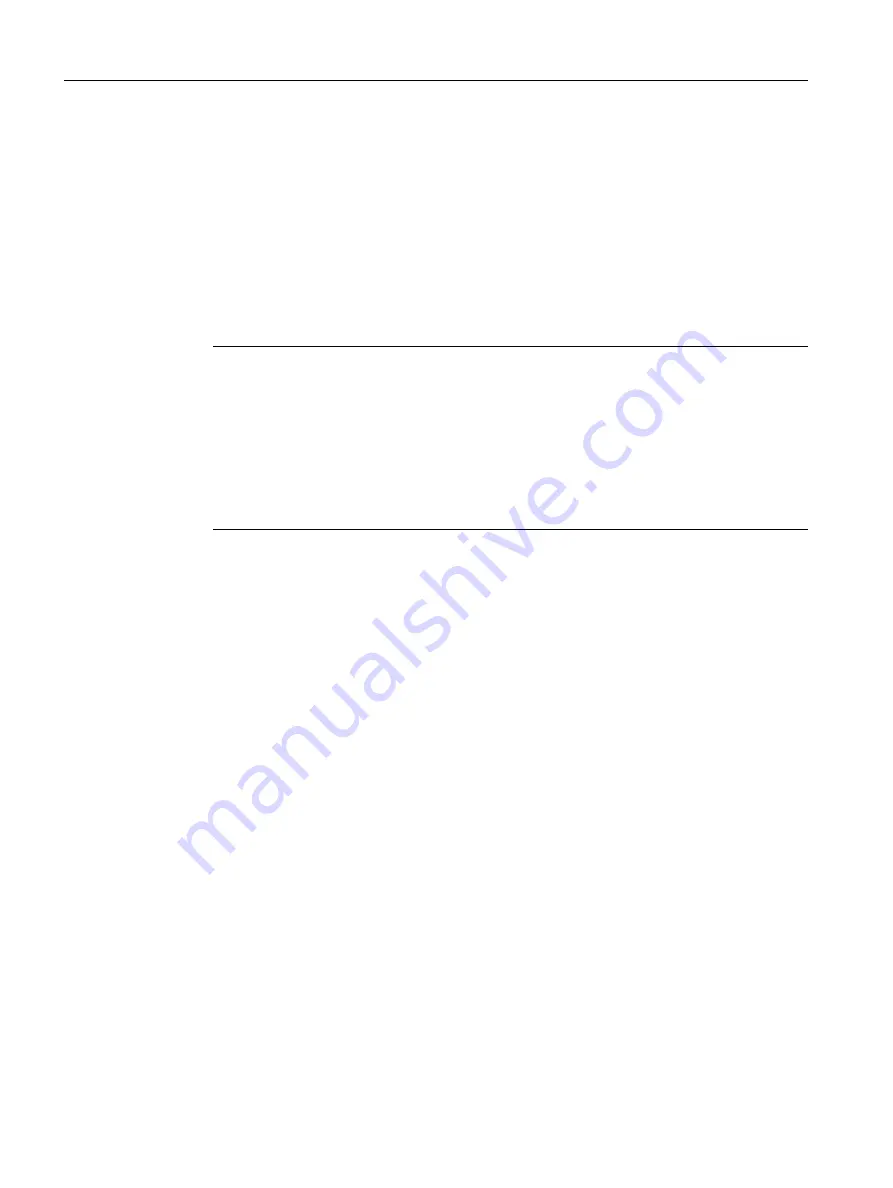
R1: Reference point approach
15.9 Referencing with absolute value encoders
Basic Functions
1246
Function Manual, 09/2011, 6FC5397-0BP40-2BA0
Example sequence of operation:
1. The NC reads the serial number of the absolute encoder for the measuring system of the machine axis in
question and the serial number is not equal to zero.
2. The absolute encoder is calibrated in the correct manner.
3. When the controller is powered up subsequently, the NC reads "zero" as the serial number of the absolute
encoder.
Serial number "zero" is ignored and the encoder status remains the same, that is "calibrated".
4. When the controller is powered up, the NC again reads the serial number it read under Item 1 and that is still
indicated in the machine data. The encoder status continues to be "Adjusted".
15.9.9
Enabling the measurement system
The measuring system of a machine axis is activated in the following cases:
• Power up of the control (POWER ON)
• Activation of the measuring system via interface signal (deselection of "parking"):
DB31, ... DBB1.5 / 1.6 (position measuring system 1/2)
DB31, ... DBB2.1 (servo enable)
• Violation of the assigned encoder limit frequency (spindles):
MD36300 $MA_ENC_FREQ_LIMIT
When the measuring system is activated, the NC synchronizes the actual value system of the machine axis with
the current absolute value. Traversing is disabled during synchronization for axes but not for spindles.
Parameterizing the encoder limit frequency (spindles)
The EQN 1325 absolute encoder made by Heidenhain has an incremental track and an absolute track.
If a spindle is driven at a speed above the encoder limit frequency of the incremental track, the substantially lower
limit frequency of absolute track must be parameterized as the encoder limit frequency.
MD36300 $MA_ENC_FREQ_LIMIT
Otherwise an incorrect absolute position would be read because the parameterized encoder limit frequency is not
reached when the measuring system is activated. This would cause a position offset in the actual value system of
the machine axis.
Note
PROFIBUS drives
As not every drive connected via PROFIBUS-DP is able to deliver the encoder serial
number in time for build-up of control or at all, the range of the encoder serial number with
PROFIBUS drives is pre-set with zero to avoid unnecessary new NC internal
adjustments:
MD34232 $MA_EVERY_ENC_SERIAL_NUMBER = 0
A manual parameterizing to 1 is ineffective.