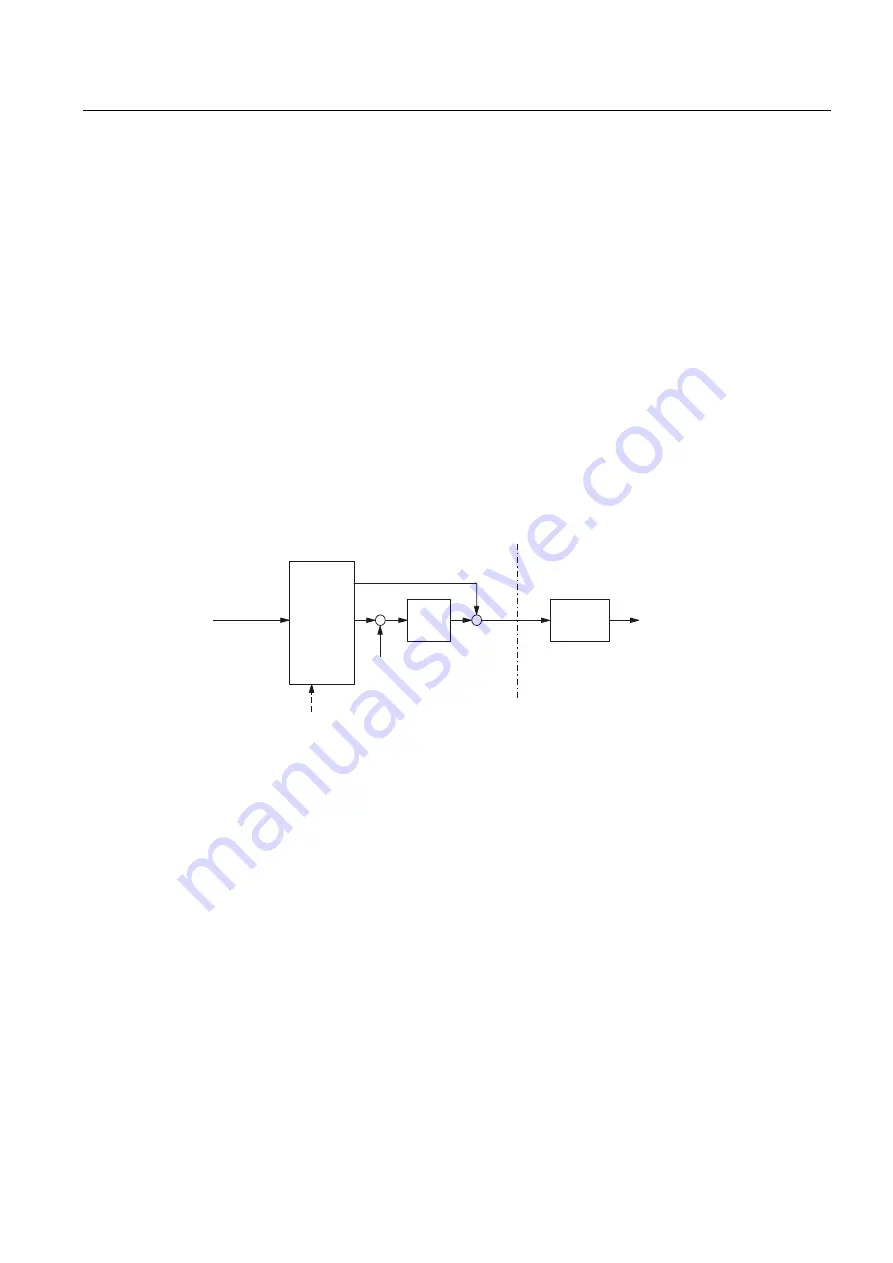
Compensation (K3)
11.4 Following error compensation (feedforward control)
Turning, Milling, Nibbling
Function Manual, 11/2012, 6FC5397-1CP10-5BA0
227
Optimization of control loop
The feedforward control is set on an axis/spindle-specific basis. First of all, the current
control loop, speed control loop and position control loop must be set to an optimum for the
axis/spindle.
Reference:
/BE/ Operating Instructions
Parameter assignments
The feedforward control parameters must then be assigned to the relevant axis/spindle and
then entered in the machine data (see next section).
11.4.2
Speed feedforward control
In the case of speed feedforward control, a velocity setpoint is also applied directly to the
input of the speed controller (see figure below).
0'(48,9B63(('&75/B7,0(
'ULYH
1&.
3RVLWLRQ
DFWXDOYDOXH
6SHHG
FRQWUROOHU
3RVLWLRQ
FRQWURO
OHU
UHIHUHQFH
YDOXH
6HWSRLQW
)HHGIRUZDUG
FRQWURO
Figure 11-8 Speed feedforward control
Parameters
In order to achieve a correctly set speed feedforward control, the equivalent time constant of
the speed control loop must be determined exactly and entered as machine data
MD32810 EQUIV_SPEEDCTRL_TIME (equivalent time constant of the closed speed control
loop) during commissioning.