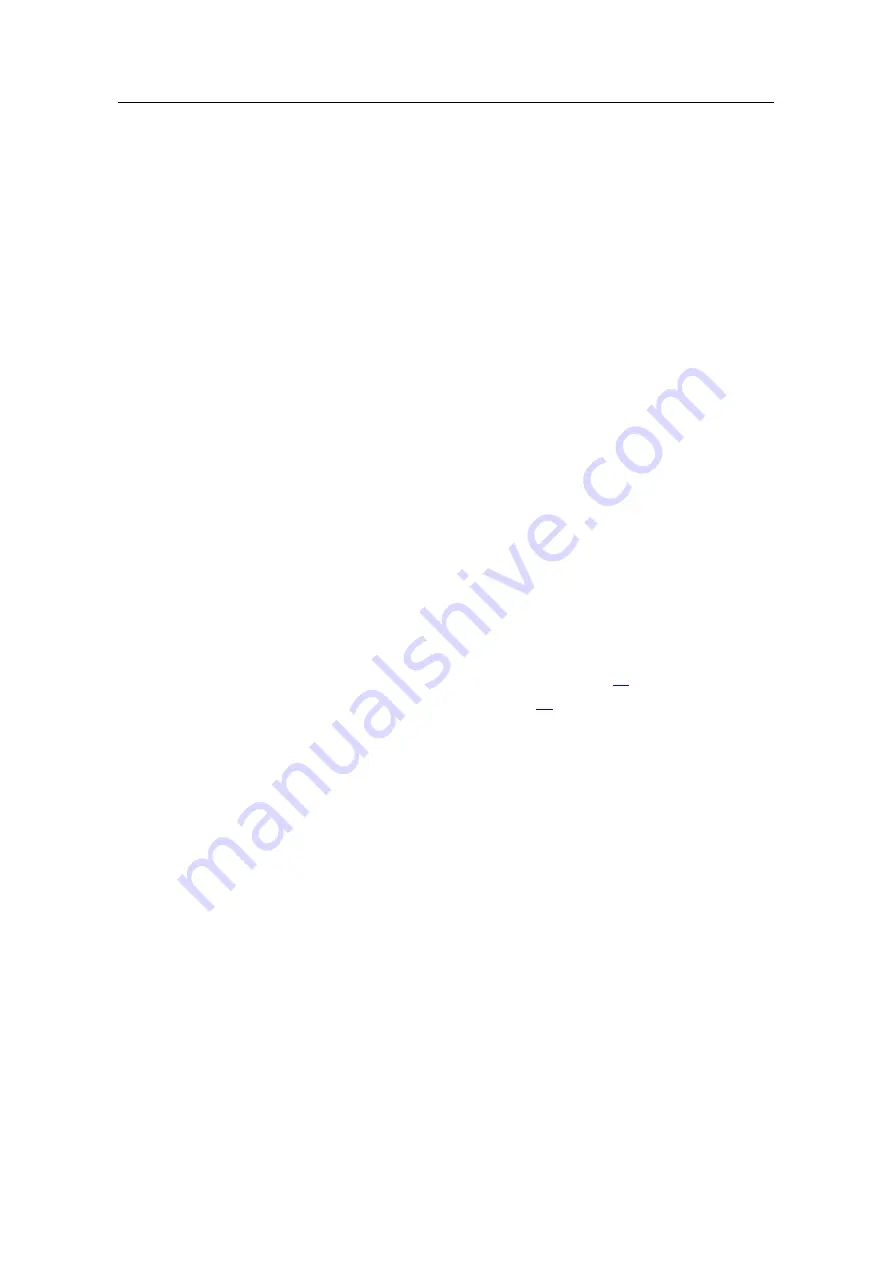
2 Operating principle
Blocking Protection for Pumps with SIMOCODE pro V
Article ID: 109478058, V2.0, 09/2020
13
©
S
iem
e
n
s A
G
2020
A
ll r
igh
ts
re
se
rv
e
d
2.2.2
Detecting faults in the conveying flow
In normal operation, the pump motor runs in a nominal range proportional to its
torque. Depending on the specific type of application in the process, a value that is
either under or over the nominal range can be a proxy for a pumping problem. Both
a significant overload along with, at worst, a complete blockage of the motor, as
well as a serious absence of motor load up to and including running dry, can be
interpreted as a fault. In order to record this, the application example measures the
motor current and voltage indicators. Based on the phase shift, the
SIMOCODE pro V PN basic unit finds the power factor.
By looking at motor current and power factor, a conclusion is made about a
disturbance in the conveying flow. In the overload range, the motor current rises
disproportionately fast, such that it can be justifiably included as a shut-off criterion
due to its steep characteristic curve. In the underload range, on the other hand, the
power factor has a steep characteristic curve trend and in this context it is more
suitable than the motor current as a shut-off criterion.
The logic in the SIMOCODE pro V PN basic unit detects a problem in the pumped
flow if one of the following conditions is met:
•
The value of the motor current leaves a defined nominal range, defined by limit
monitors 2 (value not met) and 3 (value exceeded) (inputs 1 and 2 of truth
table TT9).
•
The value of the power factor falls below a defined threshold, which is defined
by limit monitor 4 (input 3 of truth table TT9).
The three limit monitors are parameterized in such a ways that they only respond if
the following conditions are met:
•
The motor is running.
•
The start sequence is complete. This means that the limit monitors only
respond after the class time runs out that you set when parameterizing the
overload protection under "Parameters > Motor protection". Detailed
information about the Trip class can be found in manual
•
There is no test position (RMT) (see manual
The disturbance is only evaluated if the drive is running in the direction of flow, i.e.
if the value is "true" at socket "QE1" of the function block "Protection/Control"
(input 5 of truth table TT9).
In the mode "Local 2" (i.e. operation "on site" or via operator panel) you can enable
or disable handling of the disturbance with Button 1 of the operator panel. In
"Remote" mode, disturbance handling is activated via bit 0 of the interface "Cyclic
receive Byte 1". The interconnection of Counter 2, signal conditioning 3 and truth
table TT4 are used for this purpose.
The interference signal is available at output 1 of truth table TT9 for further
processing.