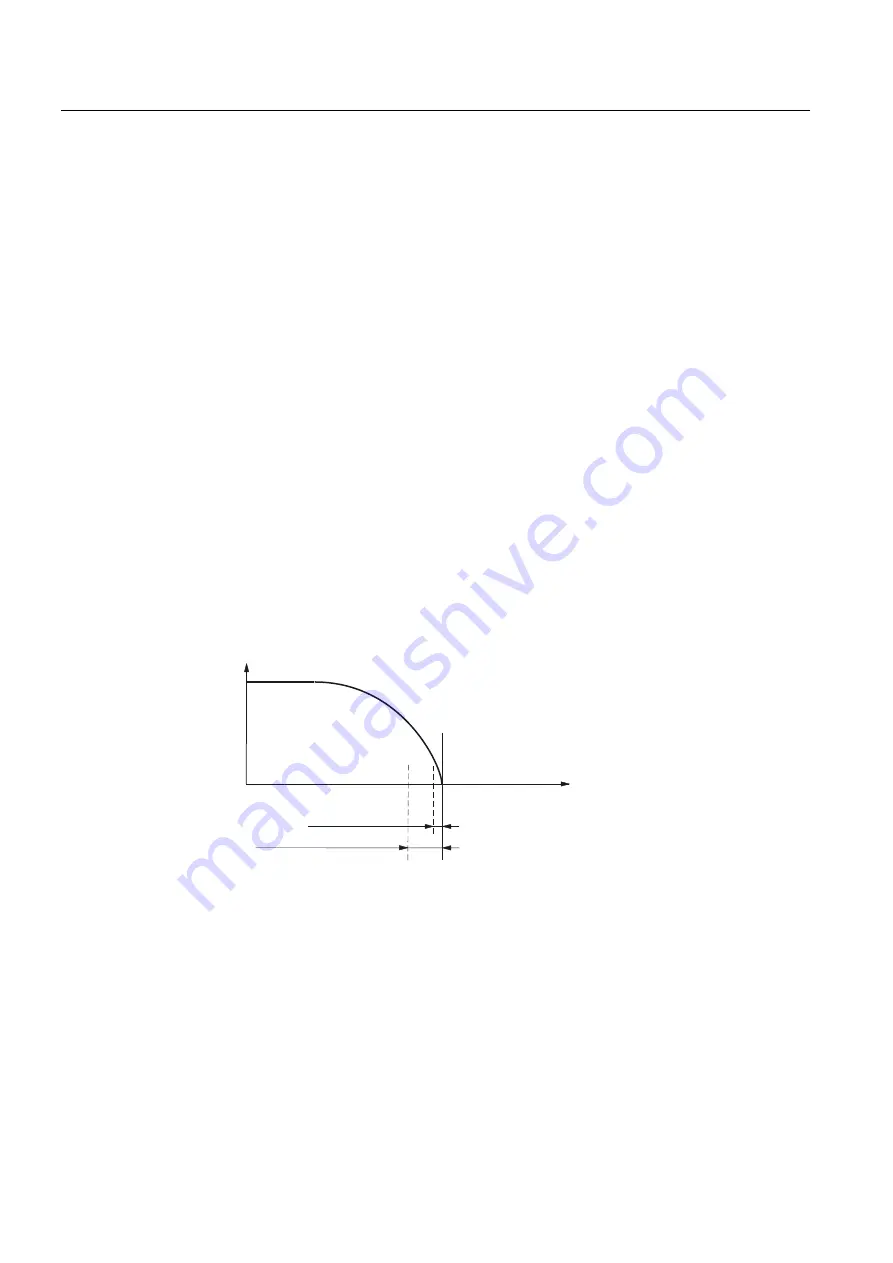
Spindle (S1)
20.6 Spindle monitoring
Turning, Milling, Nibbling
362
Function Manual, 11/2012, 6FC5397-1CP10-5BA0
If the encoder limit frequency is exceeded, the IS "Referenced/synchronized" V390x 0000.4)
is reset for the measurement system and IS "Encoder limit frequency 1 exceeded" (V390x
0000.2) is enabled.
If the maximum encoder limit frequency has been exceeded and the speed subsequently
falls below the encoder frequency in MD36302 ENC_FREQ_LIMIT_LOW (% value of
MD36300 ENC_FREQ_LIMIT), the spindle is automatically synchronized with the next zero
mark or the next BERO signal.
20.6.6
Target point monitoring
Function
During positioning (the spindle is in "positioning mode"), the system monitors the distance
from the spindle (with reference to the actual position) to the programmed spindle set
position (target point).
Two limit values can be defined as incremental path (starting at the spindle set position) in
the following machine data.
●
MD36000 STOP_LIMIT_COARSE (exact stop limit coarse)
●
MD36010 STOP_LIMIT_FINE (exact stop limit fine)
Regardless of the two limit values, the positioning of the spindle is always as accurate as the
connected spindle measurement encoder, the backlash, the transmission ratio, etc.
6HWSRVLWLRQ
3RVLWLRQ
([DFWVWRSOLPLWFRDUVH
([DFWVWRSOLPLWILQH
6SHHG
Figure 20-10 Exact stop zones of a spindle for positioning
IS: Position reached with exact stop ...
When the limits MD 36000 and MD 36010 are reached, IS "Position reached with exact stop
coarse" (V390x 0000.6) and IS "Position reached with exact stop fine" (V390x 0000.7) are
output to the PLC.