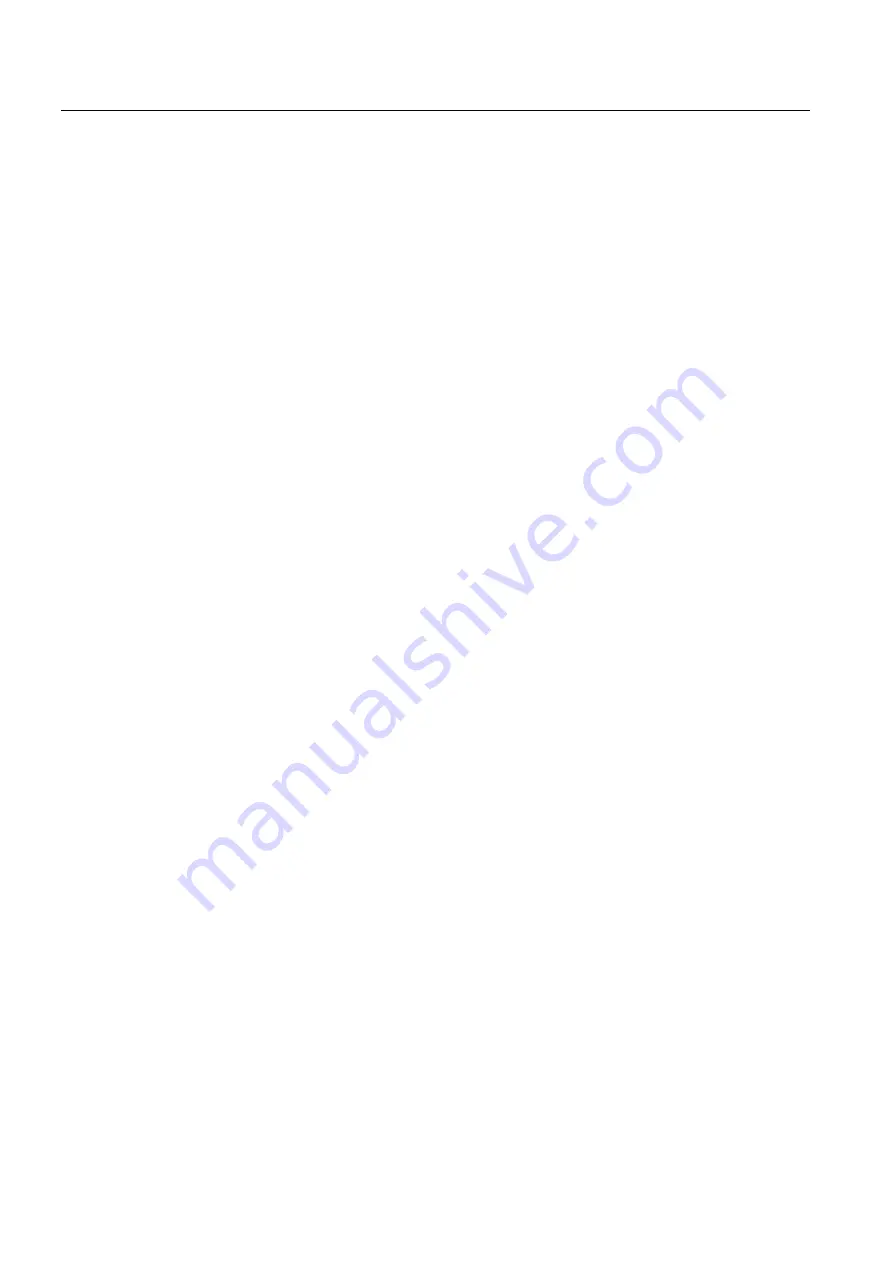
Axis Monitoring (A3)
2.3 Encoder monitoring functions
Turning, Milling, Nibbling
48
Function Manual, 11/2012, 6FC5397-1CP10-5BA0
The actual velocity monitoring is active for axes and spindles.
Effect
If the "Threshold for velocity monitoring" is exceeded the following occurs:
●
Alarm 25030 "Actual velocity alarm limit" is triggered
●
The affected axis/spindle is brought to a standstill with rapid stop (with open position
control loop) along a speed setpoint ramp. The braking ramp time is set in MD36610
AX_EMERGENCY_STOP_TIME (duration of the braking ramp for error states).
●
If the axis/spindle is assigned to an interpolatory grouping with other axes/spindles, then
these are also braked by rapid stop with following error reduction (default for partial
position setpoint = 0).
Troubleshooting tips
●
Check actual values
●
Check position control direction (control sense)
●
Check MD36200 AX_VELO_LIMIT (threshold value for velocity monitoring)
●
Check speed setpoint cable for analog spindles
2.3
Encoder monitoring functions
2.3.1
Encoder limit frequency monitoring
Function
If the permissible limit frequency of a measuring system entered in MD36300
ENC_FREQ_LIMIT (encoder limit frequency) is exceeded, the positional synchronization
(reference point) between the machine and control system will be lost. Correct position
control is no longer possible. This state is signaled to the PLC.
Effectiveness
The encoder limit frequency monitoring is always active when the encoder is switched on
and is active on axes and spindles.