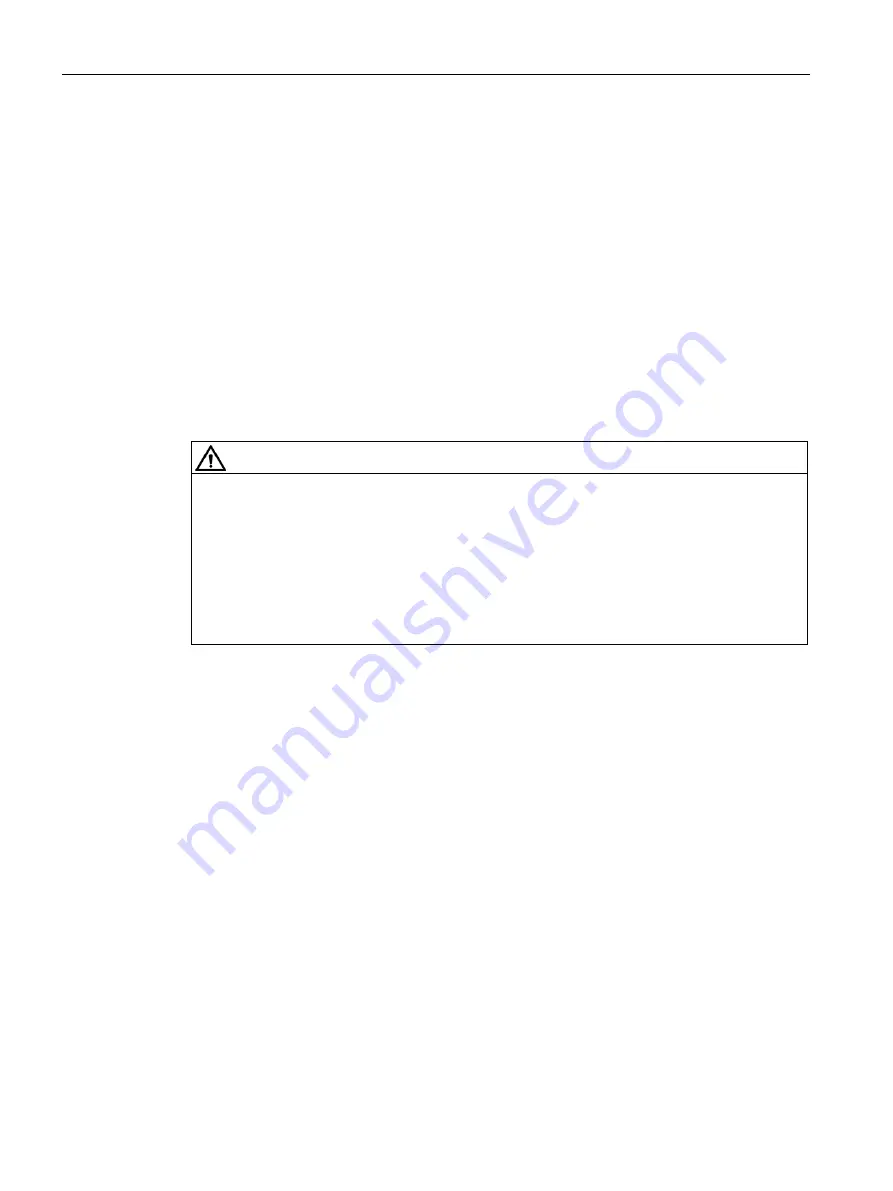
Electrical connection
6.6 Motor connection
Installation and Operating Instructions SINAMICS G180
100
Operating Instructions, 02/2019, 4BS0751-007
6.6.4
Dimensioning motor cables
●
Voltage load
Use cables with at least U
0
/U = 0.6 kV/1 kV.
●
Current load
–
Dimension the cable cross section according to the applicable standards, e.g.
VDE 0298.
–
Determine the current of the motor cable according to the converter output current,
which you can find on the rating plate.
●
Use shielded mains power cables or cables with concentric protective earth conductor,
type NYCWY, in order to comply with EMC directives.
●
For multi-system devices, connect the same number of motor cables at each system.
Note the information in section "Correct EMC installation and connection" (Page 75).
WARNING
Capacitive leakage currents
An increased current can flow in the motor cable shield as a result of capacitive leakage
currents. This can cause the cable to overheat. This can result in death, serious injury or
material damage.
Use a shield cross section that is, as a minimum, half the line conductor cross-section: For
a thinner shield or for a shield manufactured out of steel braiding, route a PE conductor,
which, as a minimum, is half of the line conductor cross-section in parallel with the motor
cable.
6.6.5
Dimensioning maximum motor cable length
The maximum cable length is determined by the following factors:
●
Peak voltage at the motor
–
All converters are equipped with a du/dt filter. The filter limits the voltage increase time
on the motor to > 0.5 µs.
–
A motor peak voltage of 1,560 V is maintained for the maximum cable lengths stated
in the table.
●
Inverter load
–
The capacitive load of the inverter increase with increasing cable length and/or
increasing number of parallel cables.
–
The parameterizable inverter clock frequency influences the converter load. If you
configure the minimum possible clock frequency , the inverter load then reduces so
that a larger cable length can be connected.