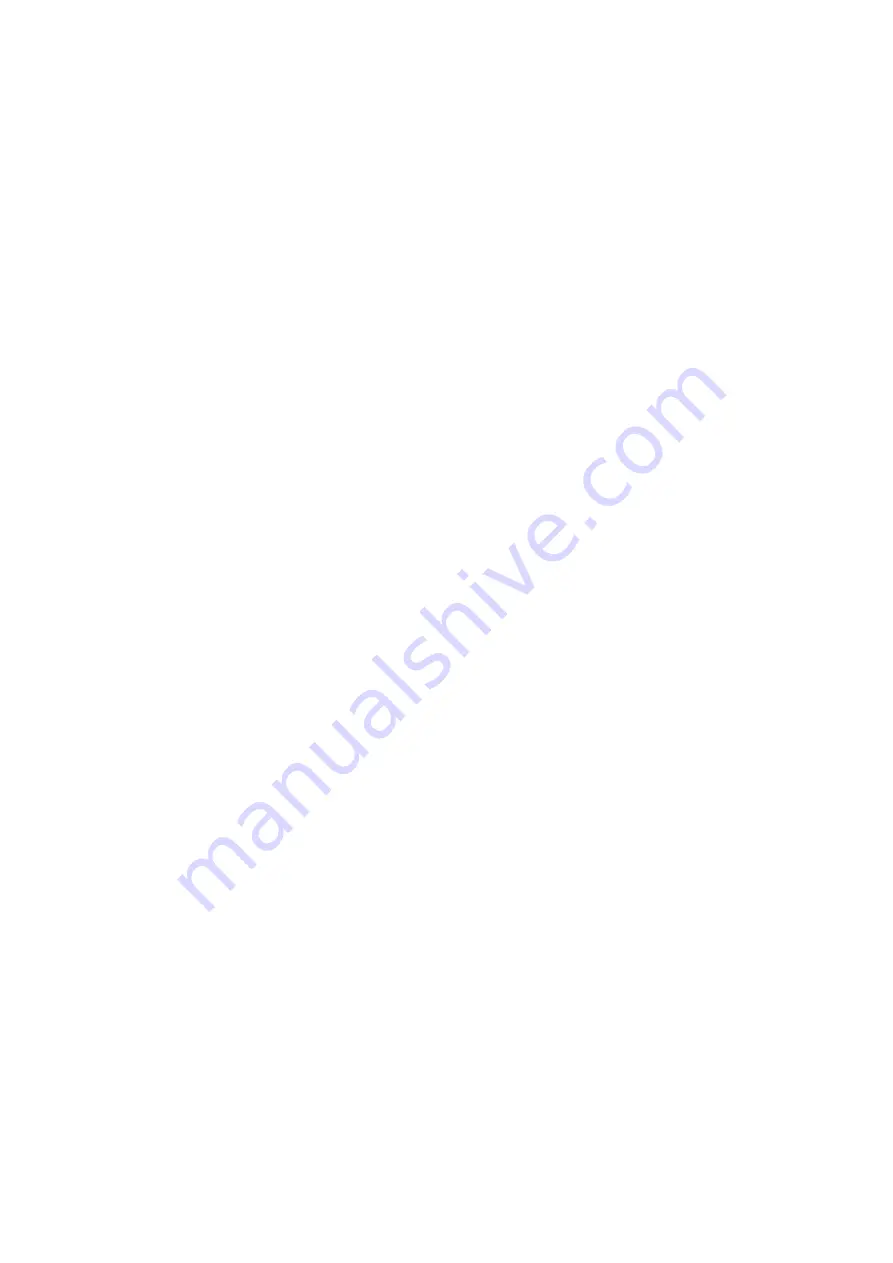
Turning, Milling, Nibbling
Function Manual, 11/2012, 6FC5397-1CP10-5BA0
315
Reference Point Approach (R1)
18
18.1
Fundamentals
Why reference?
The control must be synchronized with the position measurement system of each machine
axis so that the control can detect the exact machine zero when it is switched on. This
process is known as referencing.
The spindle process (synchronizing) is largely described in the Chapter "Spindles".
Position measurement systems
The following position measuring systems can be mounted on the motor:
●
Incremental rotary measuring system
●
Absolute rotary measuring system
The referencing for the mounted position measuring systems can be set with
MD34200 ENC_REFP_MODE (referencing mode).
Output cam
An output cam for referencing may be required for linear axes, and its signal has the
following tasks:
●
Selection of the direction of travel when approaching the zero mark (synchronized pulse)
●
Selection of the zero mark, where required.
BERO
A BERO (inductive proximity switch) can be deployed as the encoder for the synchronized
pulse (instead of the zero mark of the position encoder) (preferred for rotary axes, spindles).
Here connection is made to the 802D sl via terminal X20. Special inputs to BERO inputs are
switched via macro parameterization.
Reference:
/BE/ 802D sl Instruction Manual, Section "Configuring SINAMICS S120 with 802D sl"
IS "Active machine function REF" (V3100 0001.2)
The reference point approach is performed with the REF machine function activated (IS
"active machine function REF"). The REF machine function can be selected in JOG modes
(IS "REF machine function" (V3000 0001.2)).