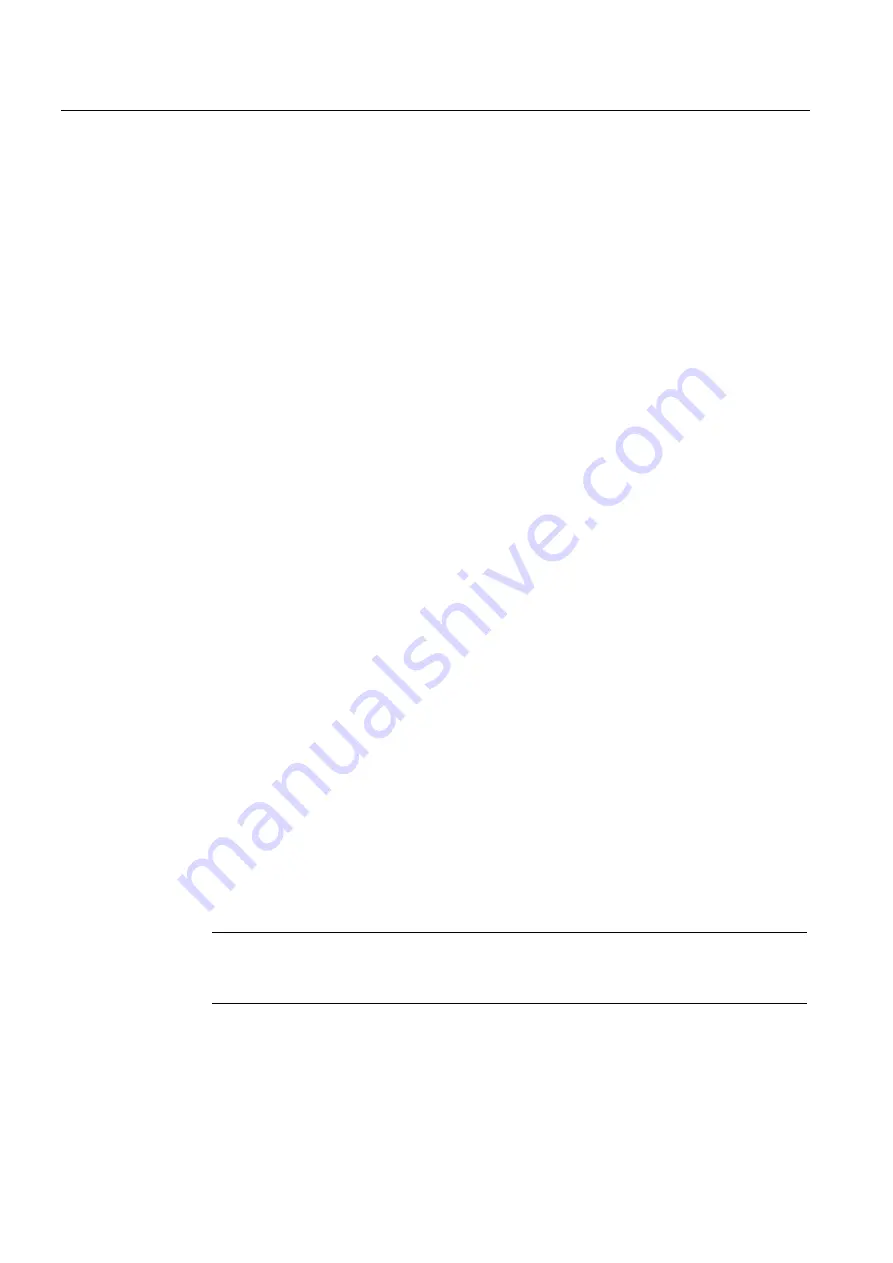
Reference Point Approach (R1)
18.4 Referencing with absolute encoders
Turning, Milling, Nibbling
328
Function Manual, 11/2012, 6FC5397-1CP10-5BA0
18.4
Referencing with absolute encoders
18.4.1
General
Requirements
An axis with absolute encoder is referenced automatically when the control is switched on if
the system detects that the relevant axis is already calibrated. This transfer of the absolute
value takes place without any axis motion, e.g. at POWER ON. Two conditions must be
fulfilled before an axis can be automatically referenced:
●
The axis has an absolute encoder with which the position control operates
●
The Absolute encoder has been calibrated (MD34210 ENC_REFP_STATE = 2)
Adjustment
In the case of axes with absolute encoders, the measurement system is not synchronized by
approaching a reference cam. It is calibrated instead. For this purpose, the actual value of
the absolute encoder is set once during start-up and transferred to the control.
18.4.2
Operator-assisted calibration
Basic procedure
Move the axis to be calibrated to a defined position to set the resulting actual value.
Chronological sequence
1.
Set MD34200 ENC_REFP_MODE and MD34210 ENC_REFP_STATE to 0 and activate
by means of a POWER ON. Parameter ENC_REFP_MODE = 0 means that the actual
value of the axis is set once.
2.
Traverse axis manually in JOG mode to a known position. The direction in which the
position is approached must match the direction stored in MD34010
REFP_CAM_DIR_IS_MINUS (0 = positive direction, 1 = negative direction).
Note
This known position must always be approached at a low velocity and from a defined
direction so that it is not falsified by any backlash present in the drive train.