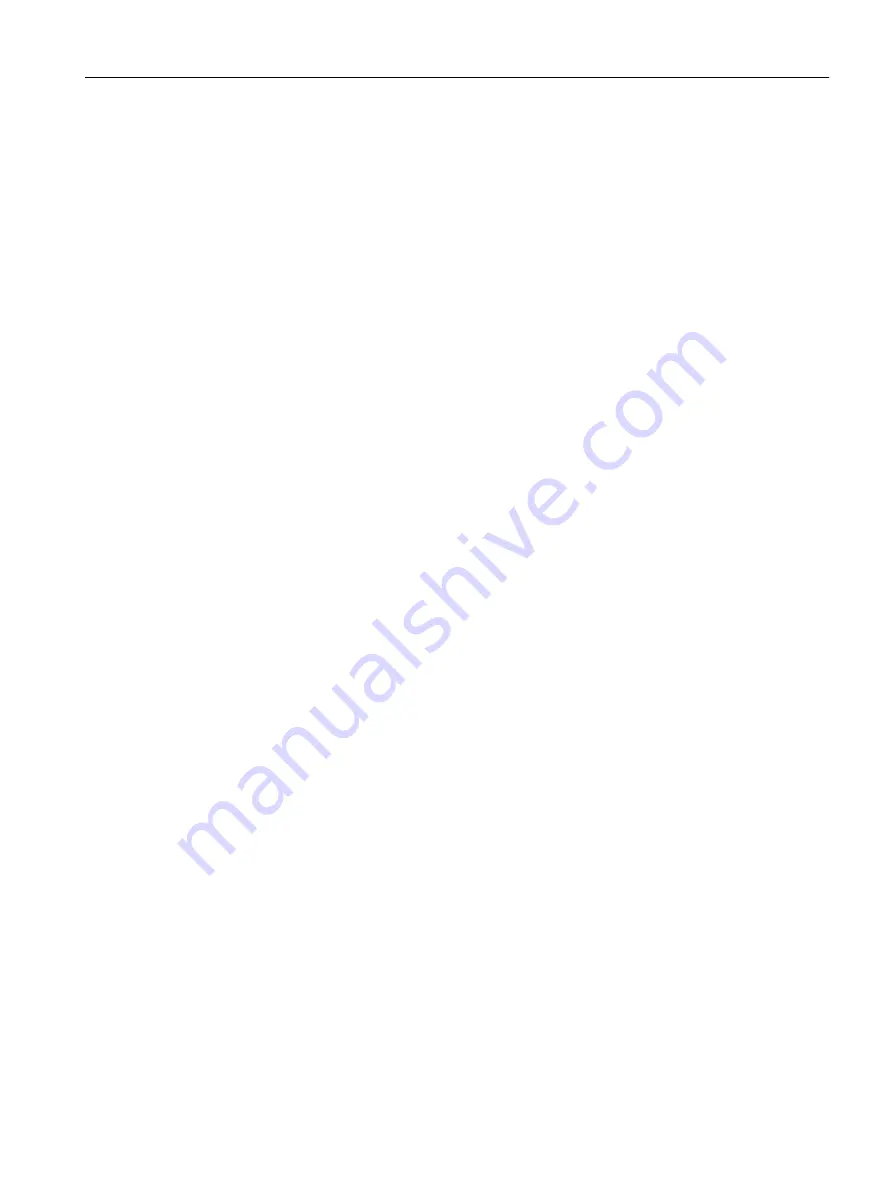
7.10
Linking an additional encoder (optional)
7.10.1
Basic principles
Using encoders
In addition to a motor encoder, additional encoders can be linked and configured:
● Additional encoders on the drive
– Encoders with DRIVE‑CLiQ interface
– Encoders connected to a CU310/CU310-2 or CUA32 via the onboard encoder interface
– Encoders connected to SIMOTION D via an SMx module
● Additional encoders on SIMOTION D
– Encoders connected via PROFIBUS
– Encoders connected via PROFINET
Configuring additional encoders
The additional encoder can be used in SIMOTION, for example, as:
● Machine encoder (second encoder = direct measuring system)
A direct measuring system measures the technological parameter directly, i.e. without the
interference of influences such as torsion, backlash, slip, etc. This can facilitate improved
smoothing of mechanical influences by means of the closed-loop control. If you use a
second encoder as a machine encoder, you can work with the encoder changeover
function.
● External encoder
You can use the external encoder to record an external master value, for example.
● Encoder for hydraulic axes
● Encoders for the implementation of cam controllers
7.10.2
Additional encoders on the drive
The following options are available for configuring additional encoders on the drive:
● Configuration of a second encoder on the drive
● Configuration of an encoder as drive object (as of SINAMICS firmware V4.3)
The following options are available for configuring additional encoders on the drive.
Commissioning (software)
7.10 Linking an additional encoder (optional)
SIMOTION D4x5-2
Commissioning and Hardware Installation Manual, 03/2018, A5E33441636B
275