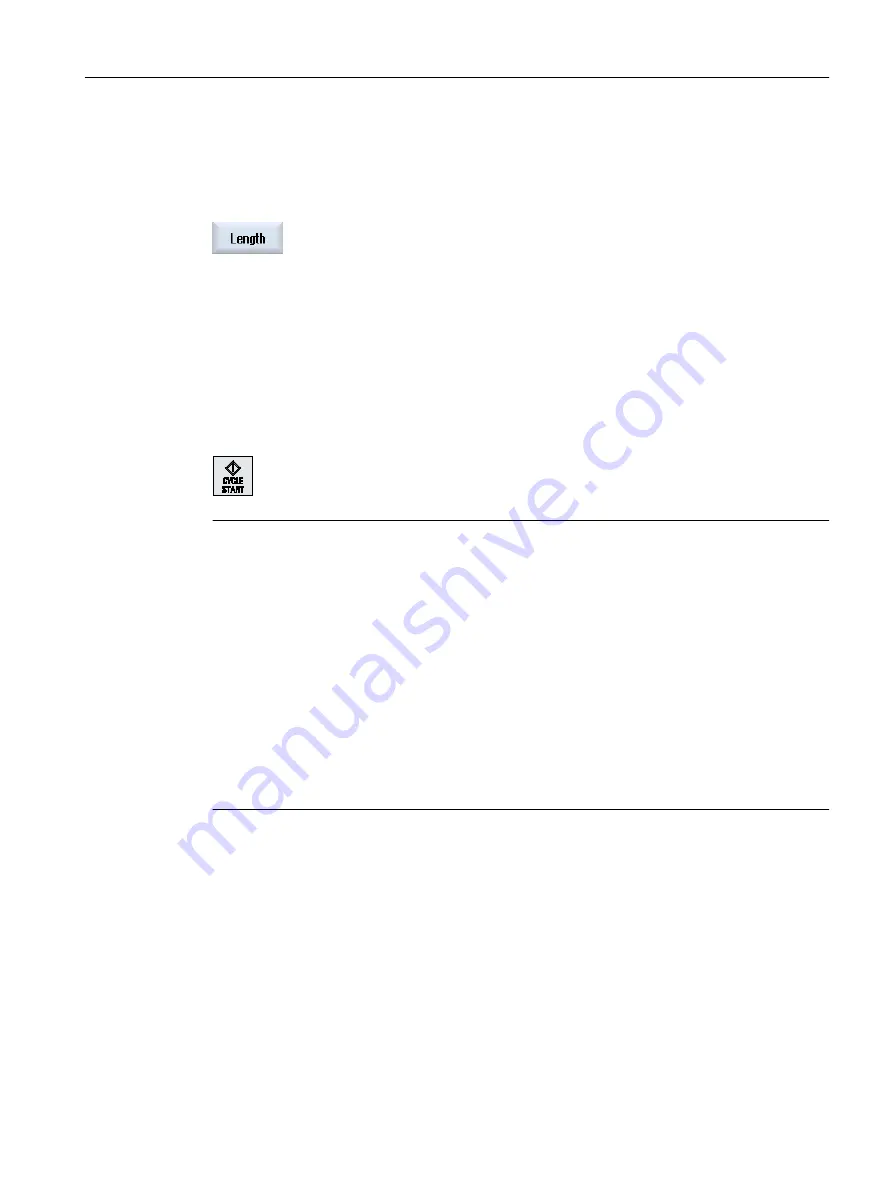
Calibration of length
9.
Move the workpiece probe over the reference surface.
10.
Press the "Meas. workp." and "Calibrate probe" softkeys.
The "Calibration: Probe" window opens.
11.
Press the "Length" softkey.
12.
Specify reference point Z0 of the surface, e.g. of the workpiece or the
machine table.
The length of the workpiece probe is determined.
13.
In the "Adjust tool length" selection box, choose "no" to save the deter‐
mined length difference in the calibration data set.
- OR -
Choose "yes" to calculate the length difference into the probe tool data.
Note
Please observe the information provided by the machine manufacturer.
14.
Press the <CYCLE START> key.
Calibration starts.
Note
User-specific defaults
● "Diameter, reference piece"
For the entry field "Diameter, reference piece", fixed values can be separately entered at
parameters for each probe number (calibration data set number). If these parameters are
assigned, the values saved there are displayed in the entry field "Diameter of the reference
piece"; however, they can no longer be changed there.
● "Height, reference piece"
For the entry field "Height, reference piece", fixed values can be separately entered at
parameters for each probe number (calibration data set number). If these parameters are
assigned, the values saved there are displayed in the entry field "Height of the reference
piece"; however, they can no longer be changed there.
Note
Please observe the information provided by the machine manufacturer.
4.6.13.2
Calibrate on sphere
When the electronic probes are attached to the spindle, clamping tolerances usually occur.
This can lead to measurement errors.
Using this measuring method, a workpiece probe can be calibrated at any position in space.
This has a special meaning in conjunction with swivel functions and transformations.
Setting up the machine
4.6 Measuring the workpiece zero
Milling
Operating Manual, 08/2018, 6FC5398-7CP41-0BA0
141