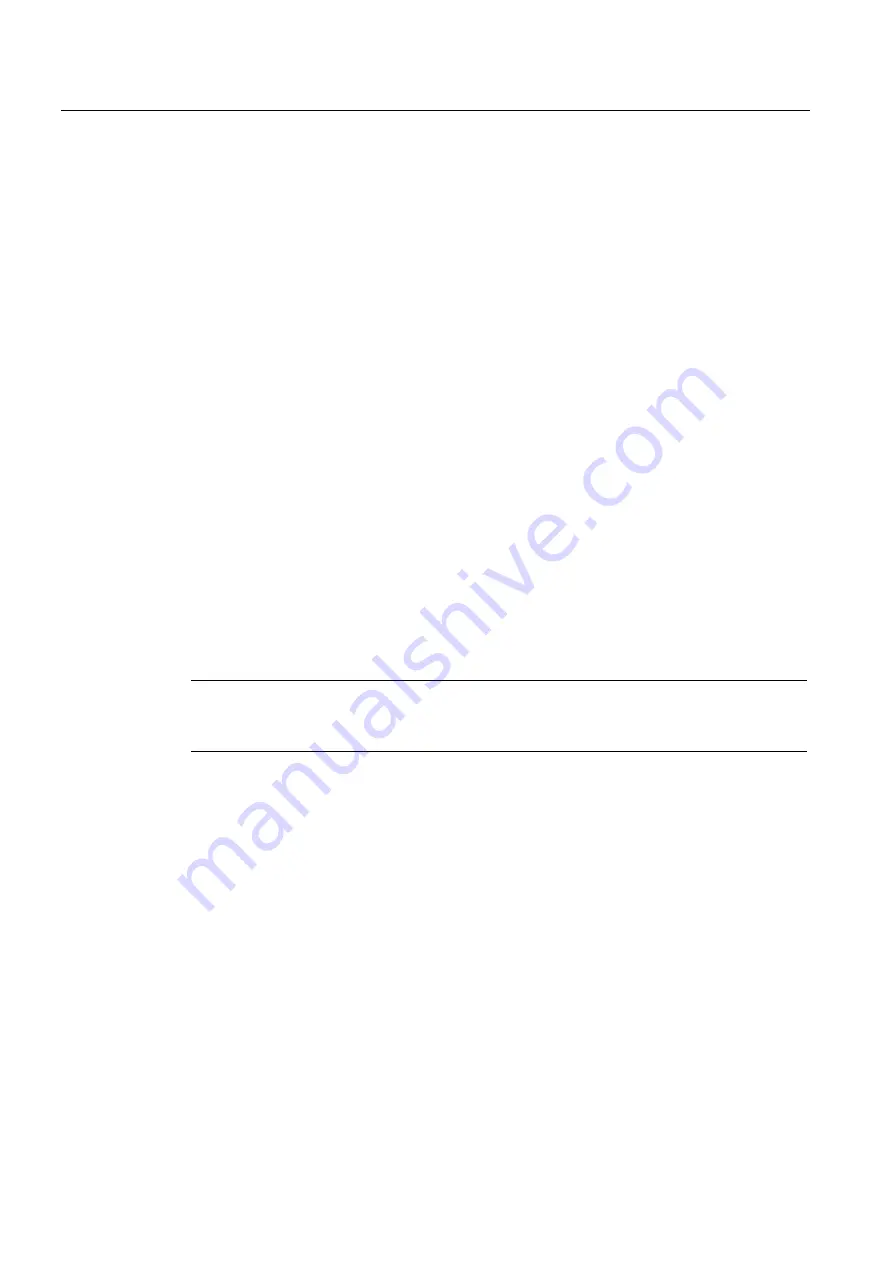
Speed/torque coupling, master-slave (TE3)
23.8 Axial interface signals
Turning, Milling, Nibbling
400
Function Manual, 11/2012, 6FC5397-1CP10-5BA0
23.8
Axial interface signals
When a master/slave coupling is requested, the PLC axis enables "Servo enable"
(V380x 0002.1) and "Pulse enable" (V380x 4001.7) of the slave axis are derived directly
from the specifications of the master axis. The separate PLC axis enable signals have no
effect.
Removing the servo enable in the master axis also results in an interpolated deceleration of
the slave axis that is carried out within the time configured for MD36610. The associated
speed and current servo enables for individual axes will only be removed once the time for
MD36620 has elapsed.
To continue to ensure the same braking response is carried out, where possible the time set
in the following machine data should be the same for all coupled axes:
MD36620 SERVO_DISABLE_DELAY_TIME
The same applies to the following drive parameters:
●
p9560 (pulse suppression, shutdown speed)
●
p1228 (pulse suppression, delay time)
If the "Current controller active" (V390x 0001.7) or "Speed controller active" (V390x 0001.6)
drive status signals are missing in the master or slave axis, the PLC interface signal
"Master/slave active" (V390x 5000.7) is reset in the slave axis while it is at a standstill. When
the master and slave axes return to closed-loop control mode, IS "Master/slave active" is set
on the slave axis.
The PLC activates the torque compensation controller using the following IS: V380x 5000.4.
The status of the torque compensation controller can be read in IS "Master/slave comp.
contr. active" (V390x 5000.4).
Note
If the coupling is closed, the slave axis is speed-controlled, meaning that status signal
"Position controller active" (V390x 0001.5) is not set.
23.9
Axial monitoring functions
Except monitoring the speed setpoint and actual speed, axial monitoring functions like
contour and standstill in the slave axis are inactive because of the missing position
controller. The position control circuit parameters like gain factor, precontrol, balancing can
thus be set differently for master and slave axes without initiating the monitoring functions.
To achieve the same braking response for all coupled axes in the event of a fault, the same
alarm reaction is applied to the entire coupling grouping when the coupling is active.
When correcting fault states, repositioning of slave axes on the interrupt point is suppressed.