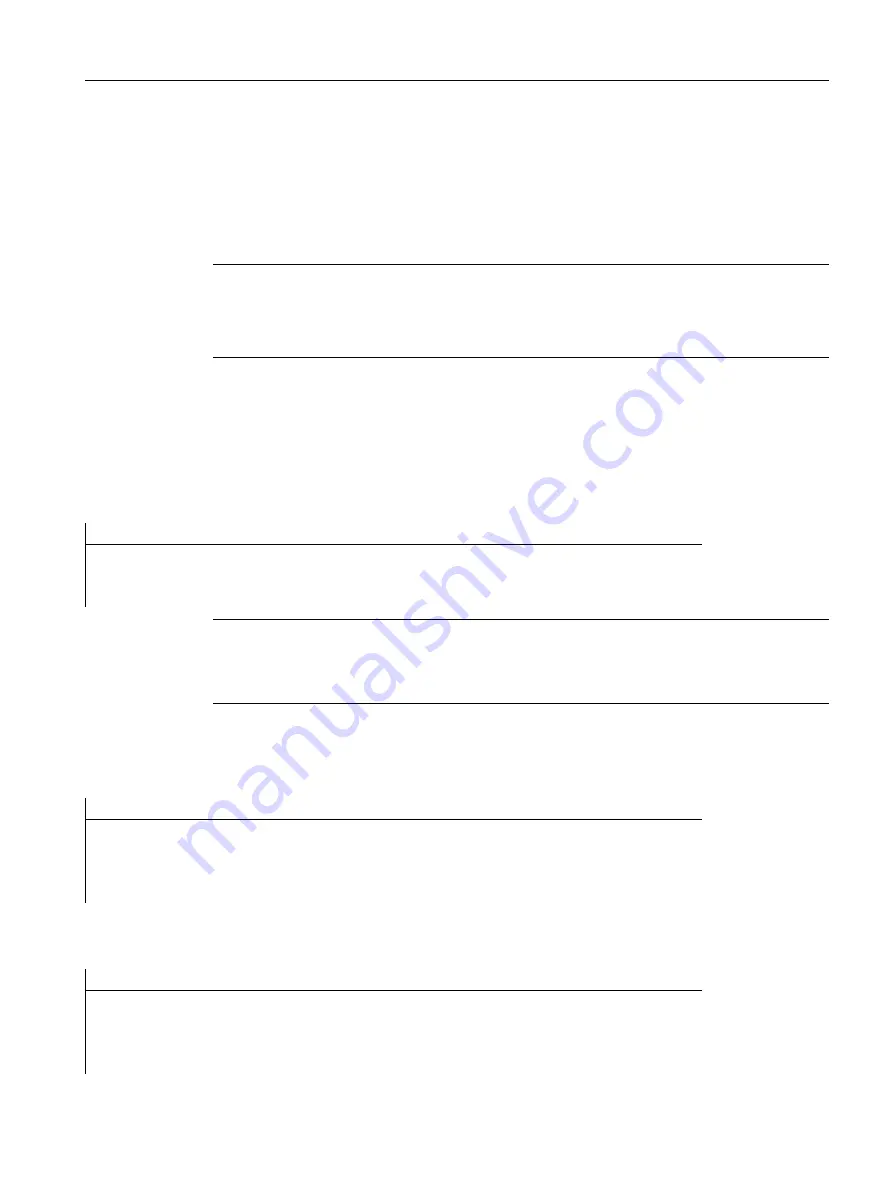
H2: Auxiliary function outputs to PLC
8.7 Programming an auxiliary function
Basic Functions
Function Manual, 09/2011, 6FC5397-0BP40-2BA0
431
8.7
Programming an auxiliary function
Syntax
An auxiliary function is programmed in a part program block with the following syntax:
<Type>[<Address extension>=]<Value>
Symbolic addressing
The values for the "address extension" and "value" parameters can also be specified symbolically. The symbolic
name for the address extension must then be stated in brackets.
Example:
Symbolic programming of the auxiliary function M3 (spindle right) for the first spindle:
Examples
Example 1: Programming of predefined auxiliary functions
Example 2: Programming examples of auxiliary functions with the corresponding values for output to the PLC
Note
If no address extension is programmed, the address extension is implicitly set = 0.
Predefined auxiliary functions with the address extension = 0 always refer to the master
spindle of the channel.
Program code
Comment
DEF SPINDEL_NR=1
; First spindle in the channel
DEF DREHRICHTUNG=3
; Clockwise direction of rotation
N100 M[SPINDEL_NR] = DREHRICHTUNG
; corresponding to: M1=3
Note
If you use symbolic names to program an auxiliary function, the symbolic name is not
transferred when the auxiliary function is output to the PLC. The corresponding numerical
value is transferred instead.
Program code
Comment
N10 M3
; "Spindle right" for the master spindle of the channel.
N20 M0=3
; "Spindle right" for the master spindle of the channel.
N30 M1=3
; "Spindle right" for the 1st spindle of the channel.
N40 M2=3
; "Spindle right" for the 2nd spindle of the channel.
Program code
Comment
DEF Coolant=12
; Output to PLC: - - -
DEF Lubricant=130
; Output to PLC: - - -
H[coolant]=lubricant
; Output to PLC: H12=130
H=coolant
; Output to PLC: H0=12