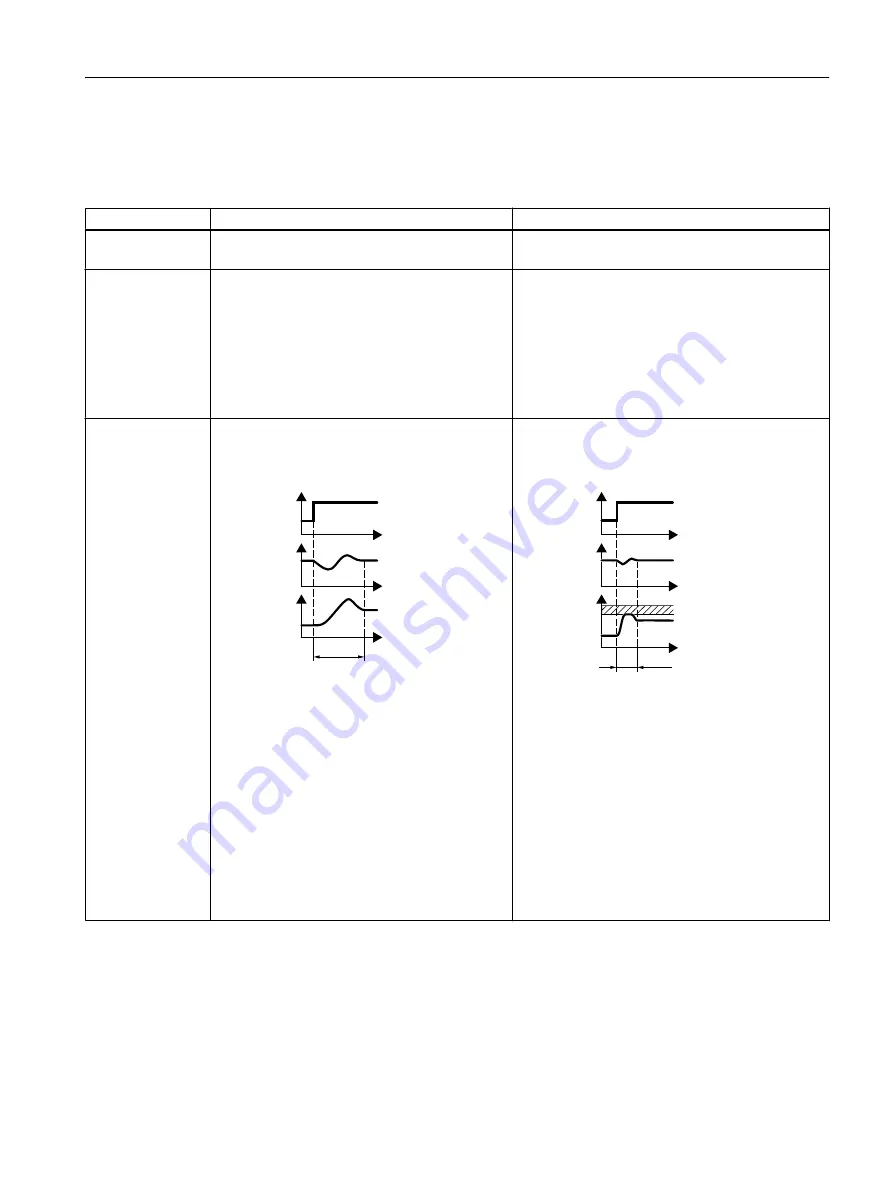
Select the suitable application class
When selecting an application class, the inverter assigns the appropriate settings to the motor
control.
Application class
Standard Drive Control
Dynamic Drive Control
Motors that can be
operated
Induction motors
Induction and synchronous motors
Application exam‐
ples
● Pumps, fans, and compressors with flow
characteristic
● Wet or dry blasting technology
● Mills, mixers, kneaders, crushers, agitators
● Horizontal conveyor technology (conveyor
belts, roller conveyors, chain conveyors)
● Basic spindles
● Pumps and compressors with displacement
machines
● Rotary furnaces
● Extruder
● Centrifuges
Properties
● Typical settling time after a speed change:
100 ms … 200 ms
● Typical settling time after a load surge: 500 ms
6SHHG
/RDG
0RWRU
WRUTXH
W
W
W
PV
● Standard Drive Control is suitable for the
following requirements:
– All motor power ratings
– Ramp-up time 0 → rated speed
(depending on the motor power rating):
1 s (0.1 kW) … 10 s (45 kW)
– Applications with increasing load torque
without load surges
● Standard Drive Control is insensitive with
respect to imprecise setting of the motor data
● Typical settling time after a speed change:
< 100 ms
● Typical settling time after a load surge: 200 ms
6SHHG
/RDG
0RWRU
WRUTXH
W
W
PV
● Dynamic Drive Control controls and limits the
motor torque
● Typically achieves a torque accuracy: ± 5 % for
15 % … 100 % of the rated speed
● We recommend Dynamic Drive Control for the
following applications:
– Motor power ratings > 11 kW
– For load surges 10 % … >100 % of the rated
motor torque
● Dynamic Drive Control is necessary for a ramp-
up time 0 → rated speed (dependent on the rated
motor power): < 1 s (0.1 kW) … < 10 s (132 kW).
Commissioning
5.4 Quick commissioning using the BOP-2 operator panel
SINAMICS G120C converter
Operating Instructions, 09/2017, FW V4.7 SP9, A5E34263257B AF
123