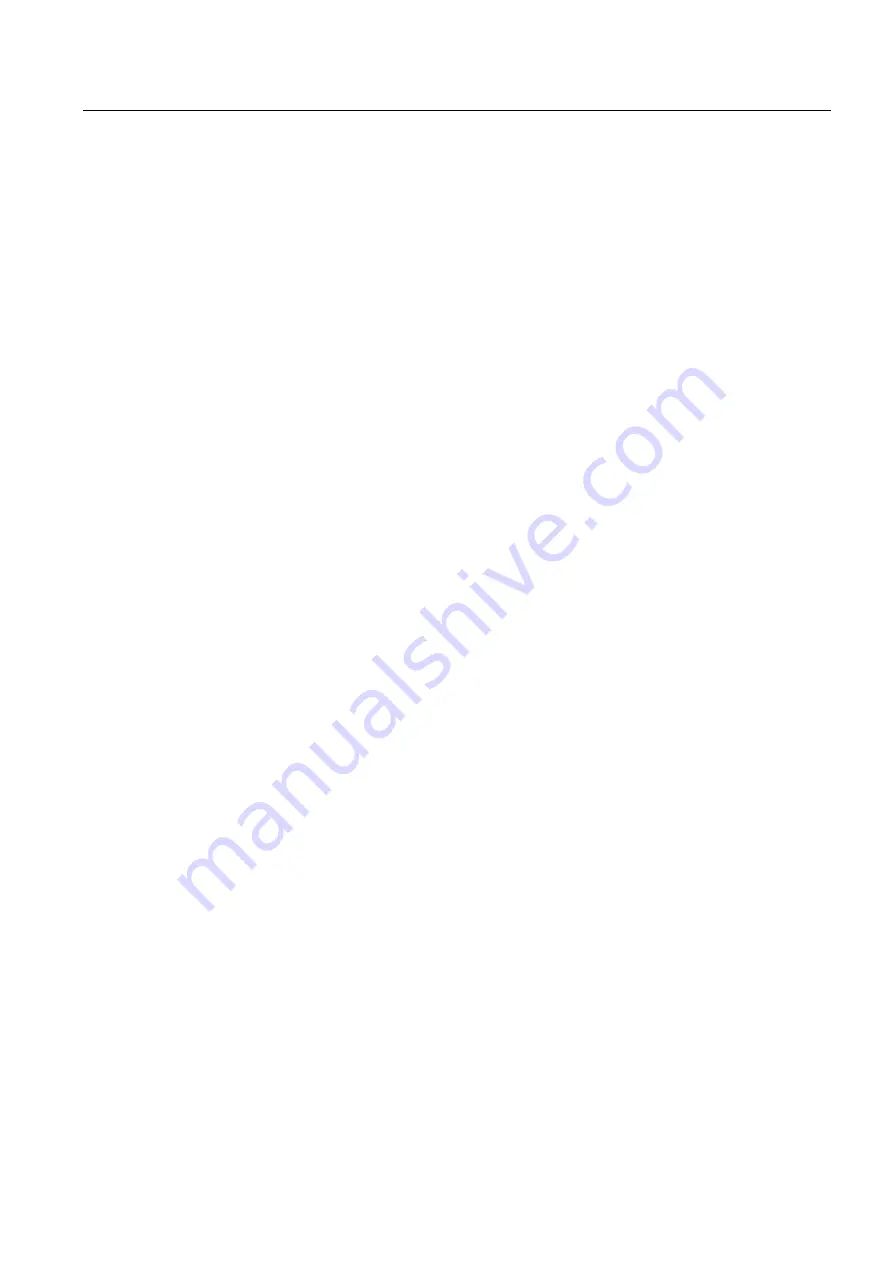
Axis Monitoring (A3)
2.4 Monitoring of static limits
Turning, Milling, Nibbling
Function Manual, 11/2012, 6FC5397-1CP10-5BA0
51
If the hardware limit switch is crossed, the PLC signals this to the NC via IS "Hardware limit
switch plus/minus" (V380x 1000.1 or .0) and the movement of all axes is stopped. The
braking method can be specified via MD36600 BRAKE_MODE_CHOICE (braking behavior
at hardware limit switch).
Effectiveness
HW limit switch monitoring is active after the control has started up in all modes.
Effect
●
When a hardware limit switch is passed in either direction, alarm 21614 "Hardware limit
or -" is triggered.
●
The axis is stopped according to the setting in MD36600 BRAKE_MODE_CHOICE
(braking behavior at hardware limit switch).
●
If the axis is assigned to an interpolatory grouping with other axes, then these are also
stopped according to the method selected in MD36600 BRAKE_MODE_CHOICE
(braking behavior at hardware limit switch).
●
The direction keys in the approach direction are disabled.
Remedy
●
Reset
●
Move in the opposite direction (in JOG mode)
●
Correct the program
2.4.2
Software limit switches
Function
They are used to limit the maximum traversing range on each individual axis.
There are two pairs of software limit switches for each machine axis. They are defined in the
machine axis system using the following machine data:
MD36100 POS_LIMIT_MINUS (1st software limit switch minus)
MD36110 POS_LIMIT_PLUS (1st software limit switch plus)
MD36120 POS_LIMIT_MINUS2 (2nd software limit switch minus)
MD36130 POS_LIMIT_PLUS2 (2nd software limit switch plus)