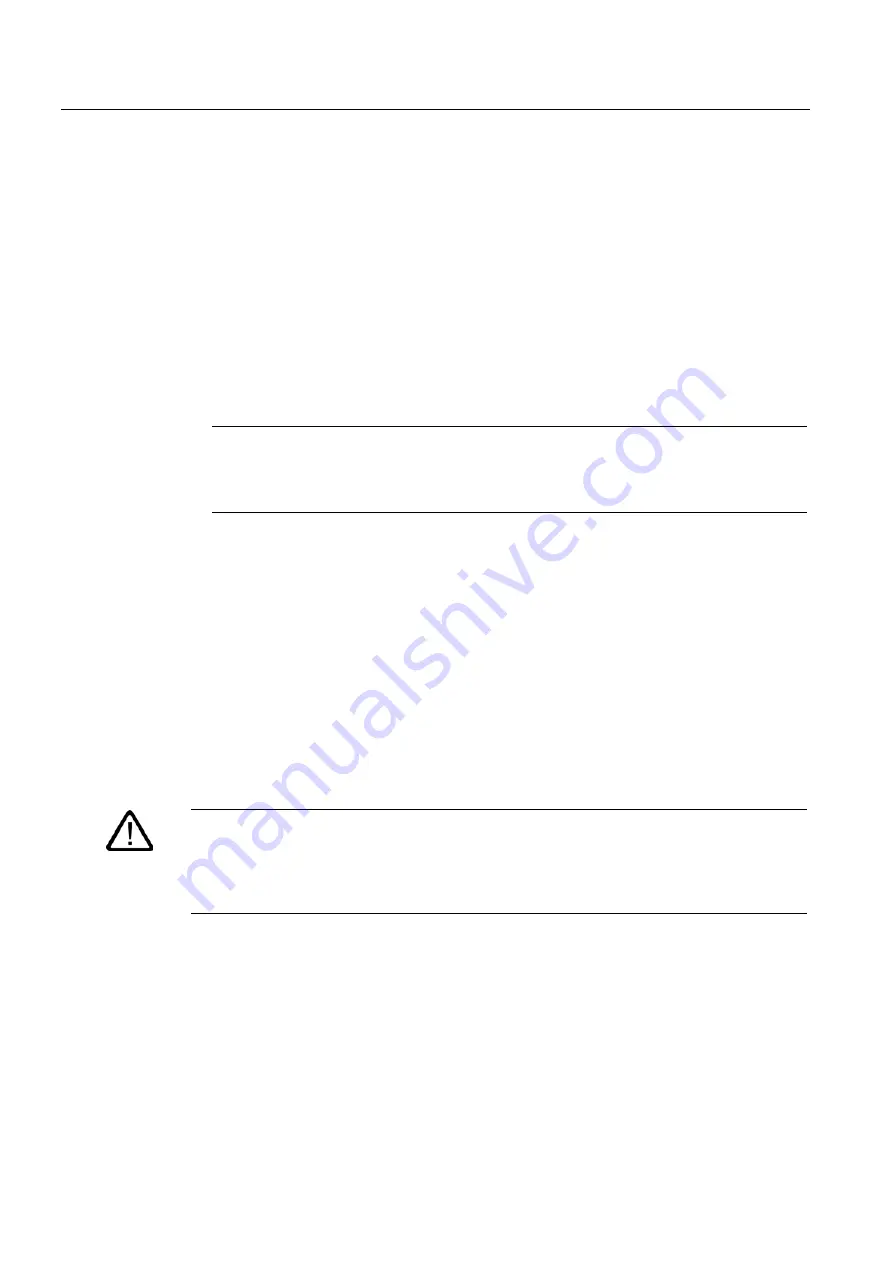
Debugging functions, diagnostics and troubleshooting
10.2 Overview: Debugging functions
S7-300, CPU 31xC and CPU 31x: Installation
10-2
Operating Instructions, Edition 08/2004, A5E00105492-05
Debugging functions of the software: Monitoring and modifying variable, stepping mode
STEP 7 offers you the following testing functions you can also use for diagnostics:
•
Monitoring and modifying variables
Can be used for PG/PC monitoring of specific CPU or user program variables. You can
also assign constant values to the variables.
•
Testing with program status
You can test your program by viewing the program status of each function (result of
logical links, status bit) or the data of specific registers in real-time mode.
For example, if you have selected the programming language LAD in STEP 7 for your
presentation, the color of the symbol will indicate a closed switch or an active circuit.
Note
The STEP 7 testing function with program status extends the CPU cycle time! In STEP 7
you can customize the maximum permitted increase in cycle time (not for CPU 3182
DP). In this case, set process mode for the CPU parameters in STEP 7.
•
stepping mode
When testing in single-step mode, you can process your program instructions in
sequence (= single-step) and set break points. This is only possible in testing mode and
not in process mode.
Debugging functions of the software: Forcing variables
The Force function can be used to assign the variables of a user program or CPU (also:
inputs and outputs) constant values which can not be overwritten by the user program.
For example, you can use it to jumper sensors or switch outputs permanently, irrespective of
the user program.
Danger
This could result in severe injury or even death, and damage to property.
Incorrect use of the Force function could result in death or severe injury, and damage to
machinery or even the entire plant. Always follow the safety instructions in the
STEP 7
manuals.