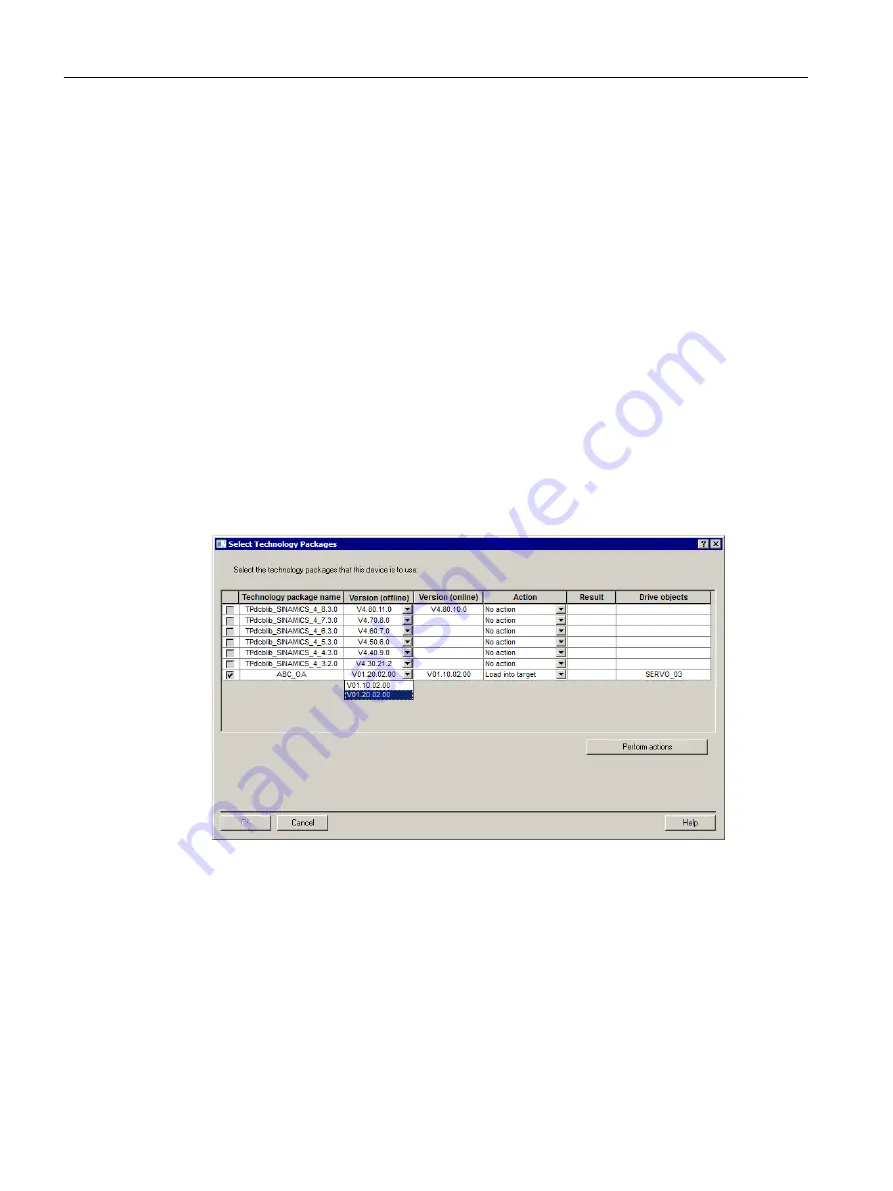
4.3.3
Download the technology package for the new version
In the following, the Technology Extension ABC_OA with version V1.2 is loaded into the device
via STARTER.
Requirements
The following requirements must be met before downloading:
1. A project matching the device is open.
2. The STARTER commissioning tool is in ONLINE mode.
Procedure
To download, proceed as follows:
1. Right-click the drive unit in the project navigator.
2. Click "Select technology packages" in the shortcut menu.
The "Select technology packages" window opens.
3. For technology package "ABC_OA", select version V01.20.02.00 under the column
"Version (offline)".
Figure 4-6
Selecting the technology package version
4. For the technology package "ABC_OA", set the action "Load to target device"
5. Click the "Perform actions" button.
6. Confirm the message that the existing technology package should be overwritten.
After successfully performing the action, the information "OK" is displayed for the
corresponding "Result" field.
Version V01.20.02.00 is now used on the drive device.
7. To activate the Technology Extension for the drive object, perform the project download.
Set the mode to ONLINE and select "Download Project to Target System".
Installation and activation
4.3 Upgrading using STARTER or SIMOTION SCOUT
RAILCTRL
26
Function Manual, 09/2019, A5E38120767B
Summary of Contents for SINAMICS RAILCTRL
Page 1: ...Function Manual Rail Control RAILCTRL Edition SINAMICS 09 2019 www siemens com drives ...
Page 2: ......
Page 14: ...Safety instructions 2 3 Industrial Security RAILCTRL 12 Function Manual 09 2019 A5E38120767B ...
Page 104: ...Index RAILCTRL 102 Function Manual 09 2019 A5E38120767B ...
Page 105: ......