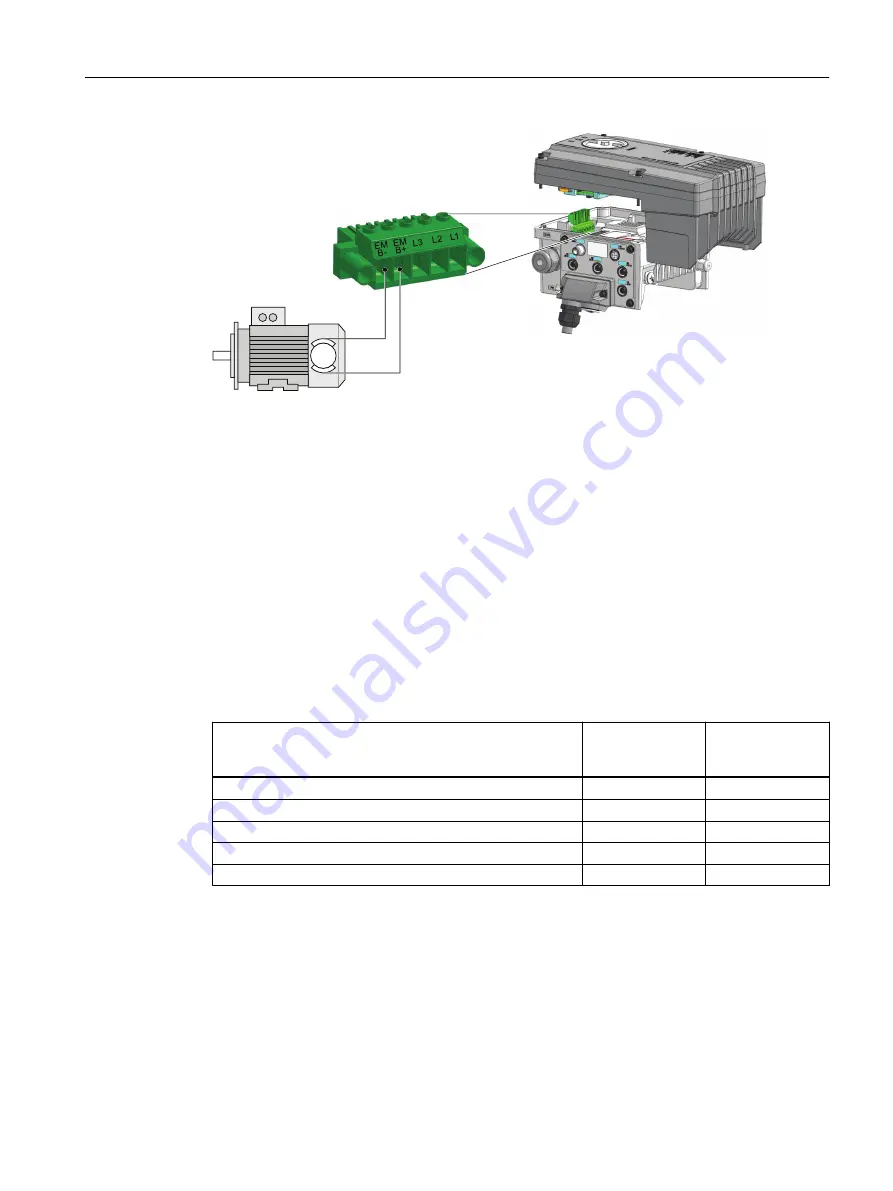
EMB+
EMB-
Figure 4-15
Simplied diagram of the motor holding brake connections
4.3.8
Connecting the PROFINET interface
Condition
The screen of the PROFINET cable must be connected with the protective earth. The solid copper
core must not be scored when the insulation is removed from the core ends.
Description
Listed in the table below are the recommended Ethernet cables.
Table 4-7
Recommended Ethernet cables and cable length
Cable type
Max. length be‐
tween 2 convert‐
ers
Article Number
Industrial Ethernet FC TP Standard Cable GP 2 x 2
100 m (328 ft)
6XV1840-2AH10
Industrial Ethernet FC TP Flexible Cable GP 2 x 2
85 m (278 ft)
6XV1870–2B
Industrial Ethernet FC Trailing Cable GP 2 x 2
85 m (278 ft)
6XV1870–2D
Industrial Ethernet FC Trailing Cable 2 x 2
85 m (278 ft)
6XV1840–3AH10
Industrial Ethernet FC Marine Cable 2 x 2
85 m (278 ft)
6XV1840–4AH10
4.3.9
Terminal assignment dependent on interface configuration
The inputs and outputs of the frequency converter and the fieldbus interface have specific
functions when set to the factory settings.
When you put the frequency converter into operation, you can change the function of each of
its inputs and outputs and the setting of the fieldbus interface.
Installation
4.3 Electrical Installation
Distributed converter for SIMOGEAR geared motors
Operating Instructions, 10/2020, FW V4.7 SP13, A5E31298649B AL
79