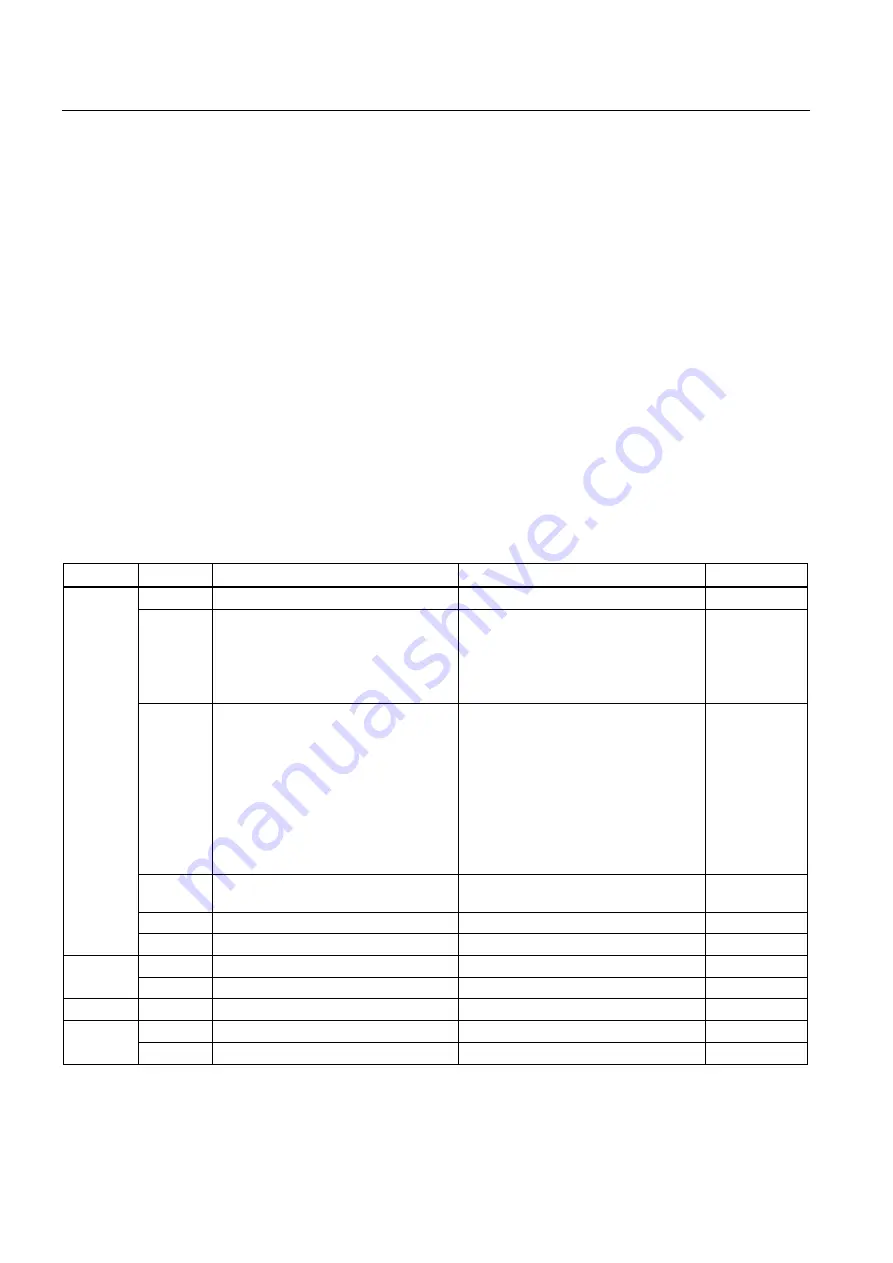
Errors and diagnostics
11.5 Operator error
Counter module FM 450-1
110
Manual, 02/2014, A5E03648739-02
Diagnostic Data Records DS0 and DS1
The information as to which event triggered a diagnostic interrupt is stored in diagnostic data
records DS0 and DS1. Diagnostics data record DS0 consists of 4 bytes; DS1 consists of
12 bytes, the first 4 bytes of which are identical to DS0.
Reading the data record from the module
Diagnostic data record DS0 is automatically transferred to the start information when the
diagnostic OB is called. These four bytes are stored there in the local data element
(bytes 8-11) of OB 82.
You can read out the diagnostic data record DS 1 and hence also the contents of DS0 from
the module using FC DIAG_INF. This is only useful if DS0 signals an error in one channel.
Assignment of the Diagnostic Data Record DS0 and the Start Information
The table below shows the assignment of the diagnostic data record DS0 in the start
information. All bits not listed have no meaning and are zero.
Table 11- 1 Assignment of diagnostic data record DS0
Byte
Bit
Meaning
Remark
Event no.
0
0
Module error
Is set at each diagnostic event.
8:x:00
1
Internal error
Is set for all internal faults:
•
Fault in RAM TEST
•
Watchdog timeout
•
Lost hardware interrupt
8:x:01
2
External error
Is set for all external faults:
•
Auxiliary voltage 1L+/1M is not
connected or 5.2 VDC encoder
supply is short circuited
•
5.2 VDC encoder supply short
circuited or overloaded.
•
5V signals faulty
•
Faulty parameter assignment
8:x:02
3
Error in one channel
1 is always assigned for internal and
external faults.
8:x:03
4
External auxiliary voltage faulty
8:x:04
7
Faulty parameter assignment
8:x:07
1
0 ... 3
Type class
Always assigned with 8.
4
Channel information
Always assigned with 1.
2
3
Watchdog timeout
8:x:33
3
3
RAM defective
8:x:43
6
Hardware interrupt lost
8:x:46
Summary of Contents for simatic s7-400 FM 450-1
Page 8: ...Table of contents Counter module FM 450 1 8 Manual 02 2014 A5E03648739 02 ...
Page 120: ...Spare parts Counter module FM 450 1 120 Manual 02 2014 A5E03648739 02 ...
Page 122: ...References Counter module FM 450 1 122 Manual 02 2014 A5E03648739 02 ...
Page 126: ...Glossary Counter module FM 450 1 126 Manual 02 2014 A5E03648739 02 ...
Page 130: ...Index Counter module FM 450 1 130 Manual 02 2014 A5E03648739 02 ...