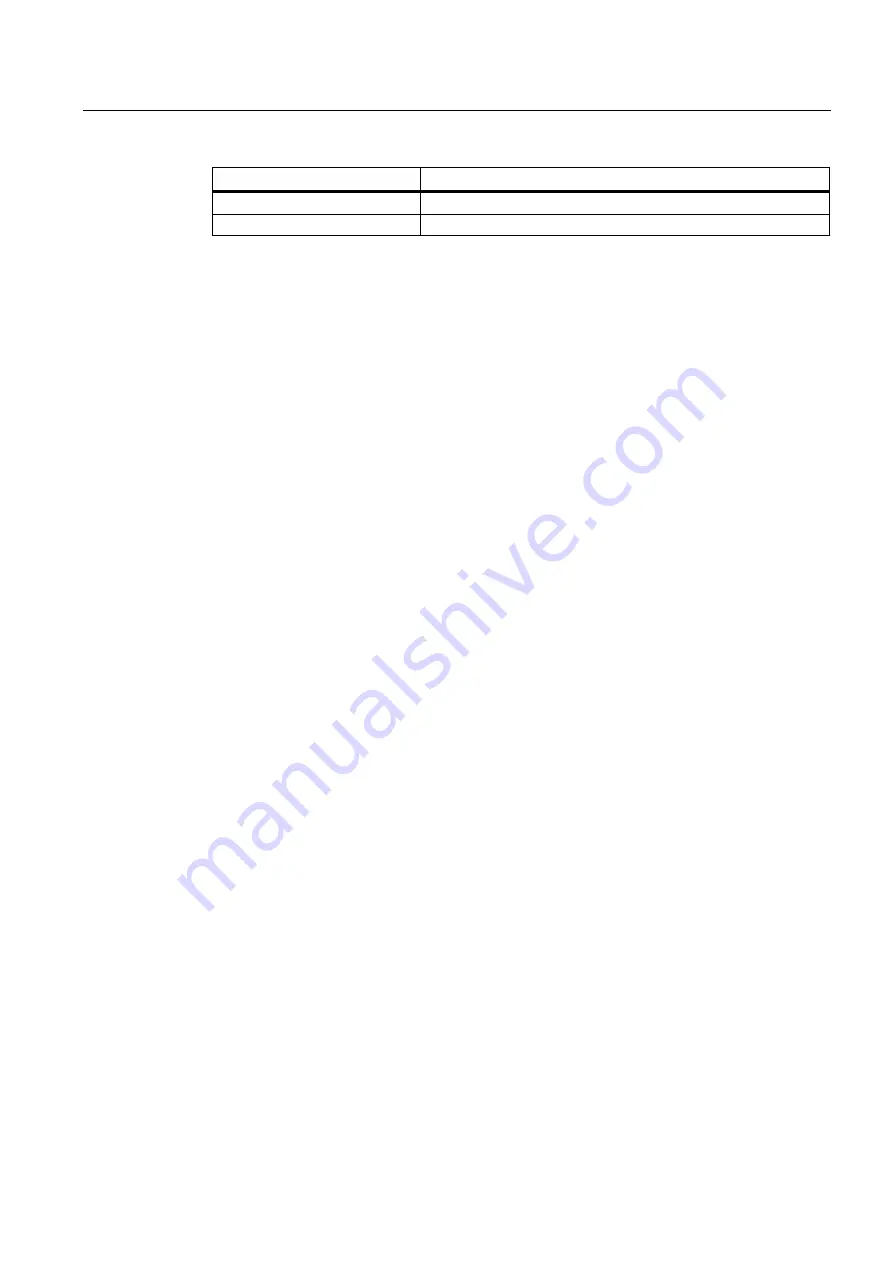
Auxiliary Function Outputs to PLC (H2)
9.3 Transfer of values and signals to the PLC interface
Turning, Milling, Nibbling
Function Manual, 11/2012, 6FC5397-1CP10-5BA0
159
Programming
Output of H function to the PLC
H17=3.5
H17=3.5
H5.3=21
Error, alarm 14770
Block change
A new auxiliary function output from the NCK to the PLC is only possible after the PLC has
acknowledged all transferred auxiliary functions. Auxiliary functions are present in the user
interface for at least one PLC cycle. A block is considered as completed when the
programmed movement has been completed and the auxiliary function has been
acknowledged. To do so, the NCK stops the part program processing if necessary to ensure
that no auxiliary functions are lost from the PLC user program's point of view.
9.3
Transfer of values and signals to the PLC interface
Time of transfer
In the case of auxiliary functions which are output at the end of a block (e.g. M2), the output
is only made after all axis movements and the SPOS movement of the spindle have been
completed.
If several auxiliary functions with different output types (prior, during, at end of motion) are
programmed in one motion block, then they are output individually according to their output
type.
In a block without axis movements or SPOS movement of the spindle, the auxiliary functions
are all output immediately in a block.
Continuous-path mode
A path movement can only remain continuous if auxiliary function output takes place during
the movement and is acknowledged by the PLC before the path end is reached, see Chapter
"Continuous Path Mode (B1)".
Interface signals
Transfer of the signals from NCK to the PLC:
Reference:
/LIS/ SINUMERIK 802D sl lists