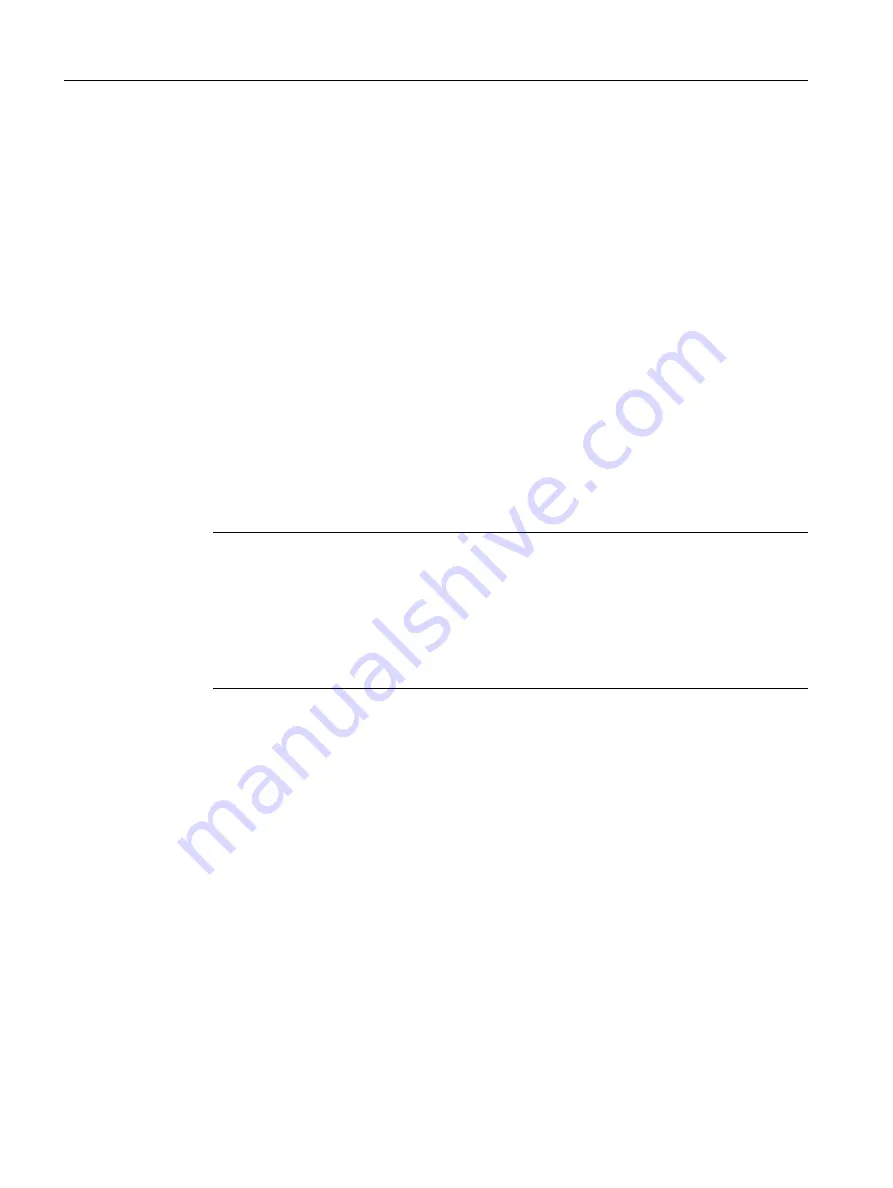
R1: Reference point approach
15.9 Referencing with absolute value encoders
Basic Functions
1238
Function Manual, 09/2011, 6FC5397-0BP40-2BA0
15.9.3
Adjustment by entering a reference point value
Function
During adjustment by entering the reference point value, the absolute position of the machine axis with reference
to the machine zero point is determined by e.g.:
• Position measurement (e.g. laser interferometer)
• Moving the machine axis to a known position (e.g. fixed stop)
This determined position value will be made known to the NC as the reference point value. The NC then
calculates the reference point offset from the difference between the encoder absolute value and the reference
point value.
Procedure
1. Set reference mode to "Take over of the reference point value"
MD34200 $MA_ENC_REFP_MODE = 0
2. Traversing machine axis in the JOG mode to the (e.g. Laser interferometer) position to be measured or
already known (e.g. fixed stop).
3. Communicate the position of the machine axis relative to machine zero to the NC as the reference point
value:
MD34100 $MA_REFP_SET_POS =
Position
4. Releasing encoder adjustment:
MD34210 $MA_ENC_REFP_STATE = 1
5. Activate NCK-Reset for acceptance of the entered machine data values.
6. Switch to JOG-REF mode.
Note
The machine axis can only be traversed in the direction enabled for referencing with the
travel keys:
MD34010 $MA_REFP_CAM_DIR_IS_MINUS (approach reference point in minus
direction)
To avoid an invalid position because of backlash in the drive train, the known position
must be approached at low velocity.