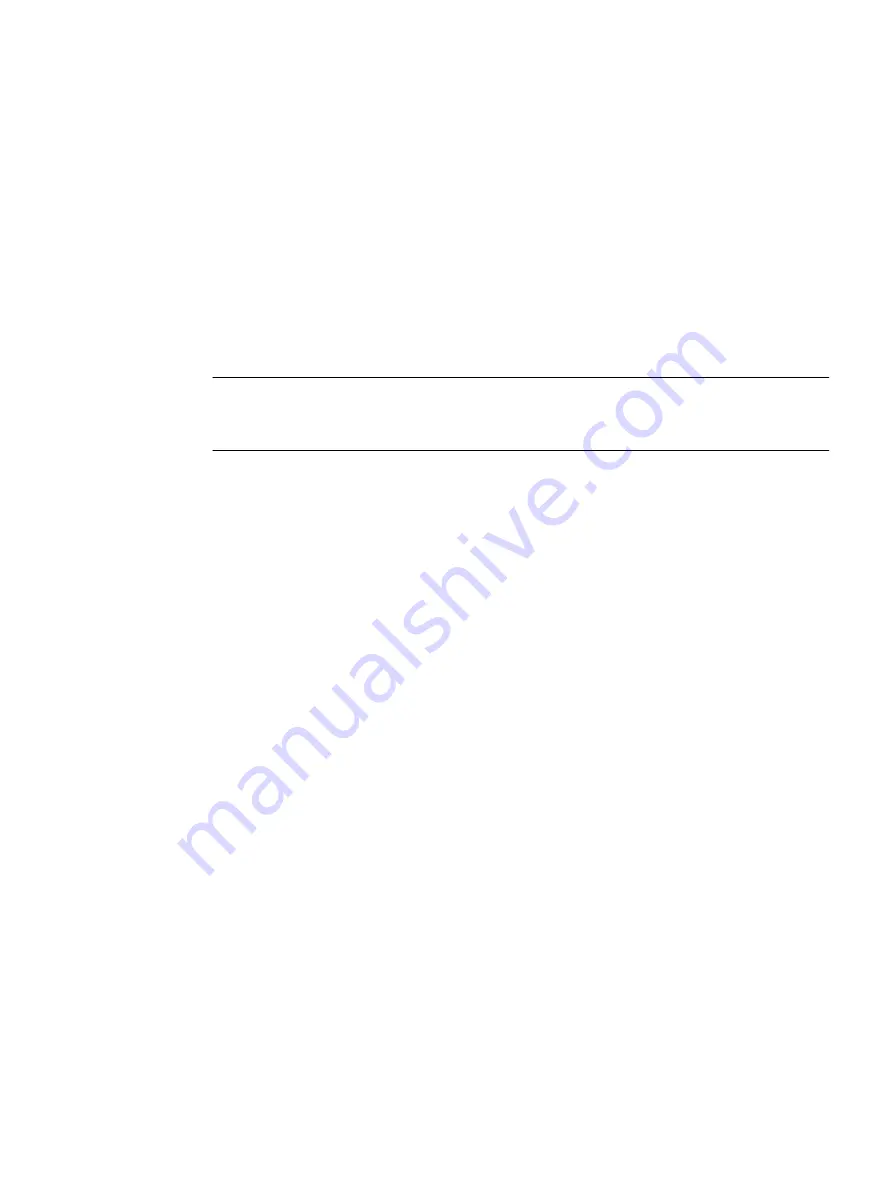
Commissioning
7
Observe the following when carrying out any work on the machine:
• Comply with the general safety instructions (Page 11).
• Comply with the applicable national and sector-specific regulations.
• When using the machine within the European Union, comply with the specifications laid
down in EN 50110‑1 regarding safe operation of electrical equipment.
Note
Service Center
Please contact the Service Center if you require commissioning support.
Danger to life as a result of the converter voltage
As long as the feeding converter is switched on, or the DC link of the converter is not discharged,
there can be a voltage at the motor terminals even when the rotor is not moving. Depending on
the converter type, the voltage is up to 1000 V. When coming into contact, this can result in
death, serious injury, and material damage.
• Maintain the five safety rules (Page 11)at all times when operating the machine.
Damage caused by the short-circuit current
When the permanent magnet rotor is a driven, a voltage ("rotor voltage") is induced in the stator
winding, that can be measured at the motor terminals. If a cable or converter short-circuit
simultaneously occurs, then a short-circuit current is driven by the induced rotor voltage. This
can result in material damage.
• Use cables that are short-circuit proof.
• Alternatively, use a circuit breaker close to the motor to protect the cable against a short
circuit.
7.1
Measures before commissioning
7.1.1
Checks to be carried out prior to commissioning
The following list of checks to be performed prior to commissioning does not claim to be
complete. It may be necessary to perform further checks and tests in accordance with the
specific situation on-site.
1FZ shaft height 280
Operating Instructions, 02/2022, A5E51698698A
77
Summary of Contents for SIMOTICS DP
Page 2: ......
Page 140: ...Index 1FZ shaft height 280 138 Operating Instructions 02 2022 A5E51698698A ...
Page 141: ......