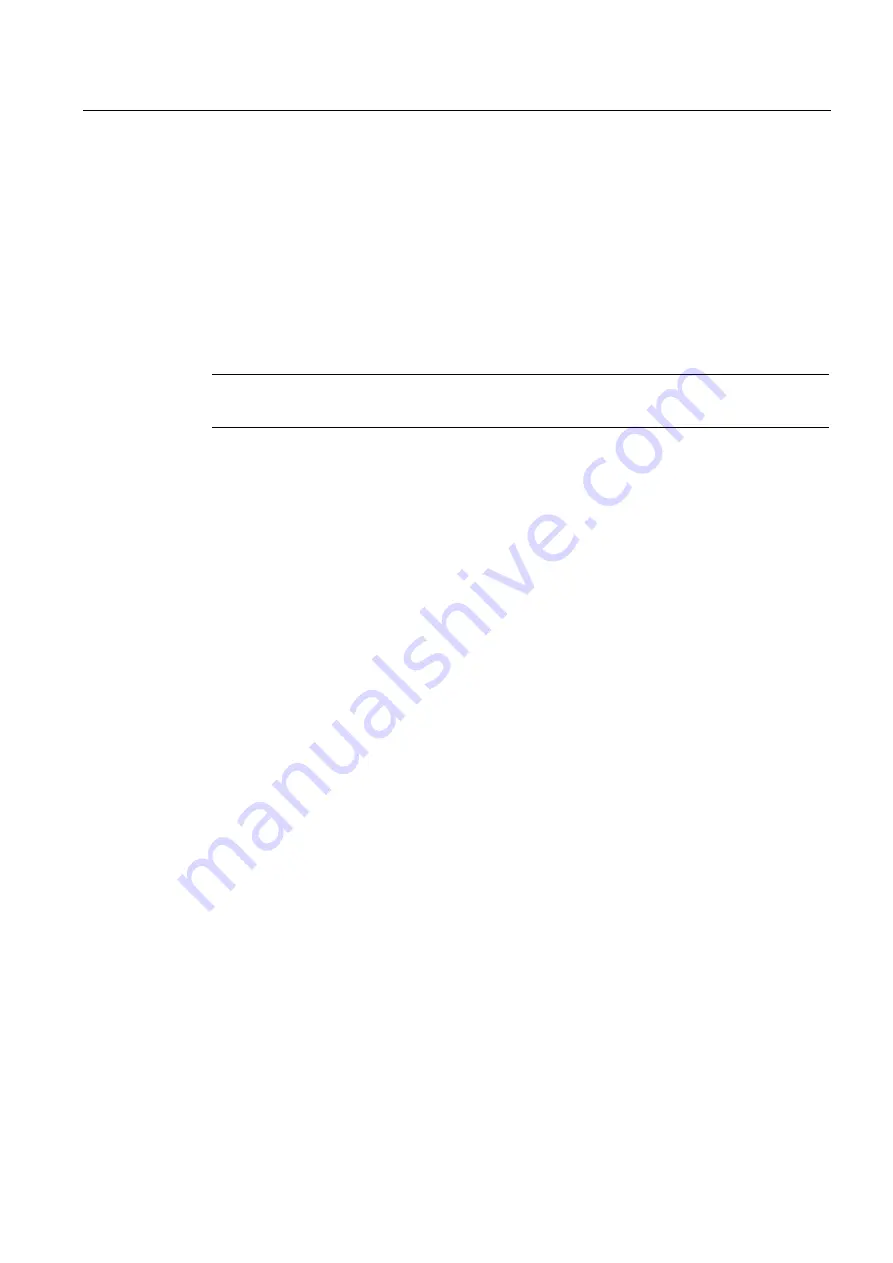
Spindle (S1)
20.7 2nd spindle / master spindle
Turning, Milling, Nibbling
Function Manual, 11/2012, 6FC5397-1CP10-5BA0
363
Block change with SPOS
If the spindle is being positioned with SPOS, the block change will be dependent on the end
point monitoring with the IS "Position reached with exact stop fine". All other functions
programmed in the block must have achieved their end criterion (e.g. axes ready, all
auxiliary functions acknowledged by the PLC).
20.7
2nd spindle / master spindle
Note
This function is not available for the 802D sl value.
Function
The TRANSMIT and TRACYL kinematic transformation functions are available for milling on
lathes. These functions require a second spindle for the driven milling tool. The main spindle
is operated as a rotary axis with these functions.
Master spindle
A series of functions is connected to the master spindle, which are only possible for this
spindle:
G95
Rev. feedrate
G96, G97
Constant cutting rate
LIMS
Upper speed limit for G96, G97
G33, G34, G35, G331, G332
Thread cutting, thread interpolation
M3, M4, M5, S...
Simple specifications for direction of rotation, stop and
speed
The master spindle is defined via configuration (machine data). Generally it is the main
spindle (spindle 1).
A different spindle can be defined as master spindle in the program:
SETMS(n)
Spindle n (= 1 or 2) is the master spindle as of now
Switching back can also be performed via:
SETMS
Configured master spindle is now master spindle again
or
SETMS (1)
Spindle 1 is now master spindle again