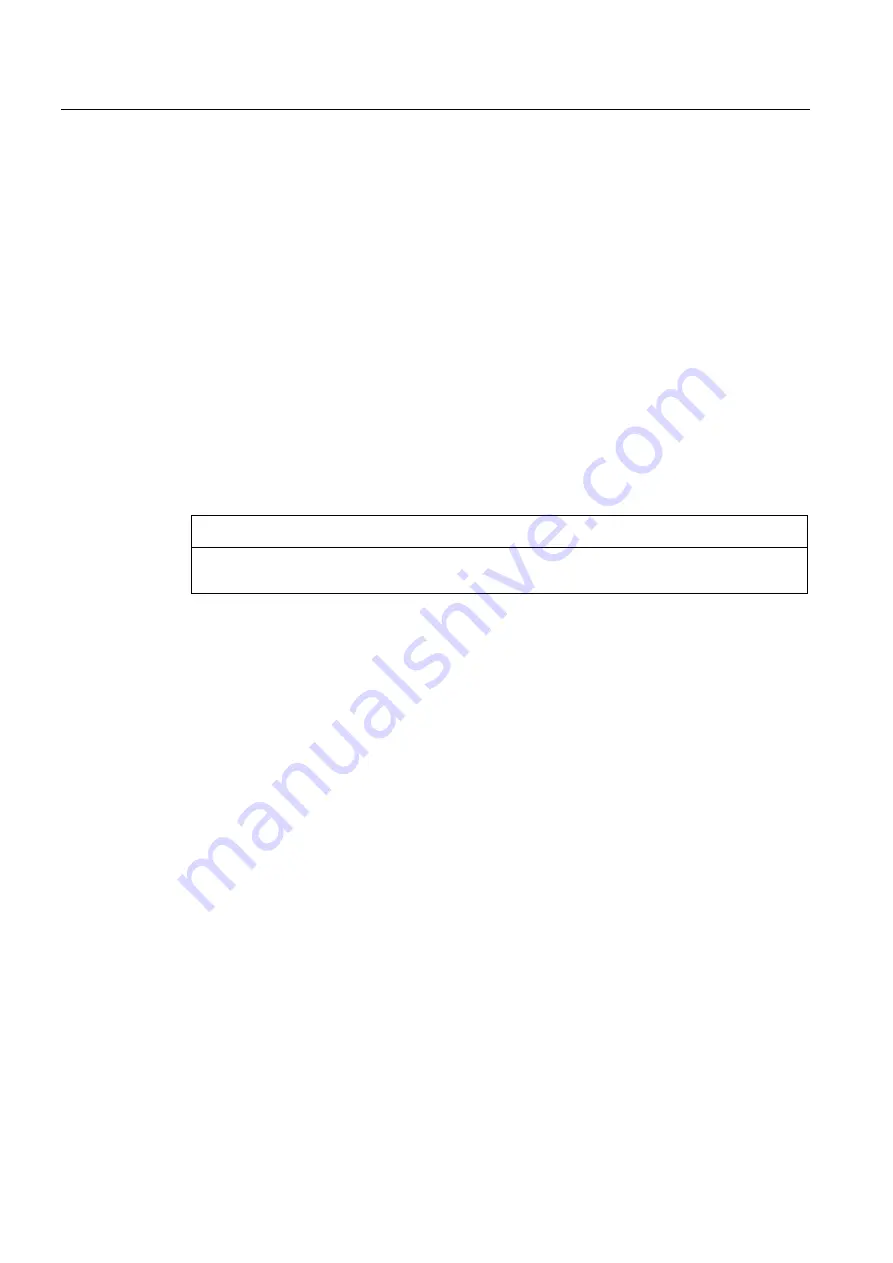
Mechanical properties of the motors
3.1 Cooling
1PM6/1PM4 Hollow-Shaft Motors for Main Spindle Drives
42
Configuration Manual, PPMS, 04/2008, 6SN1197-0AD23-0BP0
3.1.4
Coolant gland
The rotary gland for the coolant must be mounted at the non-drive end shaft centering
(screwed) - refer to the following diagrams.
The rotary gland is mounted carefully following the manufacturer's specifications.
●
GAT (Gesellschaft für Antriebstechnik mbH)
Schoßbergstr. 19, 65201 Wiesbaden, Germany
●
DEUBLIN GmbH,
Nassaustrasse 10, 65719 Hofheim, Germany
●
Ott-Jakob Spanntechnik GmbH
Industriestrasse 3-7, 87663 Lengenwang, Germany
For the 1PM6 series with mounted axial fan, the fan plus the adapter must be removed to
install the rotary gland. A recess/cut-out must be made in the adapter (intermediate housing)
to feed in the coolant. This opening must be clean.
NOTICE
When mounting the rotary gland, it must be ensured that the thread is tightly screwed into
the non-drive shaft end so that no coolant can leak.