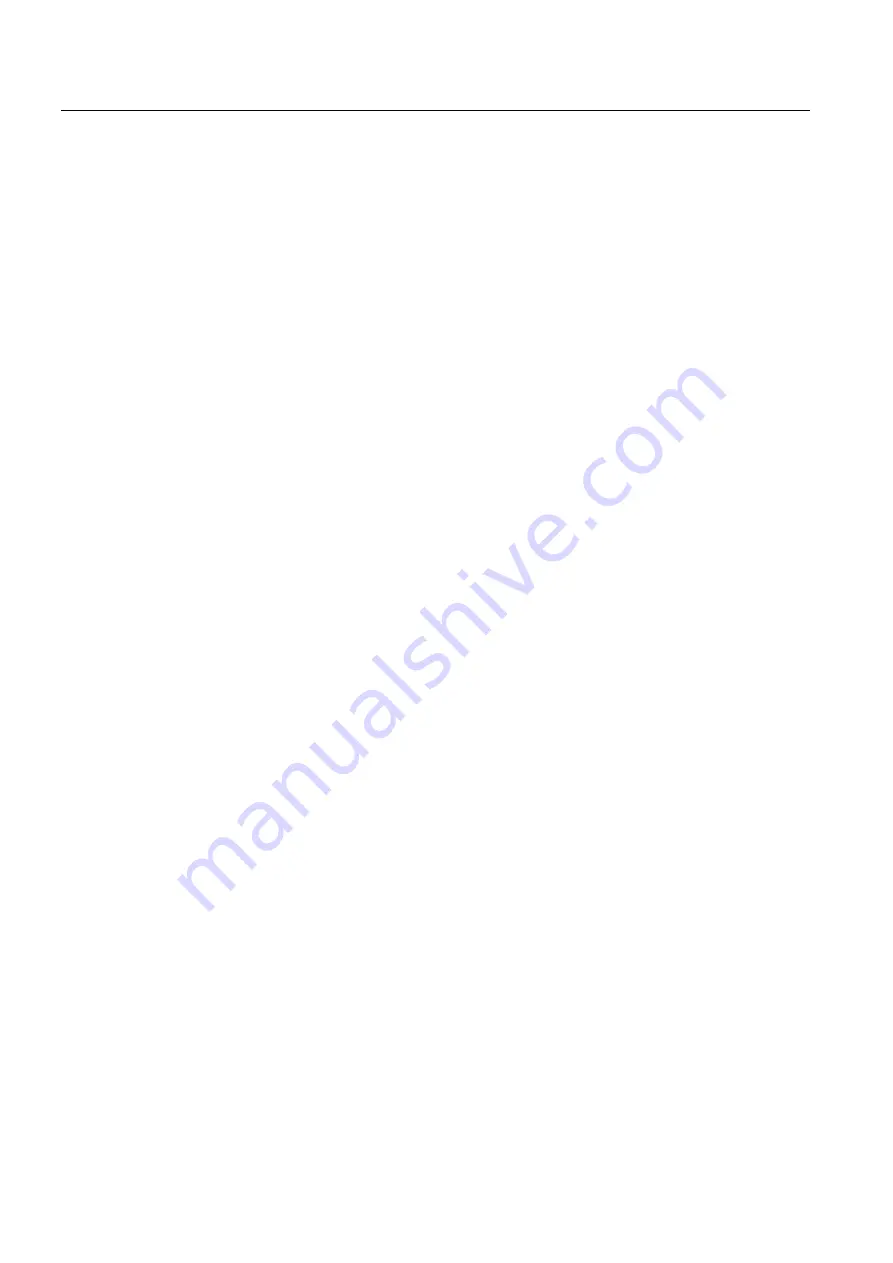
Axis Monitoring (A3)
2.2 Motion monitoring functions
Turning, Milling, Nibbling
42
Function Manual, 11/2012, 6FC5397-1CP10-5BA0
Effectiveness
Contour monitoring is active for axes and position-controlled spindles.
Effect
If the contour deviation is too large, this has the following effect:
●
Alarm 25050 "Contour monitoring" is triggered
●
The axis/spindle is brought to a standstill via a speed setpoint ramp with rapid stop (with
open position control loop).
The braking ramp time is set in
MD36610 AX_EMERGENCY_STOP_TIME (braking ramp time for error states).
●
If the axis/spindle is involved in interpolation with other axes/spindles, these are brought
to a standstill with rapid stop with following error reduction (position setpoint = constant).
Remedy
●
Increase tolerance band of monitoring in MD36400
●
The actual "servo gain factor" must correspond to the desired servo gain factor set via
MD32200 POSCTRL_GAIN (servo gain factor).
With analog spindles:
MD32260 RATED_VELO (rated motor speed) and
MD32250 RATED_OUTVAL (rated output voltage) must be checked.
●
Check optimization of the speed controller
●
Check smooth running of the axes
●
Check machine data for traversing movements
(feed override, acceleration, max. speeds, ... )
2.2.2
Position monitoring
Function
In order to ensure that an axis reaches the required position within a specified time, the timer
that can be configured in MD36020 POSITIONING_TIME (time delay exact stop
fine) is started at the end of each motion block (setpoint has reached target) and, when the
timer runs out, a check made to ascertain whether the axis has reached its setpoint within
the tolerance of MD36010 STOP_LIMIT_FINE (exact stop fine).
For details on "Exact stop coarse and fine" see Chapter "Continuous Path Mode, Exact Stop
and Look-Ahead (B1)"