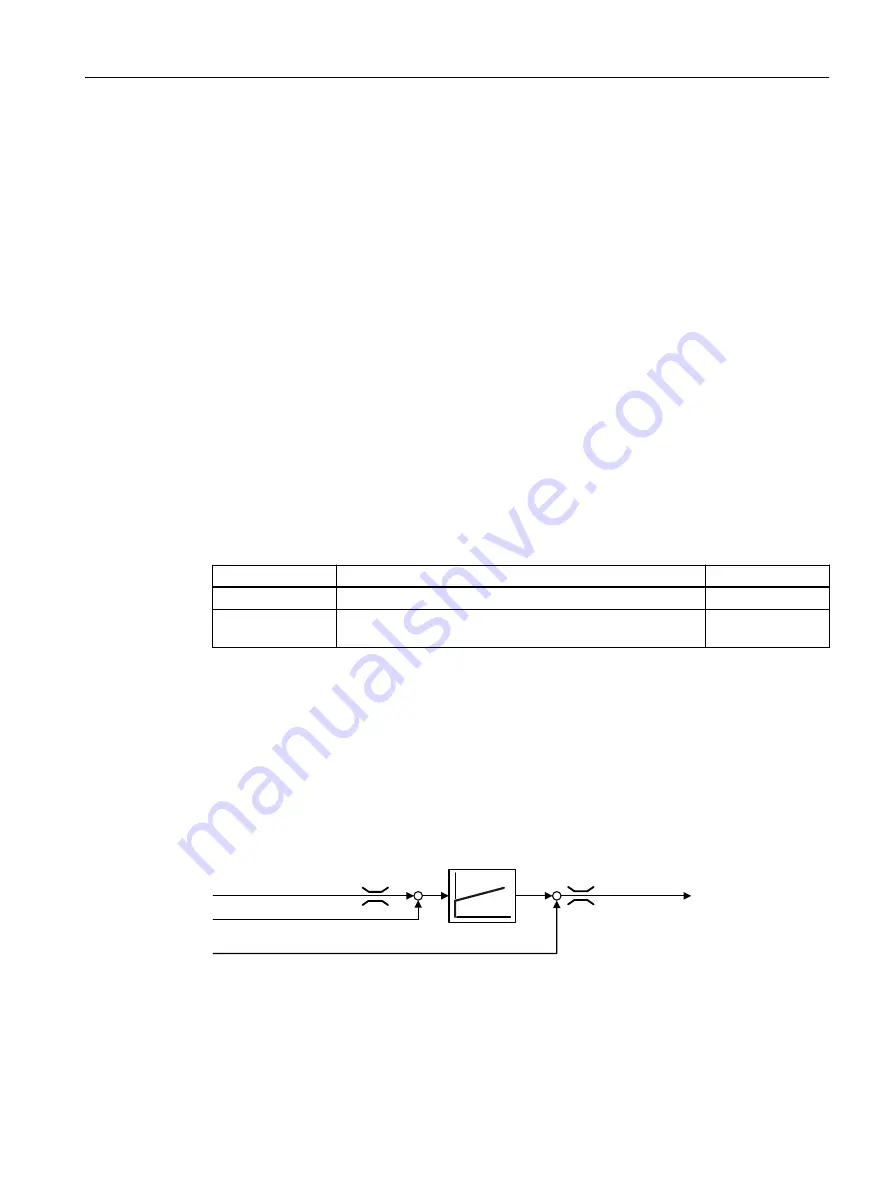
Overview
Special settings for a pulling load
For a pulling load, e.g. a hoisting gear, a permanent force is exerted on the motor, even when
the motor is stationary.
For a pulling load, we recommend that you use vector control with an encoder.
Function description
If you use sensorless vector control with a pulling load, then the following settings are required:
• Set the following parameters:
• When opening the motor holding brake, enter a speed setpoint > 0.
For speed setpoint = 0, and with the motor holding brake open, the load drops because the
induction motor rotates with the slip frequency as a result of the pulling load.
• Set the ramp-up and ramp-down times ≤ 10 s in the ramp-function generator.
• If, in quick commissioning, you have selected application class Dynamic Drive Control then
set p0502 = 1 (technological application: dynamic starting or reversing).
Parameter
Parameter
Description
Factory setting
p1610[D]
Torque setpoint static (without encoder)
50%
p1750[D]
Motor model configuration
0000 0000 0000
1100 bin
8.19.2.4
Friction characteristic
Overview
In many applications, e.g. applications with geared motors or belt conveyors, the frictional
torque of the load is not negligible.
The converter provides the possibility of precontrolling the torque setpoint, bypassing the speed
controller. The precontrol reduces overshooting of the speed after speed changes.
6SHHGVHWSRLQW
)ULFWLRQDOWRUTXH
7RUTXH
VHWSRLQW
6SHHGFRQWUROOHU
6SHHGDFWXDOYDOXH
.
3
7
1
Figure 8-56
Precontrol of the speed controller with frictional torque
The converter calculates the current frictional torque from a friction characteristic with 10
intermediate points.
Advanced commissioning
8.19 Motor control
Distributed converter for SIMOGEAR geared motors
Operating Instructions, 10/2020, FW V4.7 SP13, A5E31298649B AL
301